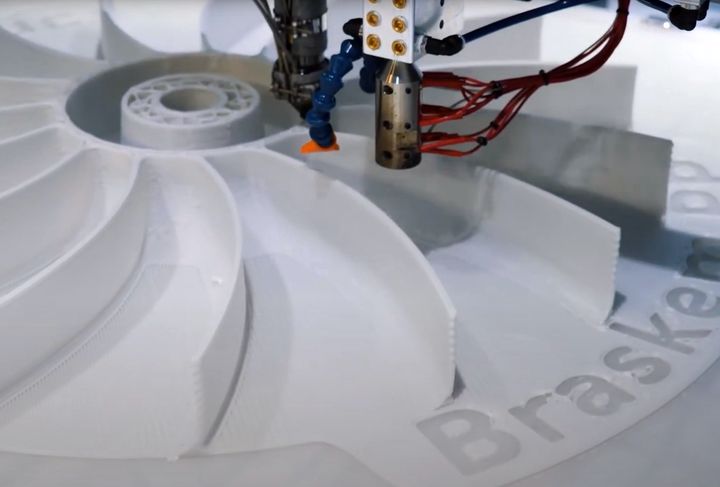
Titan Robotics announced a new partnership to produce highly effective polypropylene pellets for 3D printing.
The Colorado-based company has focused on producing very large-scale 3D printers for several years. From their first machine we saw in 2016, they have gradually evolved their 3D printer product into a rather sophisticated design.
Titan Robotics was one of the first 3D printer manufacturers to realize that pellets were the way of the future for large-scale 3D printers. The problem with large-format 3D printing is that by definition you’re using a lot of material.
Normally that material is filament, which is actually polymer pellets extruded into filament form. There’s a cost to do so, and that cost is carried through in the price of the filament. Meanwhile, the same amount of material in pellet form is vastly less expensive. Thus, more advanced large-format 3D printer systems now tend to use pellets instead of filament simply to lower operational costs by cutting out the filament step entirely.
There are plenty of materials available in pellet form, as these were used to produce filaments; the set of filaments is actually a subset of the available pellets. However, some of those source resins have been custom-designed by chemical companies specifically for 3D printing. And these are often tied directly to a 3D printer manufacturer.
Thus the breadth of generally available pellet materials is not as wide as one might think, if you’re looking to do 3D printing with them.
While there are pellet materials generally available, they are almost inevitably not optimized for 3D printing. Thus although you might use a specific material, the 3D print results might not be outstanding. Layer adhesion is usually the culprit, where prints can delaminate.
That should not be the case with Titan Robotics’ new material. They’ve partnered with Braskem, a huge Brazilian chemical company (2017 revenue of US$14.7B) to develop a polypropylene mix that’s designed for optimized 3D printing.
Apparently the two companies worked on this project for over a year, and now are ready to release the results. And it’s not just a single formulation of polypropylene. They explain:
“Utilizing Titan’s innovative pellet extrusion system on its Atlas 3D printers, Titan and Braskem worked together for more than a year on the research and development of this new polypropylene grade for additive manufacturing. Through a strategic partnership Titan and Braskem plan to continue to offer innovative new grades and custom compounds of Braskem’s polypropylene resin to meet the needs of Titan’s industrial customers.”
The new material is optimized in that its crystallization has been tuned to allow for better inter-layer adhesion, which should make for very strong parts. This is more important for large prints that must support their own weight.
Additionally, the new polypropylene mix offers “little to no warpage”, which is excellent news for anyone using Titan Robotics’ 3D printers. Large 3D prints suffer from warping because the shrinkage is amplified along the longer axes of a print. Larger prints means more warping, and that’s plagued large-format 3D printer manufacturers for years, severely restricting the usable material types.
However, Titan Robotics has seemingly overcome this barrier and now their clients can produce very large polypropylene objects with almost any geometry.
I’m impressed with this development, as it further recognizes the need for specifically-designed materials usable for 3D printing. It’s been far too long that our industry has been dependent on “leftover” materials designed for other purposes years ago.
Via Titan Robotics