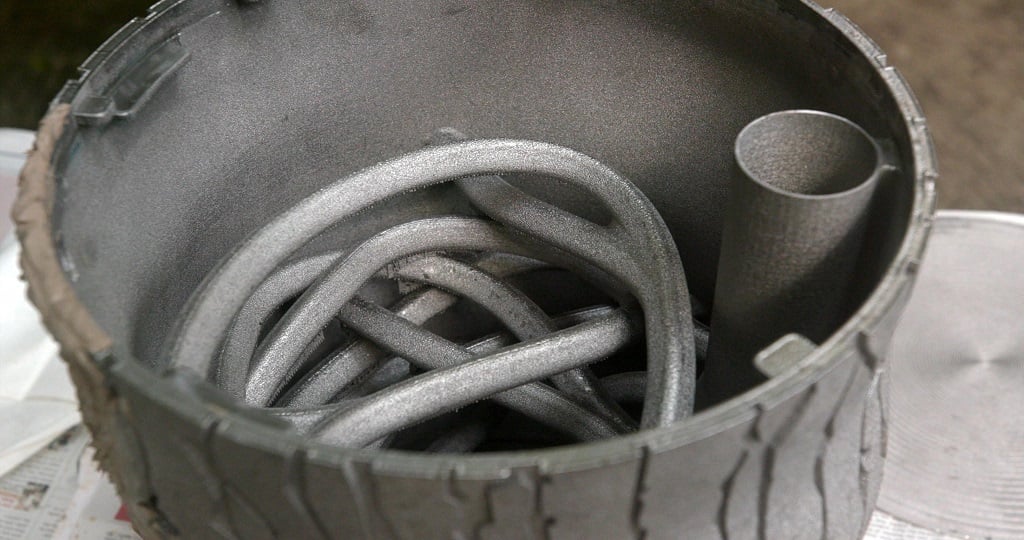
3D printing is well known for creating complex designs with intricate internal structures; sometimes those structures serve as tubes for crickets.
Earlier this year, GE Additive worked with a local zoo to help out with a rather different sort of problem than their advanced metal additive manufacturing experts usually face. This time, rather than a demanding aerospace client, they worked toward a new clientele: the meerkat. (And the fennec fox, other small mammals, some birds…)
The Cincinnati Zoo was in a bit of a quandary, one familiar to zookeepers worldwide: how could they both feed and keep animals engaged in their surroundings? Zoo animals obviously live in an environment rather different from the wild. Food is freely available, there’s less roaming to do, and people are everywhere.
How could the animals regain some sense of autonomy in their dinnertime?
Enter additive manufacturing.
GE Additive x Cincinnati Zoo
David Orban, Cincinnati Zoo’s animal excellence manager, laid out the basic premise of the project:
“Something that we often think about is how to mimic natural feeding behaviors in the animals that we care for. In the wild, animals are adapted to find, acquire, and process food – and it’s not always easy! In human care though, food is always available and of good quality and balance, and in many cases, it’s consumed quite quickly.
“For example, one challenge that we often see when we offer live insects to some of our birds or small mammals is that they are captured and consumed in a matter of five to ten minutes. We’ve had the idea to create a more complex feeder that will extend foraging duration, in turn, extending animals’ physical activity and mental stimulation, leading to more naturally behaving wildlife.”
This may not sound like a no-brainer for additive manufacturing — until the project is broken down a bit into its component needs:
- A unique geometry with complex internal structures
- A custom, low-volume part to meet a specific need
- A design that could be tweaked as needed
GE Additive’s AddWorks consulting team worked closely with the zoo to sort exactly what was needed for the pro bono work, as lead engineer Shannon Jagodinski noted. First among these is of course safety — and close behind is the need for “the animal enrichment device [to] look natural within the environment,” she said.
Two ideas emerged among the engineers, and the zoo team selected the one they thought would better offer benefits to more of the animals in their care. In February, the GE Additive team 3D printed a tree trunk-like structure using recycled titanium powder, creating a nature-inspired device that will fit in to the environment. They delivered the piece before the pandemic shut zoos down for some time, which also allowed the zoo team some quiet time to test it out with the animals.
Cricket Tubes
The 3D printed metal trunk looks nice and barky outside; inside is a complex mess of tubes of various sizes that lead to different exit points around the exterior.
Into the top of the opened device, zookeepers can position their cricket funnel and pour a multitude of the bugs in to fulfill their destiny as meerkat food. The crickets, once inside, have their choice of tubes to wander out for their final foray into the outside world.
Upon emerging, the crickets then become prey — just as they would in the wild, where the bugs appear at random in the animals’ environment.
And, just as in the wild, the animals are kept busy hunting the wee beasties for hours at a time. This is a far cry from the 5-10 minutes Orban and his team had observed prior to the new design.
The first test, successful as it was, is leading to more installations, as GE Additive explains:
“GE Additive will be delivering several more of the feeding devices to the Cincinnati Zoo, including one for education around animal enrichment and 3D printing capability. This demo piece will remove a portion of the bark textured exterior to expose the complex and intricate internal passageways made possible with metal 3D printing to teach school groups and other visitors.”
Via GE Additive