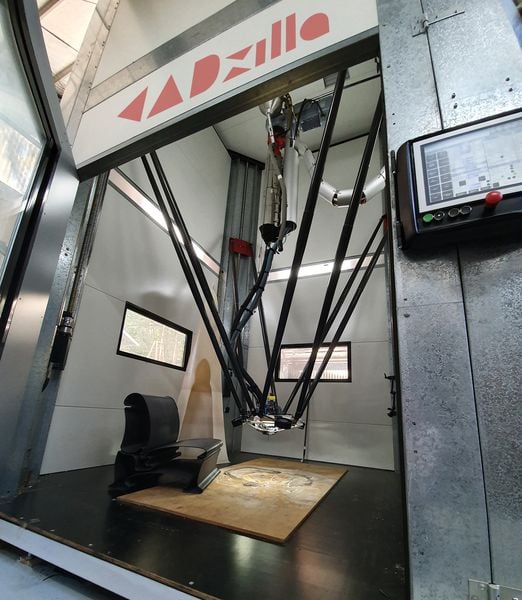
There are large 3D printers, and there are larger 3D printers. And then there is CADzilla.
Australian company Studio Kite operates a truly massive 3D printer they call “CADzilla”. It lives up to its name as it sports an unbelievable 2400 x 2400 x 3000 mm build volume, which, honestly, is best specified in meters, not millimeters.
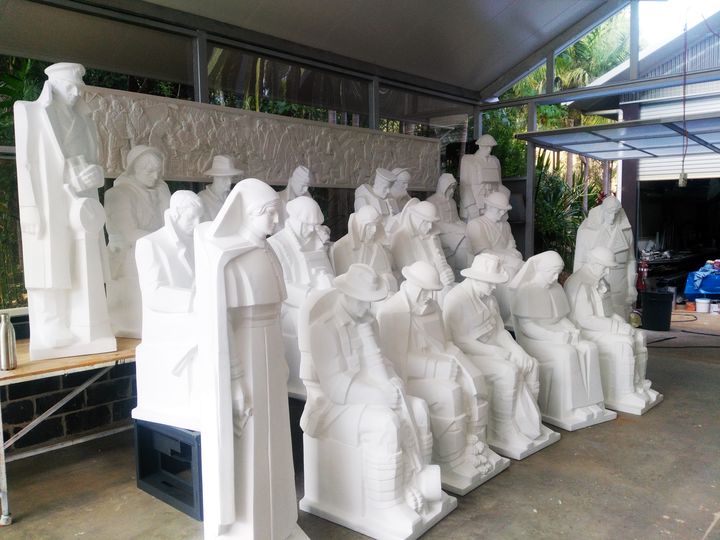
They use this enormous device to provide service to the art services industry, where public sculptures and motion picture props of large size are frequently required. In many cases these are temporary requirements, as film productions need props only for the duration their project.
Studio Kite 3D Printer
Studio Kite’s director, Steve Rosewell, realized there was an issue in this industry as years ago the standard approach was to tediously sculpt foam and then apply a rigid coating to produce large props. This was an expensive method, and resulted in huge non-recyclable objects after the conclusion of use.
Studio Kite then embarked on a long journey to develop a scaled-up thermoplastic 3D printer that could produce these huge prints, but at the same time do so at a lower cost and offer the added benefit of recyclability.
CADzilla Size
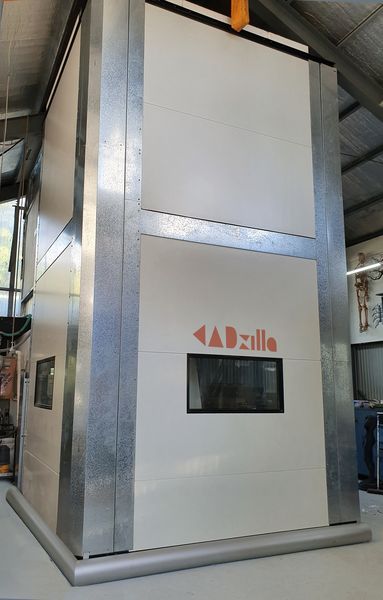
While many Fabbaloo readers are familiar with desktop thermoplastic 3D printers and the challenges of operating them, there are many additional challenges that emerge when you scale up that technology to massive sizes. We’ve previously seen companies such as BigRep, 3D Platform or Massivit bump into and solve scaling issues, but CADzilla is on an entirely different level. This machine is literally 7.2m (24ft) tall!
You might be wondering why a machine with a build volume of 3m has to be 7.2m tall, and that’s because of the machine’s design. Apparently Rosewell initially experimented with a KUKA robot arm equipped with a thermoplastic extruder, but found this approach to be inadequate. Studio Kite explains:
“A KUKA 125 robot arm was retrofitted with an extruder and trials began. After extensive tests and projects, the KUKA proved to be too slow with a loss of accuracy due to bounce. It was also dangerous. It became apparent that an original approach was needed. The outcome was to utilize a 4 motor Delta style parallel robot. This was an industry first on this scale. The engineering calculations proved it would be the only way to achieve high acceleration rates efficiently. The 4 motors design proved that if a motor malfunctioned, the other 3 motors would not let it move. Also, the lightweight design meant that powerful high torque motors were not needed. Potential injuries to an operator were mitigated by using a delta design. The 4 columns also allow for an improved print area.”
It appears Studio Kite ended up using a gigantic delta-style 3D printer
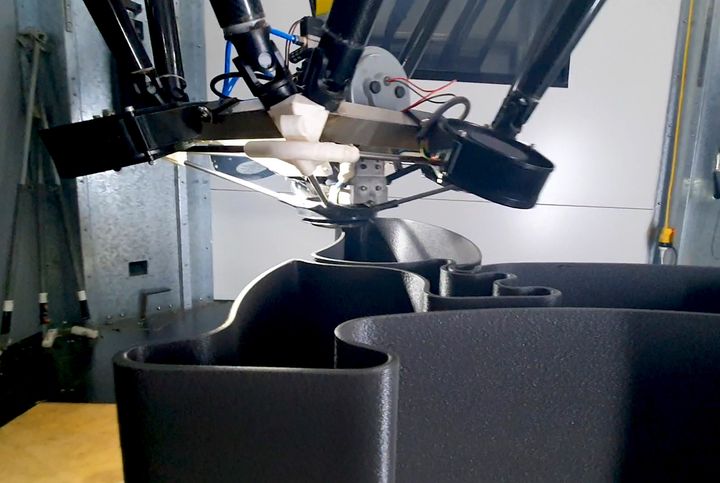
This is quite an interesting sequence of events, because there are several other 3D print initiatives intending on using robotic arms for 3D printing in just this way. It could be that Studio Kite has already encountered issues that might be seen in the future by other ventures.
I’m also impressed with their safety considerations, as that is sometimes poorly thought out by some other machine designers.
CADzilla Specifications
The result of their efforts is CADzilla, a 3D printer that has some significant specifications beyond the amazing build volume:
- Uses thermoplastic pellets and recycled chips rather than filament, which would be much more expensive
- Can extrude at 500mm per second!
- Layer heights as small as 0.2mm, but more frequently using 0.5mm for large prints
- Pneumatically controlled valve at the hot end to avoid drips and increase print quality
- Able to print quickly due to thin layers cooling faster than coarse extrusions
- Up to 30kg of thermoplastic material printed per hour, which is closing in on one tonne of material per day!
- Able to 3D print overhangs up to 80 degrees!
- Enclosed, insulated, heated chamber (up to 70C) for no-warp 3D printing — with double-glazed windows
- Water cooled hot ends
- Activated carbon air filtration system
- Carbon fiber delta arms
- Custom-designed operating system with real time control capabilities
Studio Kite explains that the cost of producing large props with CADzilla is approximately one-tenth the typical material cost and one-quarter the labor cost as compared to traditional making techniques.
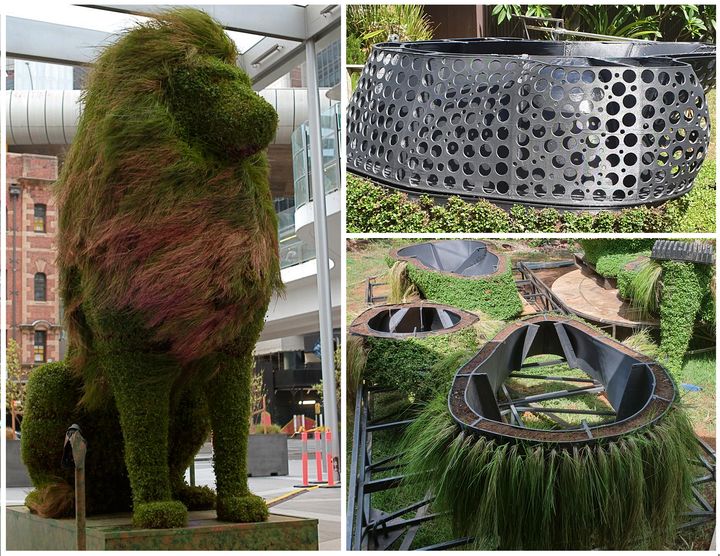
One of the interesting twists to this large-scale 3D printing approach is the internal structures of the prints. It turns out that many of Studio Kite’s 3D prints are hollow, with only the exterior shell being produced. This is because the interior of the 3D print is “almost always” equipped with a steel frame or scaffolding. I suspect this may be because the prints are often only parts of much larger pieces, and they require very strong frames to hold them together.
While the intent is to use recycled material, it seems that Studio Kite has been unable to source large volumes of suitable recycled ABS material. Instead, they are now experimenting with HDPE, which is much more easily obtained from recycling centers. HPDE is a tricky material, as it shrinks considerably when cooled, but they believe it is possible to successfully print in this material at large scales. Apparently they intend on developing a line of furniture and water run-off products using HDPE.
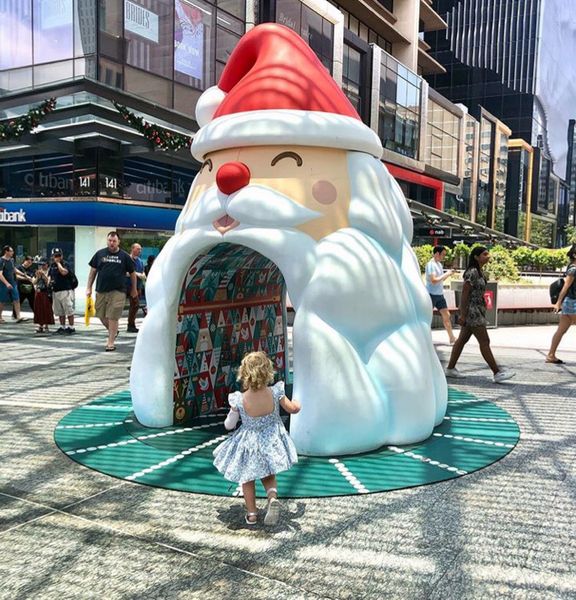
Clearly CADzilla is one of the most interesting — and largest — 3D printers on the planet.
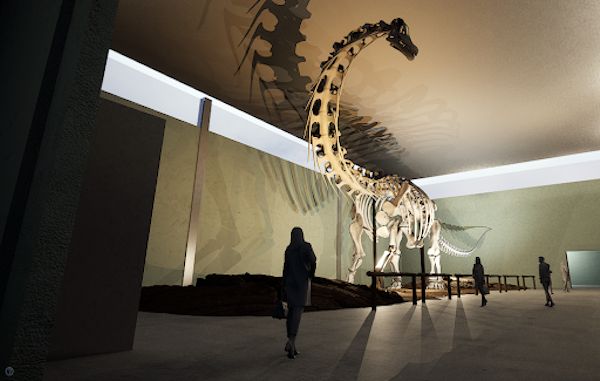
[FUN UPDATE] We’re told the CADzilla is now working on 3D printing a huge 28m long dinosaur sculpture (a Titanosaur, pictured here) for a Queensland, Australia museum.
Via Studio Kite