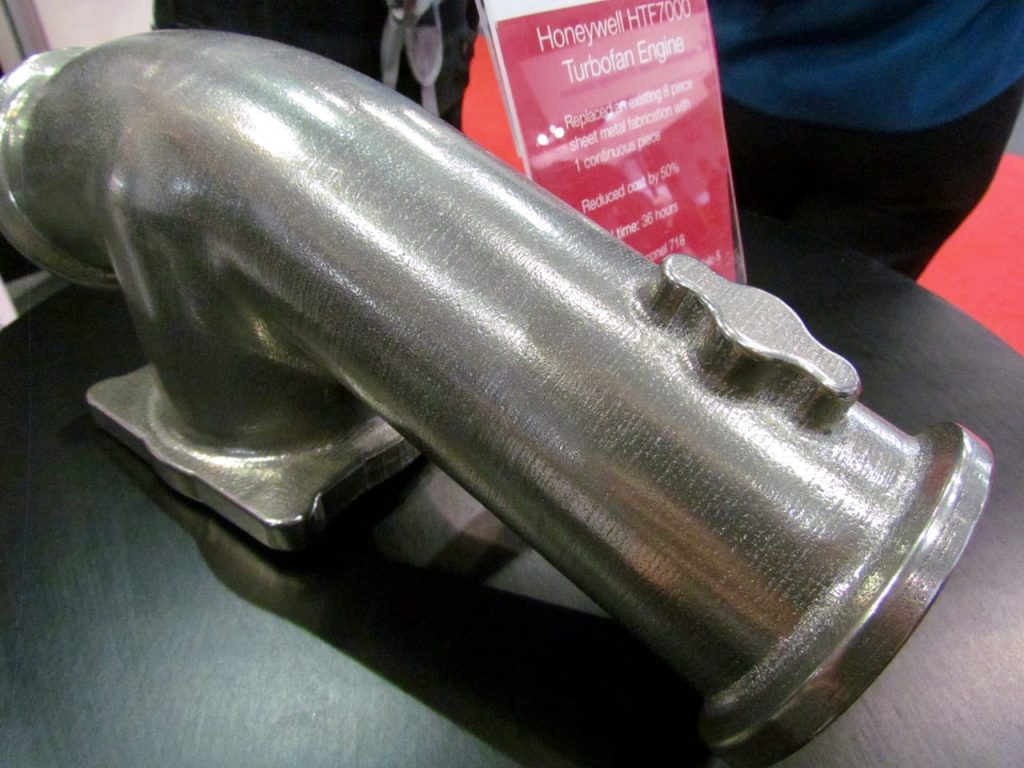
GE announced it is cutting loose another 13,000 jobs, and this may have big implications for the 3D printing industry.
Like many companies in the coronavirus era, GE is facing struggles, but perhaps more than most. While some operations are actually quite busy during the crisis, others have seen a drop off in sales as people stay home and conserve cash.
But one industry that’s taken the hugest hit has been the airline business. Due to border and travel restrictions, loss of salaries, and general fear of contracting the virus, many people are simply not flying anywhere. In many cities you’ll see flight schedules down under 10% of what they were only a few months ago. In some cases there are only a handful of flights. Airlines are desperately trying to make some cash by repurposing their fleets into rudimentary cargo carriers, but that’s not going to be enough.
Some carriers have postponed or even cut their orders for aircraft from manufacturers. There’s plenty of debate about when and how much the airline travel industry will recover. Some say a year or two; other say at least five years. Some even suggest it may never recover to previous levels as the idea of travel has changed utterly in many people’s minds. Businesses have discovered that it is actually possible to work remotely, meaning they’ll likely do more of that in the future instead of expensive physical travel.
All in all, it’s a bleak picture for airlines, aircraft manufacturers and their component suppliers.
One of them is GE.
GE Additive Manufacturing
GE was perhaps the pioneer in 3D printing technology for the aerospace industry. It was they who spent years experimenting with metal 3D printing to eventually determine ways to develop radically new designs for parts that could only be made using additive manufacturing techniques.
These parts made GE’s offerings more competitive as they were lighter — a very valuable property in aerospace — and providing equal or better functional performance.
Their success led a transformation in aerospace manufacturing in which metal 3D printers became far more popular. The move at GE in this direction was so strong they even bought not one, but TWO metal 3D printer manufacturers to ensure they were on top of the technology. They established a dedicated business, GE Additive, to roll in the acquired company operations with their own in-house offerings in the technology.
With plenty of orders for components coming in, the thinking was they would organize arrays of metal 3D printers to produce volumes of required parts on demand.
But now that’s changed, as customer demand has dried up.
Implications on Metal 3D Printing
This is most definitely not good news, as the demand shrinkage cascades down through to the suppliers and their suppliers. Ultimately it likely means the market for metal 3D printers has very significantly dropped, as aerospace was one of the leading buyers of the new technology.
It is also bad for GE in that they produce their own metal 3D printers under the two brands they acquired, Arcam and Concept Laser, as well as under their own GE Additive brand. It’s likely these will all see demand for their 3D printers drop significantly.
This is quite unfortunate, and I hope GE will recover as soon as is possible. Meanwhile, GE has set a standard for using metal 3D printing in manufacturing that has been observed by other industries. There are other industries besides aerospace that have begun a transformation, and that might not have happened unless GE had taken the steps it did.
Via CNN