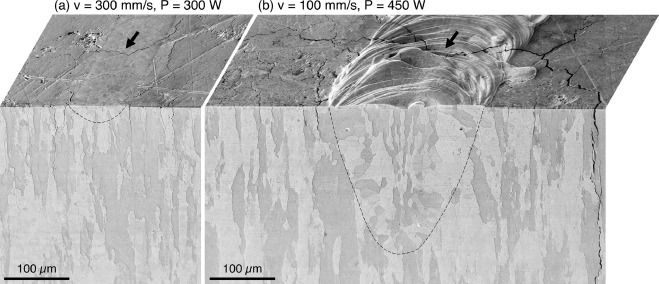
Researchers have found a way to directly observe micro-cracking of 3D printed tungsten metal.
3D Printed Tungsten
Tungsten is a very unique metal that could become a lot more important in the future. Its claim to fame is that among commonly available materials it has the highest heat resistance — 3420C, fantastically hotter than many other metals.
Because of this incredible heat resistance, it is desired to use tungsten in hot applications. One particular application that’s expected to become widespread later this century is in nuclear fusion reactors.
Fusion is the same process that takes place on our sun to generate energy by “fusing” two atoms together. In the process, tremendous amounts of energy are released that far exceed today’s nuclear fission operations. If successful, fusion reactors could provide near limitless power on Earth and perhaps even open up the solar system with new fusion-powered spacecraft.
The problem is that fusion occurs only at extraordinarily high temperatures and pressures. To do so one must build a fusion chamber to contain a hot plasma in which those conditions exist. The chamber’s “fusion-facing” elements must be made of the toughest material around, and that’s going to be tungsten.
The tungsten parts must be made perfectly and cannot have flaws, such as micro-cracks, which reduce the effectiveness of the parts.
But how do these micro-cracks develop?
Ductile-to-Brittle Transition
It turns out cracks can generate during what’s called the “ductile-to-brittle” transition. That is when the material cools sufficiently to transform from a slightly bendable state to a firmly rigid state. The micro-motions during that transition can pull material away and thus create cracks.
The accumulation of these “DBT” cracks over an entire part can compromise the part’s strength.
Apparently they occur quite rapidly when 3D printing using the PBF process, as the laser passes over the powder layer. The cracks can develop within 10ms of being heated, making it very challenging or even impossible to correct using dynamic print parameter adjustments.
Observing DBT
The researchers were able to use an advanced camera system to actually record this micro activity as it happened. Their camera, which has an astonishing 50kHz frame rate (that’s kHz, not Hz), had a resolution of 768 x 328 pixel resolution. This allowed them to see activity within a 0.620 x 0.265 mm zone.
Here is a frame showing the trail of a laser over a tungsten powder bed, and I’m sure you’ve never seen anything quite like this:
They say:
“For the first time, the ductile-to-brittle transition (DBT) in tungsten was directly visualized through a combined approach of thermomechanical modeling and in situ high speed video of microcracking during laser melting.”
The researchers then began exploring how different 3D printing parameters might affect the results. However, it seems that the issue seems far more complex than one that can solve with simple parameter changes.
Instead, this new video capability will be used to explore the problem in a great deal more detail and that, eventually, could identify the best ways to optimize tungsten — and other metals — print quality.
Via Science Direct