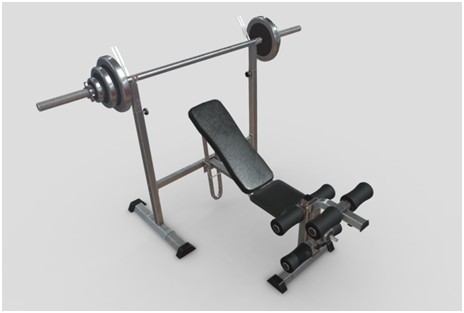
Charles R. Goulding and Adam Friedman pump up the use of 3D printing to take a look at gym equipment.
The health club market is worth $96.7 billion globally and has grown each year since 2008. In 2019, U.S. gym industry revenue increased to $35 billion.
In 2020, things changed. During the pandemic, gyms could not be accessed and even now the public is concerned about returning to gyms. Those gyms that have reopened have reduced member occupancy limits and often prohibit locker room and shower usage. The existing supply chain could not meet the demand for home use weight training equipment, which is also costly and unwieldy to ship.
3D printing is primed to enter the weight training equipment market. 3D printing can create weights and could strengthen the manufacturing of weight training equipment.
Metal fabrication is just one ability of 3D printers. Most home weights, usually in the form of dumbbells, are made of cast iron and stainless steel. The machining process to create structures for dumbbells, free weights, and barbells requires skilled machinery and sometimes machine shop processes that have production order times in the range of weeks or months. Fabricated weights need to have the correct geometry and shape so they can withstand the forces and loads they undergo while being utilized and handled. This requires skilled design and highly professional metal fabrication. Using a 3D printer for metal fabrication can emulate the comprehensiveness of metal shop production. After all, 3D printing technology has already been used to produce large structures made of metal powders or filaments.
A huge spike in demand for weight equipment during social isolation brought on by the novel coronavirus shows that weights cannot be produced in the short amount of time that it is being demanded by individual consumers. Another trend being seen is that weights are becoming technologized, adapting to consumer demand to make weights adjust to different physical forces for specialized exercises. Weights are also now being produced in never seen before large sizes for powerlifting and modern sporting competitions such as Strongman.
3D printing is the right candidate to provide relief for these heavy and unique customer demands. Large orders for home use dumbbells, kettlebells, or squat rack equipment can be a relatively easy and profitable endeavor for a 3D print shop. For heavy lifting equipment, such as heavy chains and oversized hexagon bars, CAD modeling would easily create 3D representations of typical equipment. The added ability of CAD software to customize the shape of metal allows for greater ability to experiment with printing rare lifting equipment like handle barred Atlas Stones or weighted vests.
Fitness, in and of itself, is becoming highly technologized. Many gym-goers use simple mechanical equipment such as wedges and step trainers to work out different muscle groups and/or add resistance to an exercise. Some modern exercises, such as battle ropes, require bolts and rings that fit ropes into anchoring stations. Forearm exercises that require wide grips use thickened and grooved handles that specifically target the forearm muscle and wrists. 3D printing can create customize models for this equipment and produce these structures in a matter of hours with different types of filament and materials.
Many gym-goers are not ready to work out using communal fitness equipment. While there is cleaning in place to sanitize equipment at most gyms, many individuals feel that benches and squat racks are better in places where there are no other users of the equipment. As a result, benches and squat racks will be more highly demanded in years to come. The sophisticated, yet well-publicized and documented modeling of equipment from classic companies such as Weider Gym Equipment and NordicTrack, can lead to creating 3D models from documents and eventually 3D printed equipment. Sizing and poling the fits can be optimized with 3D printing software where novel engineering and ingenuity can lead to fabricated benches and racks with grab and push assemblies, among other consumer-friendly assembly methods that can be engineered.
The Research and Development Tax Credit
Whether it’s used for creating and testing prototypes or for final production, 3D printing is a great indicator that R&D Credit eligible activities are taking place. Companies implementing this technology at any point should consider taking advantage of R&D Tax Credits.
Enacted in 1981, the now permanent Federal Research and Development (R&D) Tax Credit allows a credit that typically ranges from 4%-7% of eligible spending for new and improved products and processes. Qualified research must meet the following four criteria:
- Must be technological in nature
- Must be a component of the taxpayer’s business
- Must represent R&D in the experimental sense and generally includes all such costs related to the development or improvement of a product or process
- Must eliminate uncertainty through a process of experimentation that considers one or more alternatives
Eligible costs include US employee wages, cost of supplies consumed in the R&D process, cost of pre-production testing, US contract research expenses, and certain costs associated with developing a patent.
On December 18, 2015, President Obama signed the PATH Act, making the R&D Tax Credit permanent. Beginning in 2016, the R&D credit has been used to offset Alternative Minimum Tax (AMT) for companies with revenue below $50MM and, startup businesses can obtain up to $250,000 per year in payroll tax cash rebates.
Conclusion
The current pandemic has indelibly changed the exercise equipment industry. In particular, exercise equipment is being more highly demanded. 3D printing such exercise equipment can help keep up with the demand.