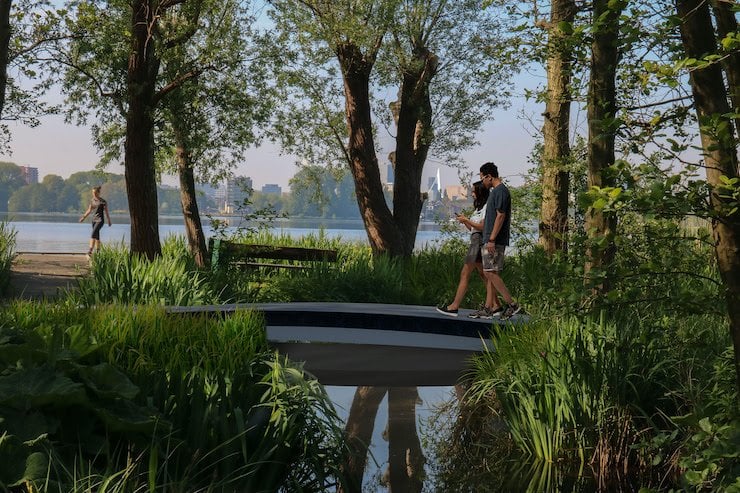
Progress has been updated on a fiber-reinforced polymer (FRP) footbridge to be 3D printed in Rotterdam.
Last year, we heard about a “world’s first” bridge to be 3D printed in the Netherlands, through work between DSM and Royal HaskoningDHV. At the time, the collaborators were noted to be engineering and project management consultancy Royal HaskoningDHV, global materials and general science company DSM, and large-scale 3D printing equipment supplier CEAD, but CEAD isn’t mentioned in this latest update. It’s possible their involvement does not stretch beyond supplying the 3D printing equipment, so there simply isn’t an update beyond ‘to 3D print this, equipment will be used.’ The City of Rotterdam is now noted among collaborators, which is certainly an important aspect in having the appropriate zoning and other considerations supported.
More details have emerged this week as progress continues on this project. DSM has announced that the bridge will be installed and in use in Rotterdam’s Kralingse Bos park before the end of this year.
3D Printing A Bridge
Many of the technical aspects remain as announced in September. The bridge will be 3D printed using DSM’s fiber reinforced thermoplastic Arnite material, which is a glass-filled thermoplastic PET combined with continuous glass fibers. While it may seem strange to make a load-bearing structure from plastic, several polymer bridges have already been 3D printed around the world, and these materials fit in with the idea of sustainability.
DSM highlights the “next generation of bridges” as structures that will offer “high performance with extreme versatility, circularity and sustainability.” Such focuses are important to the Dutch company, which has carried its visions of a more sustainable future for manufacturing into its young 3D printing business.
They also name Rotterdam as a “dynamic, innovative city at the forefront in the use of composite bridges,” which may seem like sort of a niche peg to hang a hat on, but that actually “underpin[s] the city’s drive towards circularity and sustainability.” Rotterdam is among the Dutch cities to rely heavily on footbridges — with more than 1,000 bridges in just this city — so certainly great thought has gone into how to enhance these structures to stand up to heavy foot traffic and do so in a sustainable way, with lower costs of maintenance and lifecycle.
“The city of Rotterdam is proud to be a leader in the smart and circular use of composite bridges. Together with Royal HaskoningDHV and DSM, we are continuing to push the frontiers of sustainability for bridges, using thermoplastics which will enable greater circularity. The 3D-printed FRP footbridge as a circular composite aligns with our city’s ambitious sustainability targets to reduce carbon footprint and promote liveability and we are proud to be the first city to test, print and install it,” said Asset Manager from the City of Rotterdam Mozafar Said.
DSM’s Patrick Duis, Senior Application Development Specialist Additive Manufacturing, adds that the 3D printed Arnite bridge will serve as a transition to “a more sustainable and circular type of bridges with minimal wear and tear.”
“Now that we have the new circular composite of recyclable source material along with the required performance properties available to us, we can start taking the environment-friendly design of the infrastructure to the next level,” he added.
The Digital Twin?
In the initial September announcement, the partners noted that sensors would be included to create a digital twin of the bridge.
At that time, Maurice Kardas, Business Development Manager at Royal HaskoningDHV, explained:
“By including sensors in the design, we are able to build a digital twin of the bridge. These sensors can predict and optimise maintenance, ensure safety and extend the life span of our bridges. It can also incorporate new functionalities such as monitoring vital environmental aspects and improve the decision-making process for maintenance and inspection via dynamic real-time reports on the condition of the bridge. In collaboration with these industry leaders, we are transforming the traditional playbook when it comes to bridge design and construction.”
Now the statement seems a little less clear regarding that digital twinning, as this week’s announcement states:
“Sensors could also be included into the footbridge to build a digital twin of the bridge. The sensors can predict and optimise maintenance, ensuring safety and extend the life span of the bridge.”
With the project in progress, and installation on the horizon within the next five months, time will tell how this 3D printed bridge shapes up, as well as if and how sensors are ultimately incorporated.
Via DSM