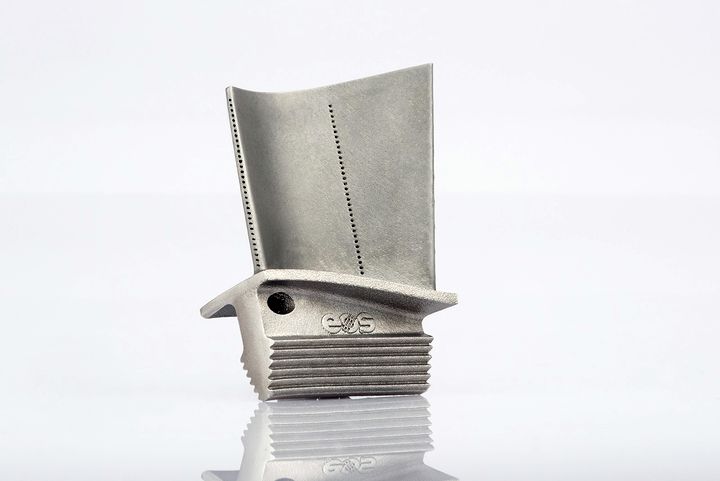
I’m reading a fascinating piece by Additive Manufacturing Consultant Michael Wohlfart discussing the different types of recoaters one might use.
Wait a sec, what’s a recoater?
3D Print Recoaters
For those who normally use filament or resin-based 3D printing, the concept of a recoater may be unfamiliar, as it is a component of neither process. Instead, it’s an integral — and perhaps the most critical — component of any powder bed fusion 3D printing process.
There are several variations of the powder bed 3D printing process that can be used to produce 3D objects in polymers or metals. EOS, for example, manufactures 3D printers for both types of materials, usually denoted by the “P” or “M” in their product name.
In a powder bed process a flat bed of fine powder is selectively energized to fuse the material together into a layer. Then, a second layer of fine powder is deposited on top, and the process repeats. At the conclusion of the print job, you’ll find the finished print buried in unused powder, which can sometimes be re-used on subsequent print jobs.
The “recoater” is the mechanism that lays down that layer of fine powder. It is critical to the process because:
- It must lay the powder down uniformly over a potentially large surface area
- The thickness of the powder layer deposition must be carefully controlled
- The recoating process must proceed quickly, as there is no 3D printing happening while powder is deposited
- It must be incredibly reliable, as PBF machines tend to be operated 24/7, with layer changes each minute
Some 3D printer manufacturers have even made their recoating process a competitive advantage, such as VELO3D. They’ve done this by very carefully designing and tuning their process, and it allows 3D prints to be made without much or even any support material.
Recoater Blades
But Wohlfart’s discussion revolves around the decision on which type of blade to use for recoating. The subject is far more complex than I had imagined.
The blade is the “business end” of the recoater, as it is the mechanism that pushes the powder to create the flat surface for subsequent energization. There are a number of considerations, including durability, because the harder the blade, the longer it will last.
You’d think that would end the discussion, but there’s more.
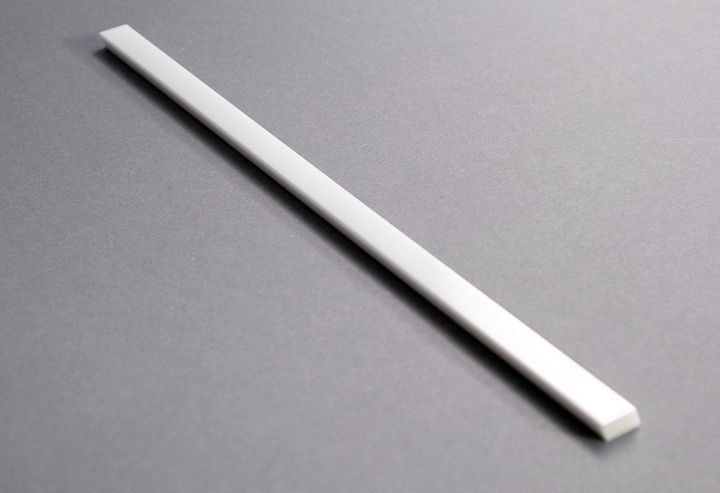
Some blades may be slightly magnetic and thus attract certain types of metal powder particles. That could mess up a print layer. In such cases you might consider using a ceramic blade.
Another consideration is collisions. In some rare cases a print layer may be ever-so-slightly taller than it should be, perhaps due to random movement of powder and spatter. On the subsequent recoat a rigid blade might actually strike this protrusion!
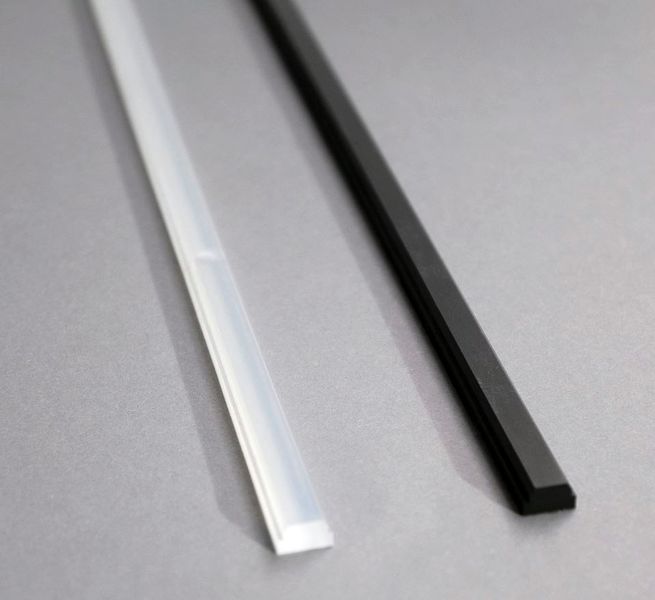
Such an impact could dislodge or bend the partial print, potentially ruining the entire print job. In such cases a soft blade, perhaps one made from silicone, might slide over the protrusion and allow the print job to continue.
Choosing A Recoater Blade
The answer to the question of blade type is thus not always obvious.
You might think that in the impact scenario above you’d want to immediately cancel the print job as there’s obviously something wrong. That could be the case, or perhaps not. Maybe the distortion is within the required parameters for that particular part, and printing could continue?
As in so many cases, the answer here is once again, “it depends”.
I recall my early days in the software industry, where I encountered two different philosophies: if the software encountered a problem — stop everything! Or, if the software encountered a problem — try to recover and continue. Both sides argued their point of view, but in the end I realized the answer depends on what the software is required to do. If it’s controlling a real-time situation, then perhaps you want to recover, or at least attempt to. On the other hand, if your system requires perfect results, then maybe stop and start over.
Much the same logic can be applied in this scenario. However, Wohlfart states his answer, which I agree with strongly:
“There is the appropriate use case for each recoater type. The hard recoater is considered by EOS as the standard option for parts with highest demands with regard to repeatable quality whereas a soft recoater enables parts with high aspect ratios. Furthermore, a soft recoater is preferred when lead time is more crucial than risk of imperfections.”
Always choose the right tool for the job.
For a deep dive on the topic of recoater blades, please read Wohlfart’s piece.
Via LinkedIn