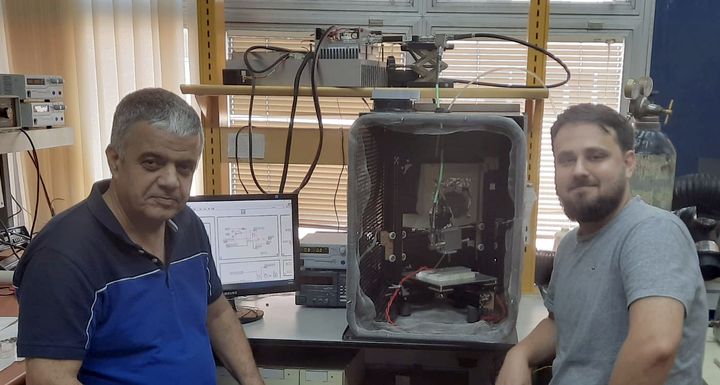
When I saw 3DSLA.RU’s unusual microwave-based 3D printer last November at Formnext, I thought it was the only one.
I was wrong.
It turns out there has been much research devoted to this form of 3D printing at Tel Aviv University by Prof. Eli Jerby. They’ve been working on this process for at least ten years.
Microwave 3D Printing
What’s so interesting about microwave 3D printing? It is an approach for producing metal objects, which is done by laser or electron beams in most current metal 3D printers. However, the powerful lasers required to swiftly melt the metal powder are quite expensive, leading to large machine costs. On the other hand, a microwave approach could be significantly less expensive, as microwave generators are commonly available.
I spoke with Prof. Jerby to find out more about this work, the process and where it’s all headed.
Fabbaloo: Who’s involved and when did you begin?
Prof. Eli Jerby: “The idea of using localized microwaves for additive manufacturing (AM) of metal parts was invented a decade ago by myself from Tel Aviv University (TAU), Israel, together with colleagues from ASCAMM (now EureCat) Catalonia, Spain.
The original patent (granted in 2017) is available here (PDF).
I have led since then the R&D project in our laboratory at TAU with my research students. Currently, the leading PhD student in this project is Mr. Amir Shelef. The project is supported by the Israeli Ministry of Science and Technology (MOST) and by the Israel Science Foundation (ISF).”
Fabbaloo: How did the project start? What was the inspiration?
Prof. Eli Jerby: “The project started in a visit by Mr. Rafael Rubio and Mr. Xavier Planta from ASCAMM (Spain) at Scilense Microwave Ltd. (Israel), a start-up company which developed in 2008-2012 a previous invention, the microwave drill, published in Science Magazine in 2002.
The microwave drill utilizes the localized microwave-heating (LMH) effect, which resembles to some extent laser heating, and hence inspired the usage of LMH also for AM of metal parts (as a substitute for lasers).”
Fabbaloo: Without giving away secrets, how does the process work in a few sentences?
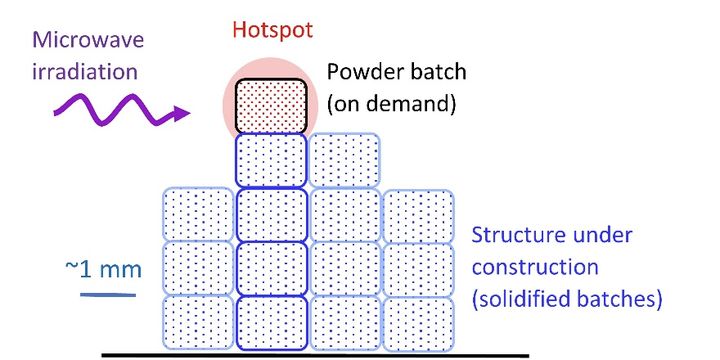
Prof. Eli Jerby: “Basically, the LMH effect leads to a local thermal-runaway instability, due to the temperature-dependence material properties, which rapidly increases the temperature in a small hotspot. Dealing with metal powders, a localized microwave power in the order of 200W may increase the local temperature at a ~1-mm3 region by ~1,000°C in ~1 second. This capability enables us to melt small batches of metal powders in order to solidify and join them in an incremental manner. In this LMH-AM process, there is no need for a powder bed. The powder is supplied by small batches of powder on demand (PoD).”
Fabbaloo: What types of materials are applicable?
Prof. Eli Jerby: “While our recent work focuses on metal powders in a PoD scheme, the patent mentioned above also covers the supply of the raw material in a form of a wire, and it is also referring to other raw materials such as ceramics. The metal powders that we use could be the same as used in laser-based AM systems (which are typically fine and quite expensive powders) or powders of much inferior quality (rough, large grain sizes, low-cost metal powders).”
Fabbaloo: Why is the process important? What advantages does it have over other processes?
Prof. Eli Jerby: “The main advantage of our concept, and hence its importance, is its low cost (in both the installation and operational levels). The LMH-AM equipment is based on commercially available RF/microwave devices, imported from widely spread microwave-heating or cellular communication applications. These are much cheaper than laser components. Furthermore, the operation of the LMH-AM process is cheaper due to the high efficiency of the microwave process (possibly up to ~70%) and due to PoD approach, which saves in the powder handling, logistic and safety issues.”
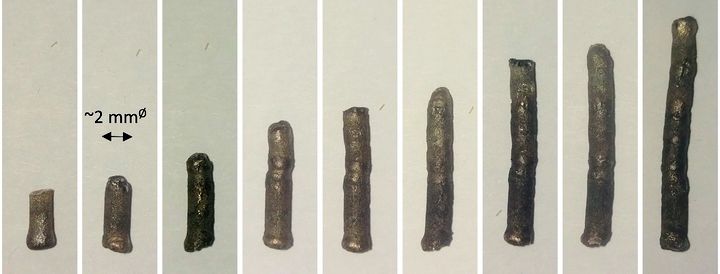
Fabbaloo: What are the limitations of the process?
Prof. Eli Jerby: “The main limitation of the LMH-AM process is the inferior resolution, as compared to laser-based technique. The voxel size is dictated by the powder-batch size and the LMH parameters, and is typically in the order of ~1-mm3 or larger. This scale resolution requires some post processing in many applications, or a hybrid operation (e.g. using LMH for the rough structure and a laser for the final details).”
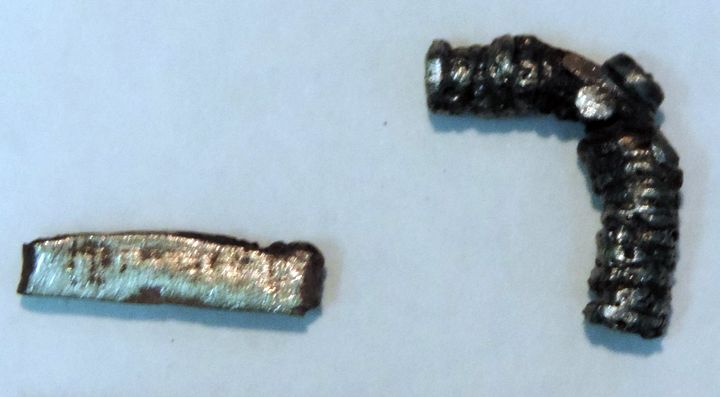
Fabbaloo: What could be future commercial applications of the process?
Prof. Eli Jerby: “The LMH-AM process may provide economical answers in two ways:
As a stand-alone LMH-AM system, it may supply needs for 3DP of relatively large and rough metallic objects.
In a hybrid approach, LMH-AM could be incorporated with laser-based 3DP’s or even with CNC machines, in a way that the LMH-AM performs the main structural construction and the laser or CNC completes the fine details. This hybridization may significantly reduce the production costs.”
Fabbaloo: What will your next steps be?
Prof. Eli Jerby: “We wish to transfer our LMH-AM to the industry, and hope to see it implemented in reality. We are now looking for an industrial/business partner who will lead the next stage of the LMH-AM technology transfer to the market, and we are willing of course to proceed in our R&D efforts on this line.”
Fabbaloo: Do you intend on commercializing the process at some point in the future?
Prof. Eli Jerby: “Certainly yes. Though most of our work is still done at an academic environment, we (personally and institutionally) certainly desire to commercialize it. We believe that it has a great practical potential, note e.g. our recent publication on the transistor-based LMH-AM system (links below) which demonstrate the LMH-AM potential as a compact, low-cost solution for rough 3DP of metal parts.”
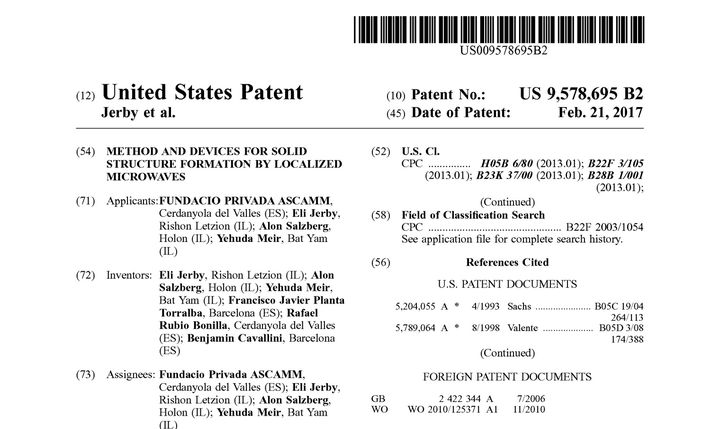
The team has indeed patented this process via US Patent 9,578,695, “Method And Devices For Solid Structure Formation By Localized Microwaves,” by E. Jerby, A. Salzberg, Y. Meir, F. J. Planta, R. Rubio, B. Cavallini, filed Sept. 24, 2013 and Granted Feb. 21, 2017.
If any readers are interested in beginning a commercialization of this work, you had best contact Prof. Jerby as soon as possible.
For further details, Prof. Jerby suggests looking at their published papers on the topic:
On The Microwave Drill
- E. Jerby, V. Dikhtyar, O. Actushev, U. Grosglick, “The microwave drill,” Science, Vol. 298, pp. 587-589, Oct. 18, 2002.
On Microwave-Based Additive Manufacturing
- E. Jerby, Y. Meir, A. Salzberg, E. Aharoni, A. Levy, J. Planta Torralba, B. Cavallini, “Incremental metal-powder solidification by localized microwave-heating and its potential for additive manufacturing,” (PDF) Additive Manufacturing, Vol. 6, pp. 53-66, 2015.
- M. Fugenfirov, Y. Meir, A. Shelef, Y. Nerovny, E. Aharoni, E. Jerby, (2018) “Incremental solidification (toward 3D-printing) of magnetically-confined metal-powder by localized microwave heating” (PDF), COMPEL – Int’l Jour. Comp. Math. Elect. Eng., Vol. 37, pp. 1918-1932, 2018.
- A. Shelef, E. Jerby, “Incremental solidification (toward 3D-printing) of metal powders by transistor-based microwave applicator,” Materials and Design, Vol. 185, Art. No. 108234, Jan. 5, 2020.