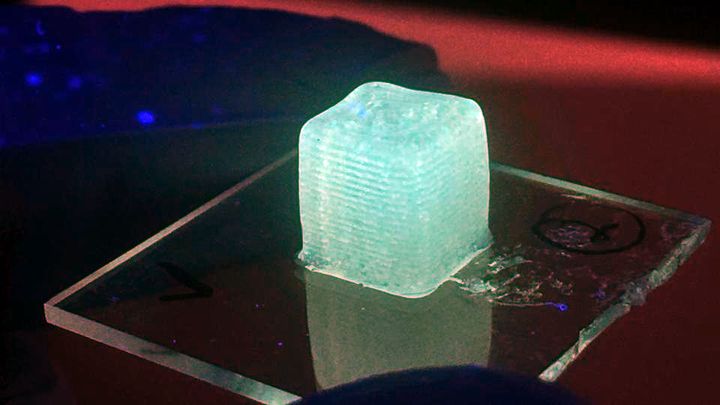
Researchers as UC Davis have developed an unusual new form of 3D printing that uses Droplet-Based Multiphase Emulsion.
One of the big challenges in 3D printing is the inability to handle multiple materials. Typical 3D printers of today can 3D print a single material at a time, with certain more advanced models being able to print with a small handful of different types.
This is generally not as useful as it could be, as typical functional objects are composed of many materials. Usually the different materials are chosen because they provide different engineering properties for different segments of the object. For example, a rigid material might form the case, while a soft rubbery material might form a grip layer on the case.
One of the UC Davis researchers, Jiandi Wan, observed that the nozzles used in 3D printing were quite similar to those used in microfluidics equipment, but that they were quite rudimentary. Wan wondered whether the complex microfluidics nozzles could be leveraged in 3D printing.
It turns out they can.
Droplet-Based Multiphase Emulsion
In the experiment, the researchers were able to add a tiny capillary nozzle to a 3D printing system. This apparatus was able to deliver controlled amounts of droplets of a second material into the main material stream. The droplets were small enough to effectively form an emulsion upon deposition.
By varying the amount and timing of droplets, the researchers were able to modify the properties of the resulting 3D print.
For example, they were able to control the rigidity of the material, able to produce a range of softness within a print on demand. The system apparently can accept ”aqueous and liquid metal droplets”, suggesting that a variety of different properties could be enabled within a 3D print material using this approach.
In fact, in the paper they say:
“The application of microfluidics for multiphase or immiscible ink blends (i.e., emulsions) in a 3D-printing context remains largely unexplored.”
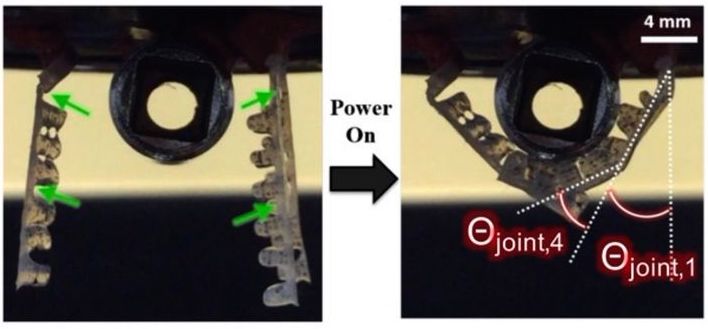
Their exploration at this point seems to be in developing practical methods for 3D printing variably flexible objects, and adding ferric characteristics, which is quite a feat. However, I suspect this approach could have far deeper implications.
Microfluidic 3D Printing
There’s a couple of interesting ideas here.
First, imagine 3D printing an object, but with the ability to continuously vary the hardness of the material. I don’t think such objects even exist today, but if an approach to produce them were popular, we could see them everywhere.
They might have designs reminiscent of today’s foam-like structures generated by FEA systems, except appearing solid yet having complex flexible streams flowing within. New analysis software might be required here, of course.
Now imagine further where this 3D printing approach is able to control not only flexibility but also other engineering properties by adding different droplets and creating unusual emulsions. Part of a print could be magnetic, another flexible, another conductive, transparent, etc. You get the idea.
Again, we’ll need some new and highly complex software to manage that awesome capability.
One more thing:
While the authors of the paper are Hing Jii Mea, Luis Delgadillo, and Jiandi Wan, the paper also says this:
“Edited by Joseph M. DeSimone”.
Dr. DeSimone is none other than the founder of Carbon, one of the leading companies producing 3D printers.
I wonder where this technology might go.
Via UC Davis