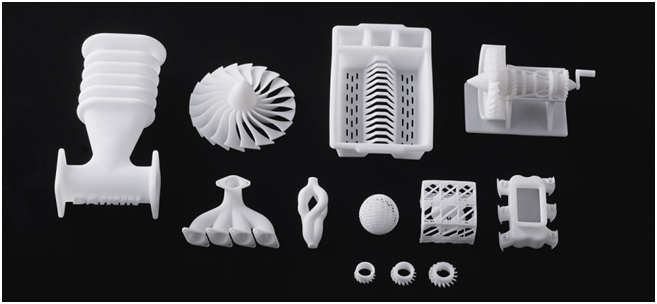
Charles R. Goulding and Mindy Zhu consider Daikin’s burgeoning usage of additive manufacturing.
On July 31, 2020, Daikin Applied announced the release of its SmartSource Dedicated Outdoor Air System (DOAS). With the COVID-19 pandemic, the need for HVAC systems that utilize 100% outside air is more present than ever. Although there are DOAS systems available, these systems are usually highly inefficient, expensive and utilize a lot of energy. Due to this, the announcement of a DOAS system that is not only cost-effective but achieves 66% higher than ASHRAE’s 90.1-2016 minimum efficiency rating blew the HVAC industry away. If this technology is possible, Daikin would show the world a whole new type of HVAC system, leading the industry into a new age of efficient HVAC systems.
Daikin
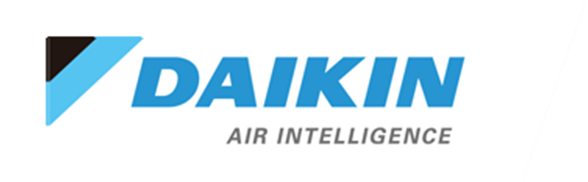
Daikin is currently the world’s leading air conditioning company; it is known for its high-quality innovations for air conditioning and heating technologies. Their key technologies include inverters and heat pumps. Inverters are utilized in HVAC systems to eliminate waste by efficiently controlling fan motor speeds. Usually, fan motor speeds for HVAC systems are running at 100% and choked to get to the speed needed. By utilizing an inverter, the fan motor speeds can be controlled without choking the air and are overall more efficient and less wasteful of energy. Heat pumps are used in the HVAC system to control the temperature of the air by transferring heat. They absorb the heat from either air, water, or ground outside and concentrate it for interior utilization. Due to this, HVAC systems with heat pumps have lower running costs, less maintenance, and are overall safer. Daikin prides itself on utilizing this technology in all of its HVAC systems and continues innovating new technologies with energy efficiency in mind.
Why the SmartSource DOAS is a Game Changer
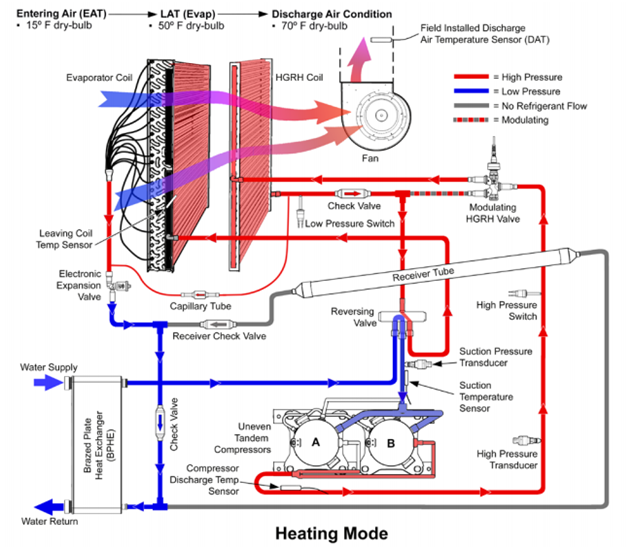
Utilizing 100% outside air for a heating and cooling system has one big issue: the heating of air utilizes a lot of energy. The air source is usually preheated by another coil before being brought to the heating and cooling system for further heating to an optimal temperature. This preheating of the air source is not very energy efficient and is a more expensive process. Due to this, HVAC systems usually do not utilize 100% outside air and instead recirculate air. But with the increasing need for a 100% outside air source, Daikin designed SmartSource.
SmartSource DOAS does not utilize this preheating coil step and instead, the air gets heated with a water source heat pump’s hot gas in addition to the unit’s primary DX coil. The hot gas reheat coil is usually not used in HVAC systems during the winter because the outside winter air does not need a dehumidification step. The SmartSource uses the hot gas reheat coil not to dehumidify the air but instead acts as another heating agent to allow an efficient heating cycle with a 100% outside air source in the winter. Instead of a DOAS system that utilizes a preheating coil, DX coil, and hot gas reheat coil, the SmartSource takes away the need for the preheating coil and increases the use of the hot gas reheat coil. By taking away just one coil, it is significantly more energy efficient and cost effective.
3D Printing and Daikin
Daikin has recently joined the trend of additive manufacturing, but its use is still under development. Additive manufacturing enables the production of objects without custom molds or tooling and allows the production of complex shapes and intricate designs that cannot be handmade.
Daikin has started utilizing fluoropolymers in their prototyping process when designing HVAC systems. Some examples of this are 3D printed fans, ducts, valves, etc. Daikin wants to further take that step with their chemicals department by developing a polymer suitable for powder bed fusion technology to create the best in class heat and chemical resistant 3D printed parts. This type of 3D printing process would not only be suitable for HVAC part utilization but also see use beyond, as the company explains:
“Daikin has developed a world-first fluoropolymer resin suitable for ‘Powder bed fusion’ technology. NEOFLON PFA’s as best-in-class heat and chemical resistance enable 3D printed parts suitable for semiconductor manufacturing, aerospace, oil and gas, and jigs and fixtures in chemical plant.”
The Research & Development Tax Credit
Whether it’s used for creating and testing prototypes or for final production, 3D printing is a great indicator that R&D Credit eligible activities are taking place. Companies implementing this technology at any point should consider taking advantage of R&D Tax Credits.
Enacted in 1981, the now permanent Federal Research and Development (R&D) Tax Credit allows a credit that typically ranges from 4%-7% of eligible spending for new and improved products and processes. Qualified research must meet the following four criteria:
- Must be technological in nature
- Must be a component of the taxpayer’s business
- Must represent R&D in the experimental sense and generally includes all such costs related to the development or improvement of a product or process
- Must eliminate uncertainty through a process of experimentation that considers one or more alternatives
Eligible costs include US employee wages, cost of supplies consumed in the R&D process, cost of pre-production testing, US contract research expenses, and certain costs associated with developing a patent.
On December 18, 2015, President Obama signed the PATH Act, making the R&D Tax Credit permanent. Beginning in 2016, the R&D credit can be used to offset Alternative Minimum tax for companies with revenue below $50MM and, startup businesses can obtain up to $250,000 per year in payroll tax cash rebates.
The Future of Daikin
As many in the HVAC industry struggle to meet the demanding 100% outdoor air source technology, Daikin continues to move forward with innovation, not only improving the energy efficiency of their technology but also making it cost-effective and finding new ways to constantly improve. Their innovation in the HVAC is profound and continuous, even with their chemistry department finding new ways to incorporate 3D printing to their technologies. Daikin is a force that will stay and continue to amaze the world with new HVAC advances.