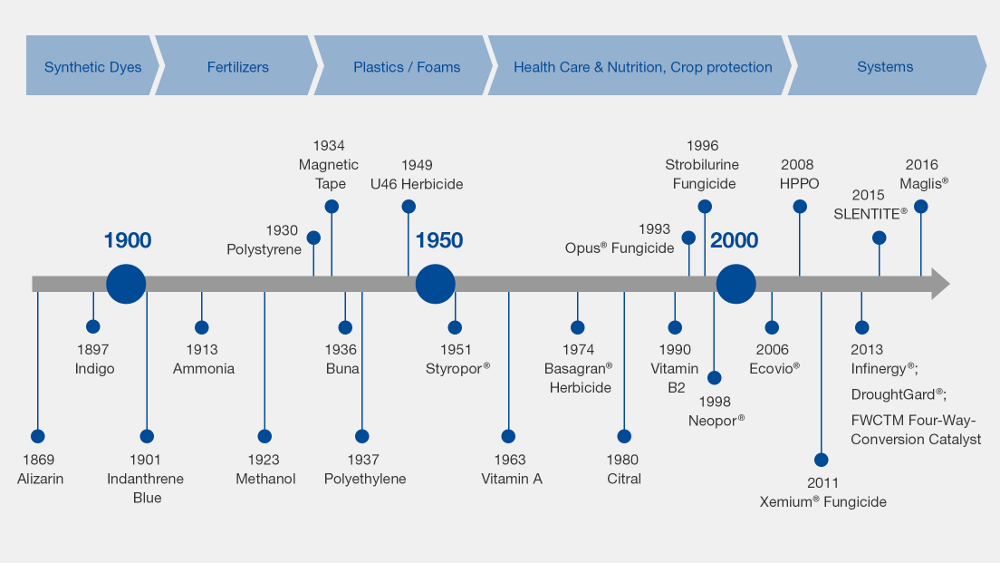
Charles Goulding and Preeti Sulibhavi examine BASF’s involvement in 3D printing.
We all know BASF “creates chemistry.” It has done so for well over a century, at a level that sets a high bar for its competitors. Created in 1865 as Badische Anilin und Soda Fabrik, “Baden Aniline and Soda Factory,” BASF SE was established to produce chemicals necessary for dye production, notably for soda and acids.
The #1 global chemical producer has a product announcement seemingly daily. The BASF group’s 12 divisions are divided into 4 segments (chemicals, performance products, functional materials & solutions, and agricultural solutions) based on their business models. In 2019 this will grow to 6 segments, and these segments will manage the 54 global and regional business units and develop strategies for 86 targeted product areas. Innovation runs deep at BASF.
Early on, BASF has made major investments in 3D printing materials technology. The fact that a global chemical giant like BASF would enter into such a leading-edge investment is actually quite remarkable. While large economic returns may not pay at this moment, we believe BASF’s investment in 3D printing technology will pay off in the long run.
The Research & Development Tax Credit
Enacted in 1981, the now permanent Federal Research and Development (R&D) Tax Credit allows a credit that typically ranges from 4%-7% of eligible spending for new and improved products and processes. Qualified research must meet the following four criteria:
-
Must be technological in nature
-
Must be a component of the taxpayer’s business
-
Must represent R&D in the experimental sense and generally includes all such costs related to the development or improvement of a product or process
-
Must eliminate uncertainty through a process of experimentation that considers one or more alternatives
Eligible costs include U.S. employee wages, cost of supplies consumed in the R&D process, cost of pre-production testing, U.S. contract research expenses, and certain costs associated with developing a patent.
On December 18, 2015, President Obama signed the PATH Act, making the R&D Tax Credit permanent. Beginning in 2016, the R&D credit can be used to offset Alternative Minimum tax for companies with revenue below $50MM and for the first time, startup businesses can obtain up to $250,000 per year in payroll taxes and cash rebates.
The New BASF Creation Center
BASF’s new Creation Center to open in Ludwigshafen in 2019 will be a unique facility where BASF designers develop new products with customers on the basis of material samples. BASF’s own Ultrasim simulation technology complements the combination of computer-aided methods with the latest visualization technologies and 3D manufactured sample components, in this center where real world materials meet the latest digitalization. In collaboration with Holo-Light, a startup company, an application was jointly developed where simulations can be displayed three-dimensionally as holographic superimpositions. Utilizing mixed-reality glasses, interactive 3D projections such as components or furniture can be shown in the immediate vicinity. This makes material properties well recognized and complex geometries easier to understand as well.
Thermoplastic Polyurethane (TPU) Powders
BASF offers complete material solutions and their portfolio comprises different polyamide and TPU powders. Their portfolio also consists of numerous plastic and metal filaments and photopolymers. While BASF recognizes 3D printing is in its earliest stages, it draws on the immense innovation power of its chemical history to fuel it with creativity and development work. BASF understands that 3D printing is an interdisciplinary field where a network must be established for strong market cooperation.
BASF and CTIBiotech: Sebaceous Glands Technology for Skin Care Applications
Sebaceous glands help the skin stay hydrated and protect it against external elements (e.g., harsh weather, pollution, microbial infections). Using CTIBiotech’s 3D human sebaceous gland technology, scientists at BASF were able to improve their 3D skin model capabilities. This new 3D technology provides a powerful platform for skin care researchers wishing to study the function of sebaceous glands, in relation to a host of age-related, microbial and inflammatory skin diseases.
BASF’s 2018 3D Printing Innovation Initiative Timeline
Below is a summary of just some of BASF’s 2018 innovation initiatives evidencing the major commitment they are putting into 3D printing.
July 4, 2018 – The creation of BASF 3D Printing Solutions (B3DPS).
July 19, 2018 – BASF creates a framework for optimizing software used in 3D printing. The agreement allows for systematic, wide-scale testing and optimization by introducing product testing and further optimization and involves a $25 million investment into Materialise.
November 6, 2018 – BASF invests in Prismlab to improve large-scale component production. It is the first direct investment by BASF Venture Capital made in China.
November 12, 2018 – BASF announces 3D printing solutions by presenting a pioneering strategic alliance for industrial 3D printing. New products for photopolymer and laser sinter printing methods were announced from B3DPS that would combine BASF’s material know-how with Origin’s expertise in printer software programming and the manufacturing of complementary hardware.
November 14, 2018 – BASF, Materialise and Essentium collaborate in advancing additive manufacturing. In an effort to combine the software development with the global materials supply chain that supports the additive manufacturing platform, BASF is contributing comprehensive material know-how.
Creating Chemistry in 3D
With all of the innovative ways in which 3D printing technology is utilized, BASF appears to have taken two approaches to establishing itself in this market. BASF has collaborated with various technology companies and startups in creating state-of-the-art new technology to be applied in ways not thought of before. BASF has partnered with HP Inc. to be a part of its 3D Printing Ecosystem. At the rate 3D printing is growing, this day may not be too far off. BASF can improve its applicable technologies, its efficiency and benefit from R&D tax credit incentives all while utilizing 3D printing.