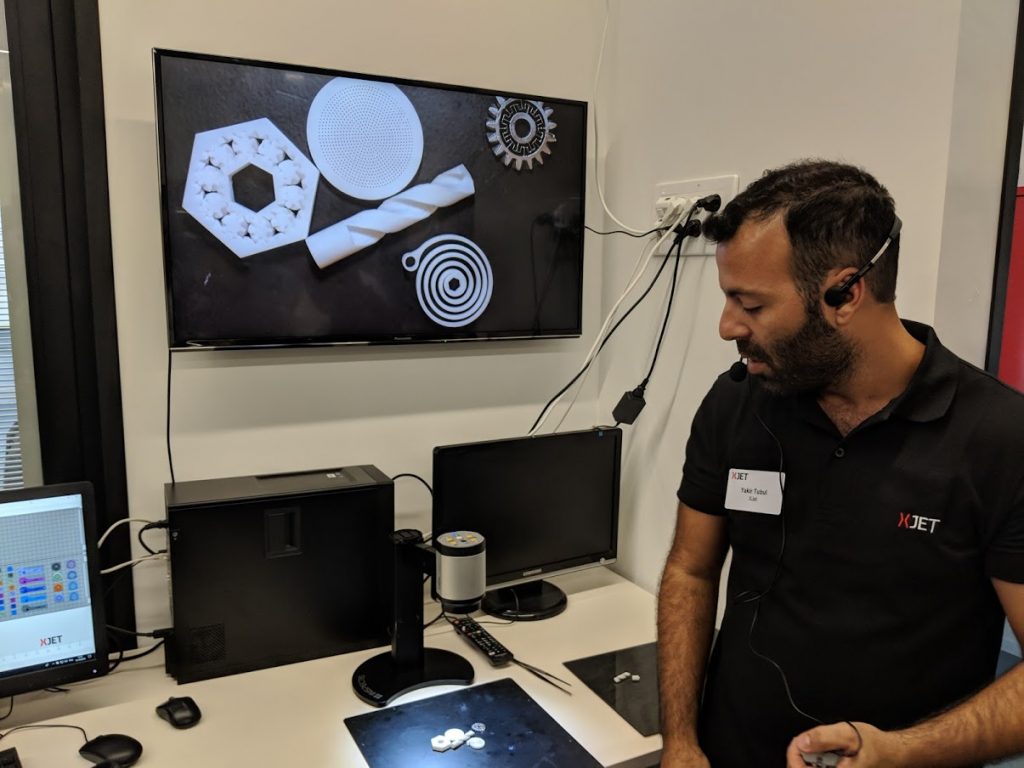
The dental industry is a major user of ceramic 3D printing, and a new global partnership is set to see applications move from concept through to production.
Israel-based XJet has been making quite a name for itself these last few years with its leading work in metal and ceramic (and even metal-and-ceramic) 3D printing. Their Carmel 1400 AM System is a thing of beauty, really, inasmuch as a piece of industrial equipment can be. The system offers NanoParticle Jetting (NPJ) technology with powderless materials contained in easy-to-handle cartridges, including the support material. The efficiency of the system and impressive results possible with NPJ have established XJet as a company with a solid niche in ceramic 3D printing across a variety of applications.
Among the top applications for ceramic 3D printing is dentistry. And it is here that a recent announcement comes into play.
XJet x Straumann
Switzerland-based Straumann Group is partnering with XJet to scale up its use of NPJ ceramic 3D printing.
Straumann, an early NPJ adopter, turned to ceramic 3D printing to enhance its dental work, including the development, manufacturing, and supply of dental implants, instruments, and more for replacement, restorative, orthodontic, and preventive dentistry.
Straumann VP Stephan Oehler explains of the company’s history with the technology and reasoning for expanding on this usage:
“We’ve been working with XJet NanoParticle Jetting technology for some time, up to now it has been used for developing product iterations and providing proof of concept. Now we’re scoring the first product development project to reach the next level of bringing this technology to production of ceramic end-use parts. We believe this technology can scale-up for production effectively, there’s a large print bed and with the soluble support material we find post-processing simple and efficient.”
The company’s primary reasons for adopting the Carmel system into use include:
- Part accuracy
- Part density
- Shorter overall production cycles
- Soluble support material
We’ve had the opportunity to get hands-on with many ceramic parts from XJet; I’ve travelled to Israel to see their $10M Additive Manufacturing Center, checking out machines running and the NPJ process, from loading cartridges to submerging parts to remove the soluble supports. Basically, Straumann’s reasonings resound with the results I’ve seen first-hand.
Straumann 3D Printing Strategy
It’s important to note the differentiating characteristics for XJet, as the company continues to set itself apart. Dental leaders like Straumann are themselves by now often familiar with how 3D printing can help their business — so it’s interesting to see their perspective of why to select NPJ and deepen that commitment.
“We’re well-versed with the benefits of AM, so we knew that the freedom of design and complex geometries delivered by the technology, now for ceramic materials, could open up new product and application possibilities for the business,” Philippe Chavanne, Head New Technology Competence Center, said.
Indeed, so familiar is the Straumann team with 3D printing that they offer their own CARES P-Series line of 3D printers for dental labs. These seem to use resin materials — but that’s not all that Straumann needs for its work. The company’s PURE implant, for example, is made of ceramic/zirconia material; they’ve shared an in-depth look at the science behind using zirconia rather than the more common titanium in this application here. Zirconia, as it happens, is a perfect fit for 3D printing with XJet’s technology.
“We work with ceramic in a lot of our products, so when we learned there was a new technology in the field, we looked into it. XJet convinced us with the quality of parts, the fine details and accuracy. In addition to that, the density of the material is extremely high, close to 100%, so it’s not like working with an ‘AM material’,” said Chavanne.
Fitting NPJ into the Straumann workflow fits neatly as well with XJet’s history of letting the customer drive the way ahead. NPJ usage, as XJet CEO Hanan Gothait has told me, “is all coming from our customers.” XJet is highly invested in seeing its additive manufacturing process and applications evolve, as CBO Dror Danai has underscored in other conversations.
Uninterrupted Dental 3D Printing
Another important point in Straumann’s NPJ adoption: timing.
Obviously 2020 has been a difficult operating environment for many businesses around the world due to the global novel coronavirus pandemic. But, as it turns out, COVID-19 hasn’t slowed Straumann’s use of its Carmel system down at all.
“There’s already a demand for the ceramic parts produced on the Carmel 1400, and social distancing is viable because operation of the system is very simple, so we’ve been able to keep the system running even through the global pandemic,” said Oehler.
Via XJet