![Phil, Vladimir, and Markus embody the spirit of togetherness driving additive manufacturing forward [Image: Sarah Goehrke/Fabbaloo]](https://fabbaloo.com/wp-content/uploads/2020/05/IMG_20181213_140150_img_5eb0a07d92b53.jpg)
Following a tour of the new additive manufacturing facility at Materials Solutions, a Siemens business, I sat down for a chat with company executives.
Markus Seibold, Vice President Additive Manufacturing, Siemens Power & Gas; Vladimir Navrotsky, CTO of Siemens’ Power Generation Service; and Phil Hatherley, General Manager, Materials Solutions offered insights into strategies and capabilities as Siemens continues to focus on the industrialization of additive manufacturing.
“Siemens is here to deliver on the promise of additive manufacturing, and is getting into position to move into production,” Hatherley said. “With the history at Materials Solutions and growing capabilities of the technology, we wanted to show customers, and the Siemens team, how we can deliver. The grand opening had that wow factor. It’s not all there now, but we have the vision to move forward, and feedback has been overwhelmingly positive.”
The facility’s grand opening was held the day ahead of the press tour, as dozens of customers and team members from broader Siemens operations gathered at the site in Worcester, UK. The 4,500-plus-square-meter facility currently houses 19 3D printing systems and has the capacity for 50 machines, as growth in scope is built into the plans.
![Phil leads the way through the print farm [Image: Sarah Goehrke/Fabbaloo]](https://fabbaloo.com/wp-content/uploads/2020/05/IMG_20181213_112002_img_5eb0a07e4589d.jpg)
Growing on-site capabilities are built upon a foundation of concurrent growth in team expertise and in technological capabilities. Expertise comes, of course, from a deep understanding of a full process, and Siemens’ focus is toward that end-to-end comprehension and delivery.
“There’s 3D printing and there’s additive manufacturing,” Seibold said, picking up on a thread from earlier presentations discussing the full technology suite in focus at this particular advanced manufacturing site.
“When most people think additive manufacturing, except for very educated customers, they think it’s having a 3D printer and pressing print. What we hope people saw is that, yes, a printer farm is a key element of the site and is key to what’s possible — but walk out of the printers and into the quality inspection room, then into post-processing, then depowdering, and soon into a CNC area, and you see it’s way beyond 3D printing. This is toward the Internet of Things, process controls, hardware and software management; it’s a digital factory. We take digital models into production machines, we simulate performance; Siemens’ vision is way beyond 3D printing. Additive is way more than this.”
Transparency and communication are integral to Siemens’ strategy. More than just a nice throughline for visitors and media to latch onto, refreshingly Siemens seems to truly mean it. Just as additive manufacturing needs more than 3D printing to successfully industrialize, the team at Materials Science and parent Siemens need more than internal know-how to push forward.
![Materials Solutions has a long history with EOS and powder bed technologies, Phil explains [Image: Sarah Goehrke/Fabbaloo]](https://fabbaloo.com/wp-content/uploads/2020/05/Phil_img_5eb0a07eb9ae6.jpg)
Collaboration, cooperation, co-creation: all are terms familiar to anyone with more than passing acquaintance with the 3D printing industry, as these turn up as popular buzzwords at nearly every conference and event. Beyond the buzz is an underpinning of understanding, as no single company, no single technology, represents the singular way ahead in this next Industrial Revolution (because there isn’t one). Industry 4.0 hinges upon many technologies, and these are built by many companies — and Siemens just so happens to have a hand, conveniently, in many of these.
Siemens acquired Materials Solutions in 2016, giving the company not only name recognition but access to its new parent’s broad portfolio of operations and extensive network of resources. Focus on especially powder bed technologies is creating targeted expertise, which is being proved out through marked milestones as well as Siemens’ positioning as both user and service provider in additive manufacturing.
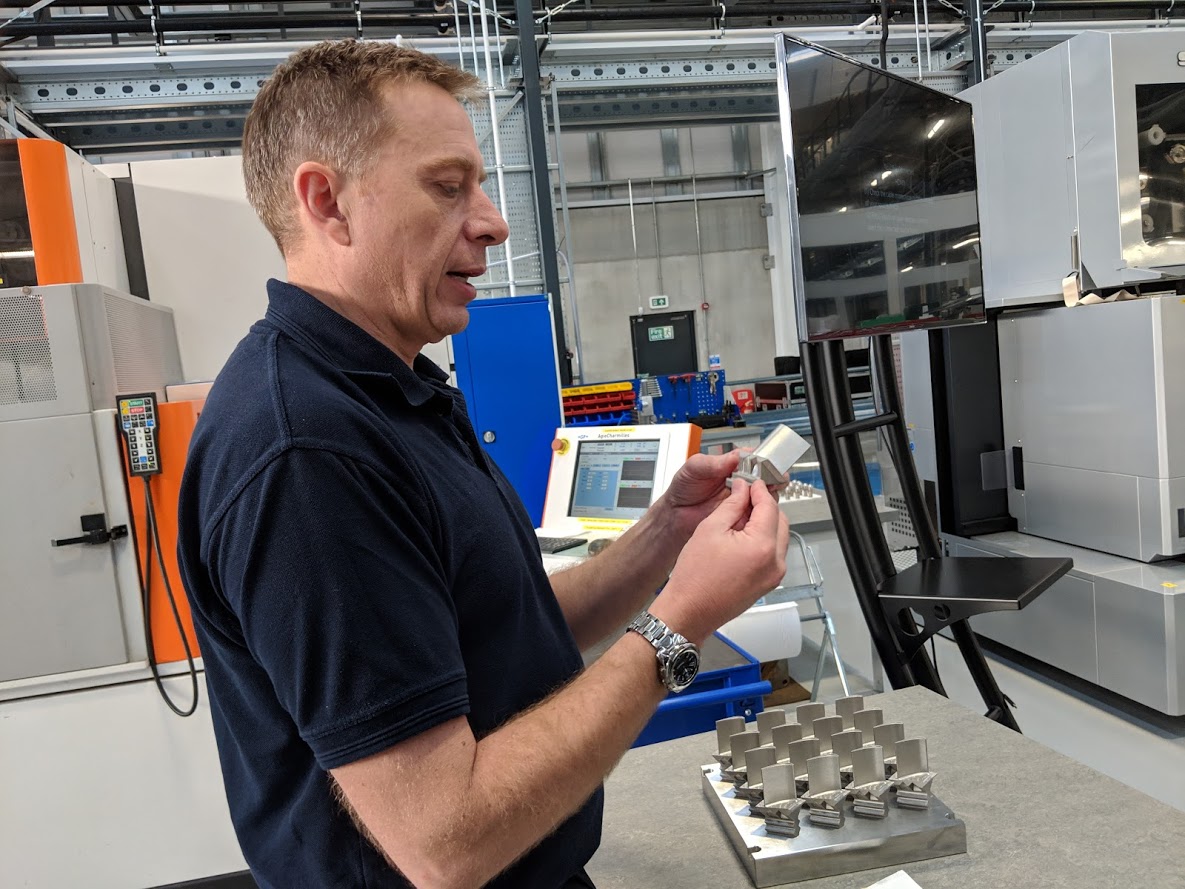
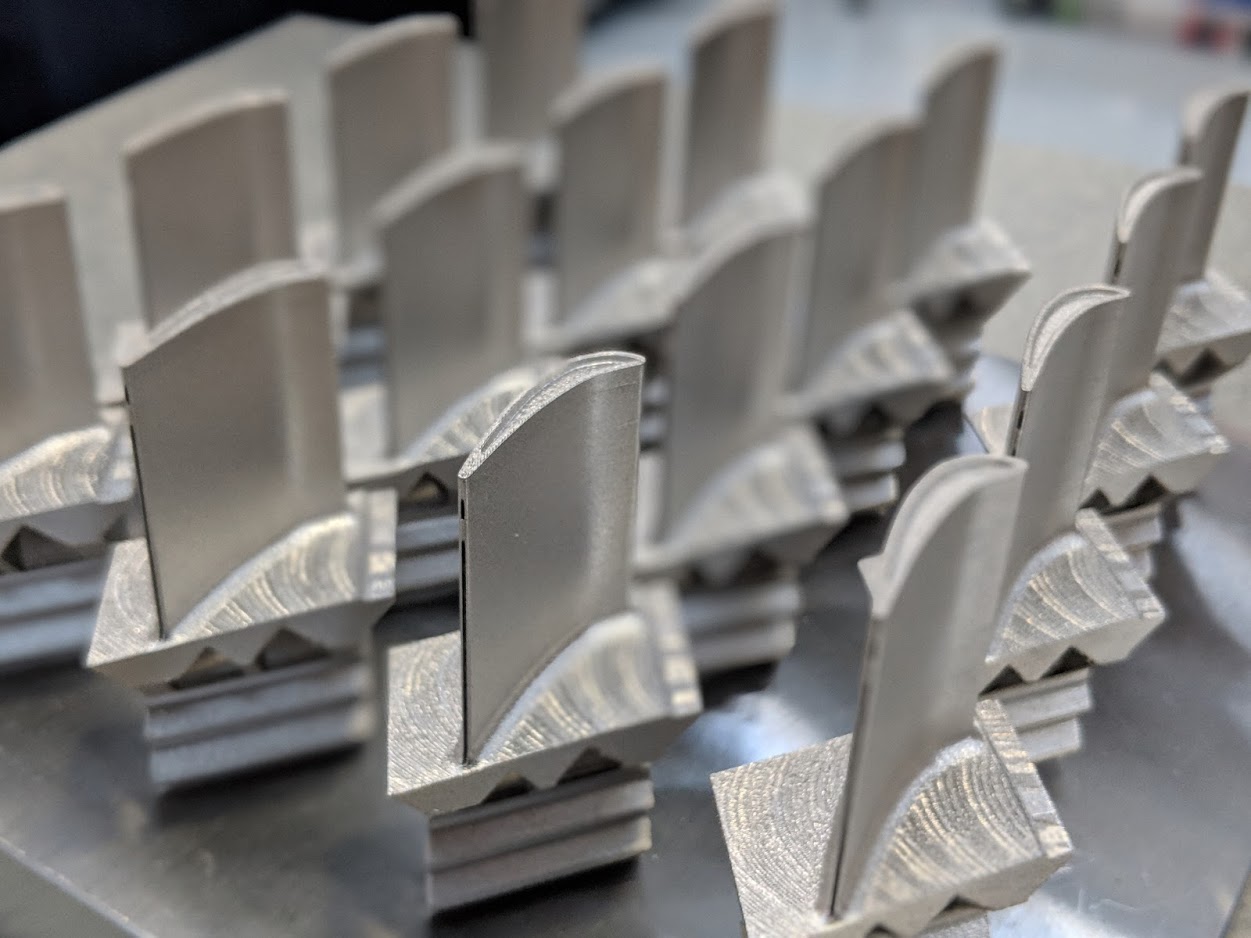
The promise of additive manufacturing is promising indeed: freedom of complexity, bespoke parts, customized designs, savings in cost, time, materials, labor. Most has as yet been unfulfilled as additive manufacturing remains a long game.
“We need to create the right expectation; we are not ready to print any product wanted, we are at the beginning of this journey,” Navrotsky said evenly. “There’s a lot needed to be done, it’s not a simple ‘push the button and the parts come out’.”
On the wall is an unmissable message in large block letters:
“Together we lead the Additive Manufacturing REVOLUTION”
![[Image: Sarah Goehrke/Fabbaloo]](https://fabbaloo.com/wp-content/uploads/2020/05/IMG_20181213_084722_img_5eb0a0804f5b9.jpg)
That’s more than just a nice, catchy phrasing for the break room wall, Seibold said as we wrapped up our chat. They mean it. (Though it helps that it’s catchy.)
“Together with our customers, together with our team, we are leading this additive revolution. There’s a lot to that ‘together’. It is collaboration with suppliers, it is co-creation with customers. We all face the same problems: adoption rates are too slow, there is not enough revenue for investment. We all help each other — together. It puts it in a catchy phrase, but there’s a lot to that,” Seibold concluded.
For Siemens, working together is the only viable way along the next step on this long journey. Because of the company’s position as both user and service provider, internal and external relationships alike are necessary components to core strategic approaches.
Navrotsky added, “Together means focus on the right things.”
The words may be grand, but the vision is grounded.
We can expect great things to emerge from this newly opened facility as it — and the industry — continues toward growth and toward the fulfilment of promises decades in the making.
Via Materials Solutions and Siemens / All images: Sarah Goehrke/Fabbaloo
Volumetric 3D printing could be the biggest shake-up in 3D printing history. But who is working on the technology? We made a list.