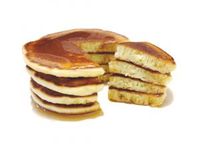
Subtractive manufacturing can be wasteful. Consider the titanium cube that might be milled down to a final object comprised of only 10% of the original cube’s mass. Sure, you might be able to recycle the shaved-off bits, but that’s not going to be efficient.
Step forward to the 21st century where we have “Additive” manufacturing. In this approach there is no original material to subtract from. Instead, we simply deposit new material in an “additive” way to gradually build up an object from nothing. We do this with extruders, laser sintering, powder fusing and other approaches. But they are all additive.
Or are they?
Consider the case of Solido and MCOR, who use sheet-based additive manufacturing approaches. In this approach, a flat sheet represents a layer that is added. Then the machine removes (subtracts?) the areas of the sheet that are not required. The question then is, are MCOR and Solido additive or subtractive? We think they are both because they add layers, but subtract from each layer.
To print on one of these machines you must visualize the input material: a stack of sheets, plastic or paper. Your object has to be contained within that stack. So like Michelangelo, we believe every stack has an object hidden inside. Even pancakes.