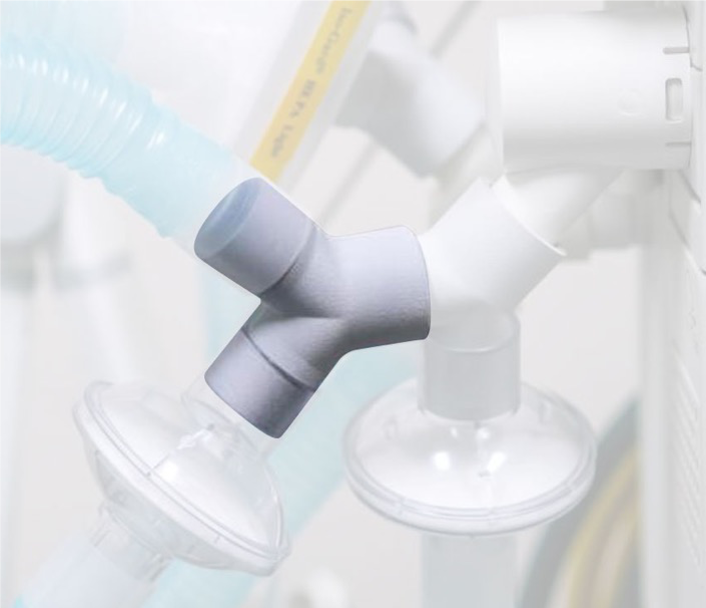
Jabil is uniquely situated to address both stop-gap and long-term supply chain needs relating to pandemic response, as a recent conversation highlights.
The digital manufacturing solutions provider has become ever more deeply entrenched in the 3D printing industry over the years, and it’s always interesting to see where they are stretching to fit this technology into their broad global operations. While speaking with John Dulchinos, Vice President of Digital Manufacturing, to catch up on Jabil’s recently announced collaboration with Fictiv and other operations updates, one portion of our conversation stuck out as having broad-reaching and long-lasting implications springing from the unusual market conditions of 2020.
Jabil COVID-19 Response
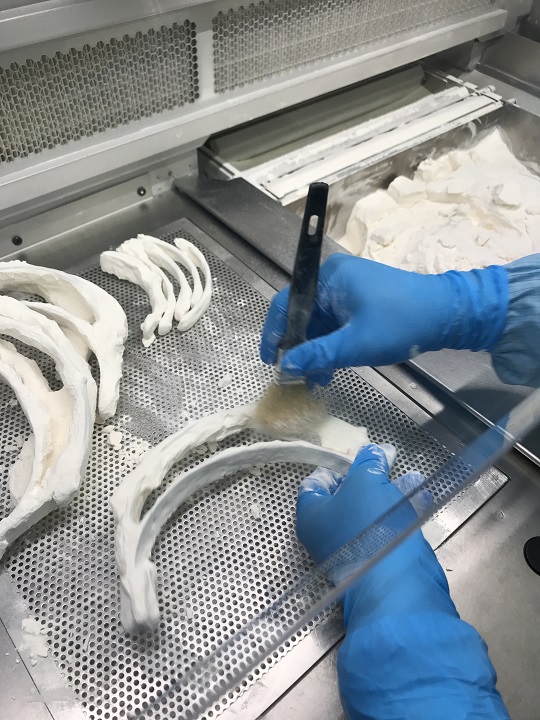
As with many companies working with 3D printing, Jabil was quick to deploy its capabilities to serve pandemic response starting earlier this year.
“In addition to all those sites [we operate in production and research applications around the world], we have hundreds of 3D printers deployed across the company of varying degrees, from desktop to more sophisticated industrial systems. These are not focused on our external network, they’re more supporting our operations,” Dulchinos explained to set the scene. “In mid-March when we saw the pending impact of the virus on the economy and the healthcare system, and the need for a whole set of devices there were shortages around, whether that be PPE devices and masks and face shields, or whether it was test strips or components that were in short supply for ventilators, we could see there was an immediate need to fill that void.
We turned to our additive manufacturing network and started tapping into our excess capacity of 3D printing across the company, from Blue Sky and even labs in St. Petersburg, Florida — we even had some guys who had printers in their garage. We were filling the void like so many other 3D printing companies were.”
The company shared a quick snapshot of just a few of their pandemic-response efforts, including:
- Helped a healthcare customer produce a 3D printed prototype of a reusable N95 mask in 24 hours—Prototypes were well received by health professionals, putting Jabil on course to produce 30K to 50K reusable masks per day using volume manufacturing
- Worked with a customer to develop “Wye splitters” to allow one ventilator to provide air for two or more patients at a time
- Produced 3D printed prototypes and parts for test products (virus/antibody); connected a customer to a member of the Jabil Additive Manufacturing Network to accelerate the production of NP swabs needed in COVID-19 testing
- Developed a prototype for a plastic battery case to expedite the redesign of an EOL battery and case need for older Powered Air Purifying Respirators (PAPR) that had been in storage.
3D Printing In Supply Chain
What, for Jabil, has proven especially illuminating in dedicating resources to these efforts goes beyond immediate response.
Certainly that response was necessary, and it’s been remarkable to see this industry banding together to provide massively-needed medical equipment during a pandemic — but there’s more to the story that will see impact beyond this terrible virus.
“For Jabil, what’s really noteworthy is — the reality is, as much as we talk about how great 3D printing is, it’s still a really insignificant part of the overall manufacturing economy. Even looking at capacity, we’re still nowhere near the capacity of traditional manufacturing,” Dulchinos acknowledged. “One great thing we could do, starting in mid-March to make face shields, components for ventilators, and so forth, but really take a step further in doing that really heavily in March, into April. By the first half of April we had a number of areas using 3D printing to fulfill supply chain and get to mass producible robust designs — then turn our rapid tooling operations on in Asia. In a matter of weeks, certainly by the middle of May, we started to tool up these operations and produce then at a very high scale. In the next phase of the pandemic, we are still filling voids in masks and components, and seeing ramped up high-volume production lines.”
That’s exactly where 3D printing has been seen to fit here, filling immediate supply chain needs as traditional manufacturing ramps up to full capability to produce the medical equipment and devices in such short supply.
With countries like the US still deeply in the grip of the virus, the need for personal protective equipment (PPE), testing equipment, ventilator parts, and other such products is ongoing. And Jabil is in a unique position to address both immediate and longer-term supply chain needs.
“That’s the Jabil story: yeah, we can immediately jump in with solutions in 3D printing, but we’re using that to validate designs and really ramp up production. We have to get to an economic model that makes sense, and manufacture to hit that scale,” Dulchinos told me. “The value proposition we brought to the marketplace is to fill that gap, refine the designs, then move those items to volume production and get the cost and the volumes to a point where we could make an impact on those gaps in the marketplace.”
That’s exactly what we’ve been seeing for long-term implications, where the low-volume production of 3D printing can be brought online nearly immediately and used until high-volume production capabilities are ready. Jabil is unique in offering this entire workflow within a single entity.
The company is up to much more, as Dulchinos shares in the second part of our conversation focusing more on Jabil’s operations, from facilities and collaborations to materials advances.
Via Jabil