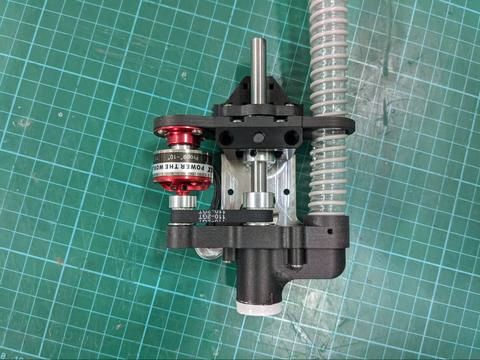
E3D-Online announced a new tool for their Toolchanger 3D printer that performs coordinated subtractive operations.
The UK-based company launched their highly unusual Toolchanger device as a “research platform”, and indeed that is how it is being used.
E3D-Online Toolchanger
The device attempts to overcome the problem of multi-material 3D printing, where the two other widely used approaches fail. The first style involved twinning the hot ends and extruders, but many found issues aligning the two, and drips from the “other” nozzle often ruined the print. The second approach involved using a single nozzle that solved alignment issues, but required wasteful “purges” to change colors.
The E3D-Online Toolchanger solves this by literally changing the extruder and hot end entirely using a motion system that picks up and drops off toolhead in a “garage” at the back of the build chamber. This allows hot ends to be ready to print immediately, and avoids alignment issues. It’s a very interesting approach that seems to work quite well.
But wait, there’s more!
This machine is a “tool changer”, not just a “material changer”. The toolheads parked in the garage don’t have to be extruder and hot ends, they can be any kind of useful tool.
As such, enterprising experimenters have begun to develop a number of unusual toolheads for the Toolchanger. One is a pick and place unit, shown in this video:
This tool allows the print job to include steps to drop embedded parts within the print itself. One can imagine this tool doing things like placing nuts, pins, circuit boards and more directly into the part, where they can be sealed in via subsequent print layers.
There are several more experimental tools being developed for the Toolchanger, but one seems extremely interesting: E3D’s own ASMBL toolhead.
ASMBL Toolhead
“ASMBL” stands for “Additive & Subtractive Manufacturing By Layer” and it provides a subtractive function that can be combined with other tools.
One prime function for ASMBL would be to smooth the external surfaces of a 3D print. The idea is to run the subtractive ASMBL tool along the edges of the print every few layers. This will maintain a smooth edge and the resulting 3D print will appear to be of injection-molded quality.
This approach has been used before in certain metal 3D printers, such as the Matsuura Lumex Avance-25. This metal 3D printer is a hybrid that includes a CNC milling head that smooths the metal surfaces during 3D printing. The results are excellent.
This approach is used in metal 3D printing because metal 3D printing processes often result in rather coarse surfaces. Milling can transform those rough prints into near-perfect parts.
ASMBL could do the same for polymer 3D prints.
However, I suspect it could only work properly on higher-temperature materials, as the milling process generates heat that might soften materials like PLA, or possibly even ABS. In their report, E3D says they’ve been experimenting with ASA and PEEK.
E3D says, however:
“We have no doubt that with further experimentation and testing we’ll be able to mill most, if not all, materials currently available. Hopefully flexibles too.”
That would be quite an achievement, I think.
ASMBL Debris Collection
Another challenge with a subtractive process is waste material. Normally in a 3D printer, which uses an additive process, there is little to no waste to handle during a print job. That’s definitely not the case with subtractive processes, as they by definition generate a great deal of debris.
This loose debris could work its way into the 3D printer’s motion system and mess things up, so E3D has included a vacuum system as is commonly seen on most CNC systems. This is a pipe system that can collect most of the shavings that come off the ASMBL toolhead.
ASMBL Software
A huge challenge for the ASMBL concept is software, as something needs to generate the correct GCODE to drive both the additive and subtractive processes. Typical 3D print slicing software handles only the additive actions, and CNC software handles only the subtractive actions. ASMBL needs both, integrated together to generate a unified tool path for all tools during a print job.
From initial experiments with scripts to merge 3D print GCODE with CNC code, they’ve now had a huge break as Autodesk has added 3D print slicing to their Fusion 360 product. This software already generates subtractive tool paths, so E3D created a Fusion 360 plugin to generate unified GCODE.
However, as slicers go, Fusion 360’s is pretty basic. While it’s a good start, they have a very long way to go to catch up to the likes of Ultimaker Cura, Simplify3D and PrusaSlicer. That may happen eventually, but for the moment it seems that the Fusion 360 plugin is sufficient for experimentation with ASMBL.
If E3D can perfect the ASMBL system it could be a game changer: near-perfect parts could be reliably produced without the need for expensive injection molds or wasteful CNC jobs. That in turn may attract more businesses to the technology, especially if they found “layered” 3D prints to be inadequate.
Via E3D-Online