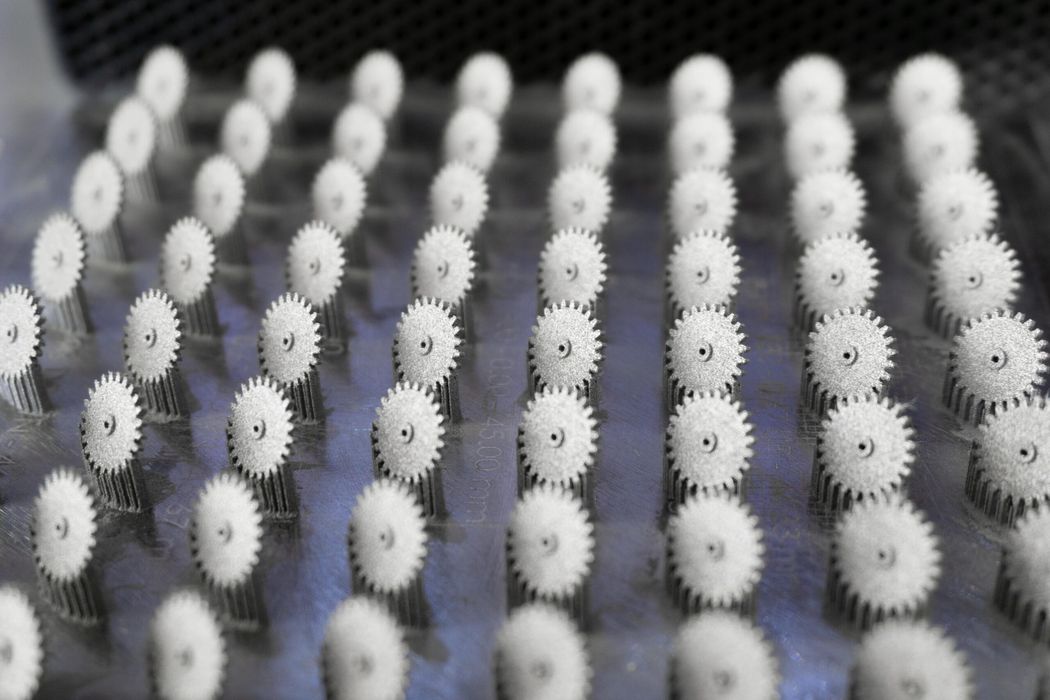
Xact Metal continues their move into the tooling industry with a key partnership.
The small Pennsylvania company produces a relatively inexpensive LPBF metal 3D printer for industry, which has been well-received by customers. While their orders are up over year’s, they’re constantly looking for new applications.
They hired on specific engineers to assist developing customer applications, but have specifically been focusing on the tooling industry. Manufacturers require all manner of tools to assist the production of parts, and many of them are made from metal.
A common tool is a mold in which plastic materials are cast. Injection molding is a fairly rapid method of production, but there is a catch: the metal molds eventually heat up, collecting energy from the hot injected plastic materials.
That’s a problem because the casting process isn’t complete until the plastic sufficiently cools down for removal. If the mold is already hot, then there’s more cooling delays. The ideal approach is to actively cool the mold.
Cooling a mold is typically done by including small conformal channels in the mold through which cold water can flow. The water captures some heat and carries it out of the mold.
Even better, 3D printing is the ideal approach to produce metal molds with conformal cooling channels: the technology allows complex channel geometry to achieve optimal cooling profiles.
This all sounds terrific so far, but there’s a problem: most of the 3D printable metal materials have a problem with the water: they corrode. This makes the molds usable for a shorter working lifetime, and that adds cost and time to the production process.
Xact Metal has solved this issue with a new partnership with Uddehome. Uddehome is a 350 year old Swedish producer of high quality tool steel alloys.
One of their products is Corrax, a proprietary tool steel. Uddehome describes Corrax:
“Uddeholm Corrax is a precipitation hardening steel with a unique set of properties that makes it perfect for many demanding applications. The superior resistance against corrosion combined with a hardness up to 50 HRC and a simple heat treatment makes Uddeholm Corrax the obvious choice for long run series of aggressive plastics such as PVC.”
Note that they’re talking about corrosion from PVC material, not water, suggesting that molding can be done in a wider range of materials in addition to cooling advantages.
The partnership will put Corrax material into Xact Metal’s 3D printers with a new metal powder option, allowing customers to print highly complex injection molds with conformal cooling channels that last a very long time.
This may seem like a minor product change: Xact Metal adds another tool steel. However, if you look behind the headline and think about what this material can actually do for manufacturers it is quite significant.
Xact Metal is very likely going to score quite a few more manufacturing customers as a result of the introduction of Corrax.
Via Xact Metal