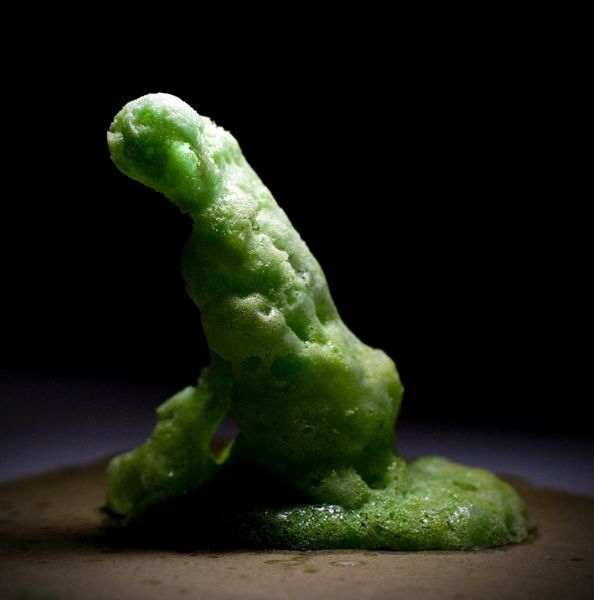
I’ve recently been corresponding with reader Michał Baran, who has been working on one of the most unusual 3D printing processes yet seen.
Baran, a jeweler by trade, is located in Poland, where he postulates different methods of making objects. I should point out he not only postulates them, but in several cases has performed experiments necessary to prove they are feasible, including this highly unusual and as-yet-to-be-named foam-based 3D printing process.
One of his projects involves a radically new way to 3D print using foam, a method that in retrospect is so obvious it is surprising it has not been attempted previously.
Using Foam For 3D Printing?
I asked Baran to explain how this concept came to be, and he replied with the most unusual story:
“Because I didn’t know anything, I started looking for experts in this topic.
Once upon a time I met a bumblebee and asked him what do we have to do? He replied:
‘Bro, finally someone sincerely asks us about it! The answer is very simple – start comparing how we, birds, trees and intoxicatingly beautiful dolphins are different from the things you humans make… Note that we are mostly made of nothing, the main ingredients are air and water… Dude! Your body also built that way! Never forget that you yourself are the best model for what you’re doing. Additionally, notice our topology! This is crucial! Proper topology is key to everything. You won’t find a single point, straight line or right angle anywhere in nature. So why you even draw these wickedness?! The effects of human activities are like a cancer against the reality that surrounds you. Change it!’
He told me this and flew away, I have an old pear tree as a witness. I was shocked. For the first time I realized where the causes of the problems were and how much we have gone astray. We are doing everything upside down. Seriously! If aliens came to Earth, they would be non-stop surprised.
‘Guys! Why are these skyscrapers are so silly shapes? Why don’t they look like redwoods or termite mounds? Look! Their females are so beautiful, rounded – why do they force them to live in hideous, angular houses?! What is going on here on this Earth?!’
I started to analyze everything in terms of what Mr. Bumblebee told me. I changed my mind about many things. This process is so painful but salutary.”
It was this revelation that put Baran on track towards developing a foam-based solution. But how to make a structure that stands up on its own? After some contemplation, Baran realized he could use a photopolymer approach:
“This ingredient must be in liquid form for the foaming process to take place. Ok, can we use any kind of water-soluble resin? Yes, but no…
It should be noted what happens to the ‘pure’ foam itself. When it only consists of water and air and… something else. It’s about surfactants. This is a very complex process, but they are what you need. Even good quality foam has a very limited lifespan. So we have really little time for our actions. Therefore, not all resins are suitable for this task. Those that are water-soluable/dilutable, need a lot of time to work, the water must evaporate… But water is also somehow the first builder of our foam, so the foam will disappear before the resin starts to take on stiffness. I decided that it is necessary to use resins that have a very fast transition from liquid to solid. Possibly immediate.Okay, maybe polyurethanes can be a good candidate? Yes, you can adjust the mixture of two-component polyurethane foam that works fast. But there is also a problem – if you start a reaction, you can’t stop it anymore… Its out of control. The same problem is with cyanoacrylates – please, be careful with them!
Therefore, photopolymers seem to be the natural choice. You do what you want and when you want to accept it, you constitute this change. And you immediately have a rigid effect.”
Photopolymer Foam
Then came the stunning revelation about how this could work:
“Finally I had a solution! And I put it aside for a long time… Because UV resins are still too expensive. I started working on other methods (more non-woven like structures).
One day, I went to the kitchen, got some dish soap. Then I mixed it with UV resin. I made a minifoamer, a foaming attachment for an airbrush… I cured formed foam by UV flashlight. Yes – this is a rude, primitive method but it works! There is an even simpler solution (my second choice) – you can use foam soap dispenser, from bathroom this time… 🙂 So all this machinery you can fit in your pocket, and it will cost you only a few bucks…
Apart from the appropriate recipe, the mixing mechanism and the formation of the foam structure are also important. It is different in both cases. It is a big challenge to research it. Foamer or foam cannon gives more possibilities, such a process is easier to be parameterized.”
Let’s recap this if you’re not following the process he’s developed:
- Mix a photopolymer with a dish soap
- Emit foam from the mix with a foaming device
- Solidify the photopolymer in the foam using widely broadcast UV light
Baran explains how the UV radiation is applied:
“Irradiation is equally important – not only the power and wavelength, but also the direction. Since each time we create a fragment of a spatial object, the lighting should be around this place.
Notice how lucky we are – in a normal situation, photopolymers polymerize in a very thin layer. That is why we are always doomed to layering… Larger volumes cannot be polymerized. The foam is very voluminous but consists of extremely thin material walls. Therefore, for our resin, a foam works like a spatial optical fiber! This is a wonderful circumstance.”
This is notable: the foam itself carries the UV radiation through to internal portions of the foam to allow full curing.
How To 3D Print With Foam
Since the initial experiments, Baran has moved on from “dish soap” and now experiments with more sophisticated materials, but the concept is the same: extrude photopolymer foam and quickly solidify it.
There’s a question about how this could be used to form useful shapes, and that depends on the method of delivery. I can see several approaches:
- A manually operated foam extruder that would work somewhat like a 3D pen
- A robotic arm to do the same motions
- A gantry-based motion system to move the foam extruder to appropriate locations
Or, this:
When I watched that video, the future of this process became clear to me. It should be possible to very quickly produce structures of at least simple geometry by combining that approach with that of Baran’s foam solidification method. However, there would be a great deal more work to do to fully develop the approach.
I got the impression from Baran that his goal is simply to change the way people make things; to make things in a more simple manner. It’s not clear whether he wishes to commercialize the project, but I suspect some Fabbaloo readers may be interested in doing so.
Regardless of the commercialization potential, this is surely one of the most interesting 3D print processes I’ve seen in a while.
Via ArtStation