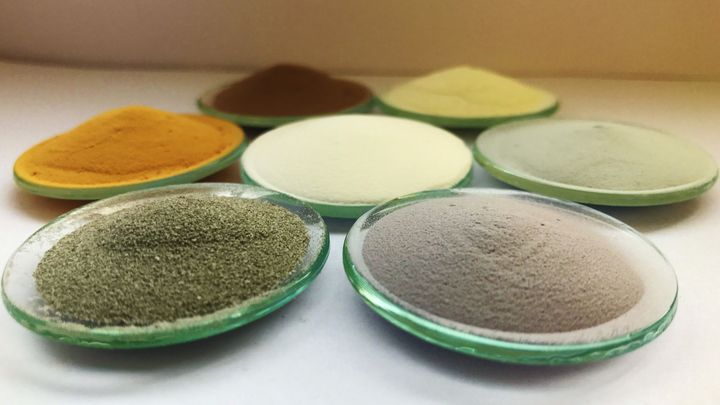
Researchers at the University of Duisburg-Essen have developed a way to generate colors during SLS 3D printing processes.
SLS 3D Printing
SLS 3D printing is not a new technology; it’s been around for decades, but still forms a strong base from which industrial products are produced and prototyped. The essence of the SLS process is that a powerful laser beam sweeps across a flat bed of powder, selectively fusing the particles together. After an application of another thin layer of powder, the process repeats until the object is fully built.
SLS has several great attributes, including the ability to produce very strong parts in high detail. SLS prints typically have smooth surfaces, making it an excellent choice for prototyping. Typically nylon powders are used in SLS print jobs.
But there’s a problem.
SLS Color Problem
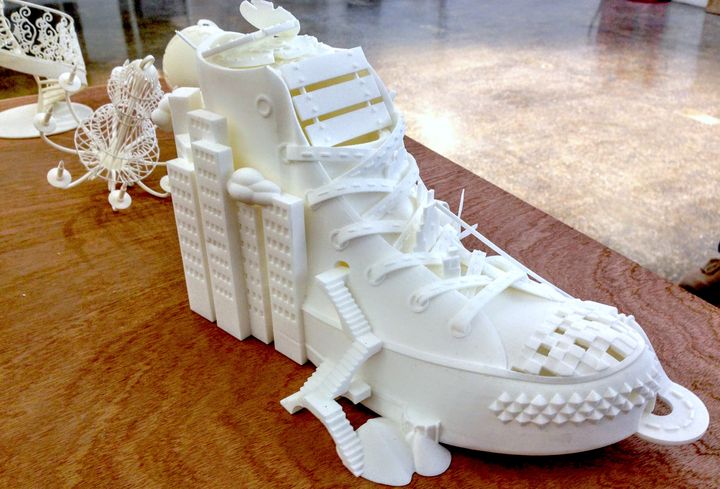
You may have noticed that virtually all SLS 3D prints are either white or black in color. This is because the normally white powder requires very high energies to cause fusion to occur: the white color reflects most of the light!
That is the reason SLS systems typically are high-priced: they require expensive high-power laser systems to achieve those energy levels.
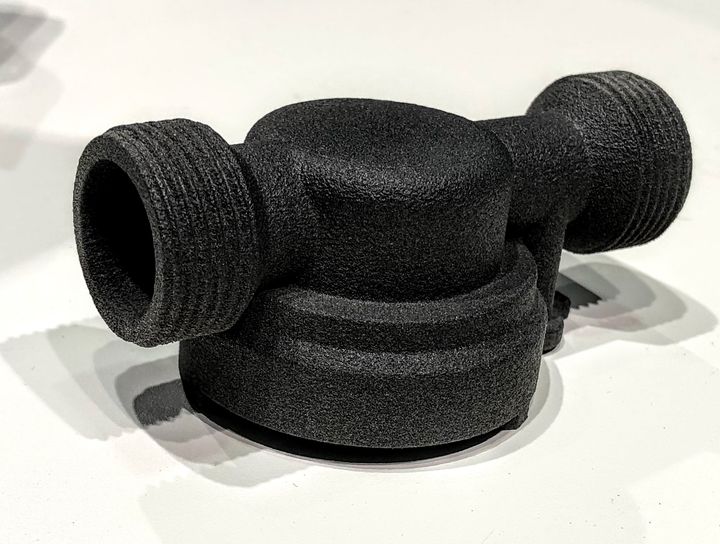
But wait, you say, there are several less-expensive SLS 3D printers on the market. Indeed, this is true. In those devices, the lower cost is achieved by using relatively low-power laser components. How do they get away with lower energies? The trick is to use black powder, which is designed to absorb more energy from the weaker lasers.
This is why you get black or white SLS 3D prints.
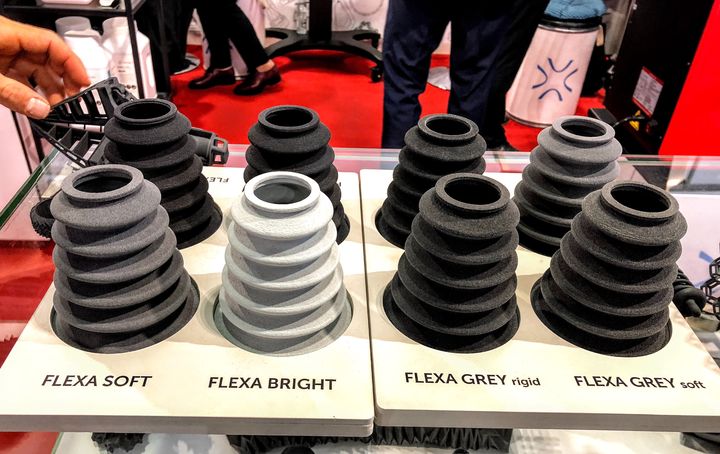
Plasmonic Nanoparticles In SLS
The researchers wanted to find a way around this problem, which is one of both color and energy levels, and it seems they have succeeded.
Their approach is to dope the powder with a very small amount of plasmonic nanoparticles.
Hold on, what the heck are “plasmonic nanoparticles”? Wikipedia explains:
“Plasmonic nanoparticles are particles whose electron density can couple with electromagnetic radiation of wavelengths that are far larger than the particle due to the nature of the dielectric-metal interface between the medium and the particles: unlike in a pure metal where there is a maximum limit on what size wavelength can be effectively coupled based on the material size.
What differentiates these particles from normal surface plasmons is that plasmonic nanoparticles also exhibit interesting scattering, absorbance, and coupling properties based on their geometries and relative positions.”
In other words, these are particles that can react when energized in different ways. And that’s the property the researchers attempted to leverage.
Dr. Bilal Gökce explains:
“Since the nanoparticles sit firmly on the surface of the powder grains and are not just mixed in, just a pinch of them produces an even color. And what works with silver also works with nanoparticles made from other elements, so that there are no limits to the colors in this process. As a bonus, there are other characteristics of the particles such as the antibacterial effect of silver or the magnetic properties of iron oxide.”
It seems they may have solved the long-awaited issue of SLS colors by using these special nanoparticles. It may thus be possible, for example, to eventually purchase a tub of “red” SLS powder, and expect it to work efficiently during SLS operations.
It may also mean the possibility of lower-cost SLS systems overall. If lower energies are all that’s need for these special powders, then the cost of SLS 3D printers should correspondingly drop. That could open up new markets for the technology, which has largely been limited to big operations and service bureaus.
This development does not mean there is a way for an SLS system to print in multiple colors, however.
That is a problem for another day.
Via University of Duisburg-Essen (German) and Wiley (Hat tip to Benjamin)