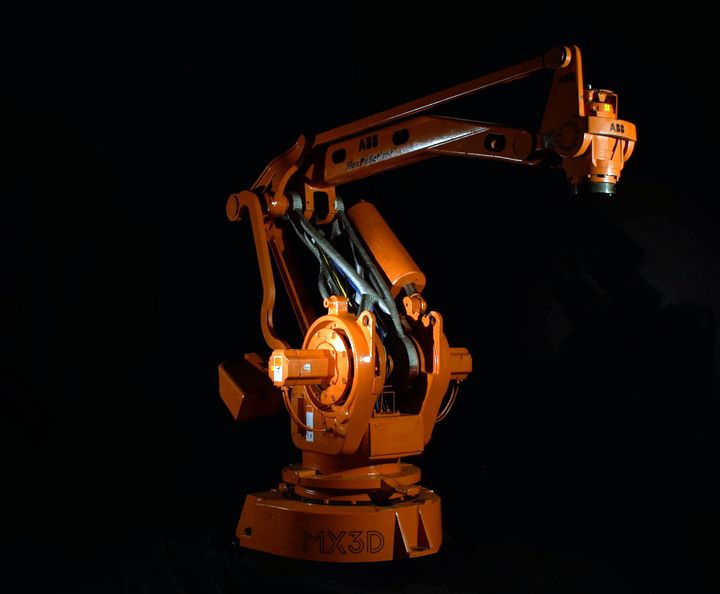
When we last saw MX3D at Formnext 2019, they were showing off a 3D printed robot arm. Now, they’ve tested it in a working robotic system.
The Amsterdam-based company has been developing a method of metal 3D printing they call “WAAM” — Wire Arc Additive Manufacturing. It’s a type of deposition 3D printing in which they have a wire arc welding head mounted on the end of a robot arm. The arm moves to effect deposition of metal layers to build up an object.
WAAM Manufacturing
Using WAAM, the firm has successfully demonstrated several large projects, including a bike frame and even an entire bridge.
One of their most recent projects was to develop a replacement part for a robot arm, which we saw last November. This is a rather large piece that weighs 73kg. While that’s pretty weighty, it’s far less than the original part’s 150kg.
It seems that MX3D worked with engineers at Altair to design a replacement robot arm part that weighed much less due to the removal of unnecessary material. By performing advanced structural analysis they were able to generate the unusual geometry of the replacement part, and then print it in real life.
The 3D printed part is not finished once it emerges from the WAAM 3D printer. In fact it has to be finished with a CNC machine, or in the case of the robot arm part, the portions that connect to the remainder of the robot. This required a couple of smooth surfaces and a precision hole for attachment. Otherwise, the entire part was usable directly from printing.
Using Metal 3D Printed Parts
The news today is that MX3D have resumed operations after a delay due to the pandemic, but were then able to install this unusual part in an ABB robotic system, as seen above.
While there’s plenty of buzz about lightweight aerospace parts, for obvious reasons, there are also reasons for lightweight parts in other industries. This robotic system, for example, would have less mass to move as the ABB robot engages. Less mass means less stress on the motors, which could lead to a longer operational life.
It could also mean, if sufficient additional parts were similarly treated, the motors could be downgraded as there is less mass to move in total. This could create a reduction in price for the robotic system, or more profit for the robotic system makers. Or perhaps a little of both.
What’s important to me here is that MX3D were not only able to design and produce this unusual part, but also prove that it worked by actually installing it in a working system. In the video you’ll see the ABB robot moving successfully.
There are plenty of times where prototype parts are made by 3D printer manufacturers as demonstrations, but in many cases the parts are merely for show and aren’t “real” parts that could be actually used. MX3D has taken things a bit farther here and shown the feasibility of their process.
As should everyone.
Via MX3D