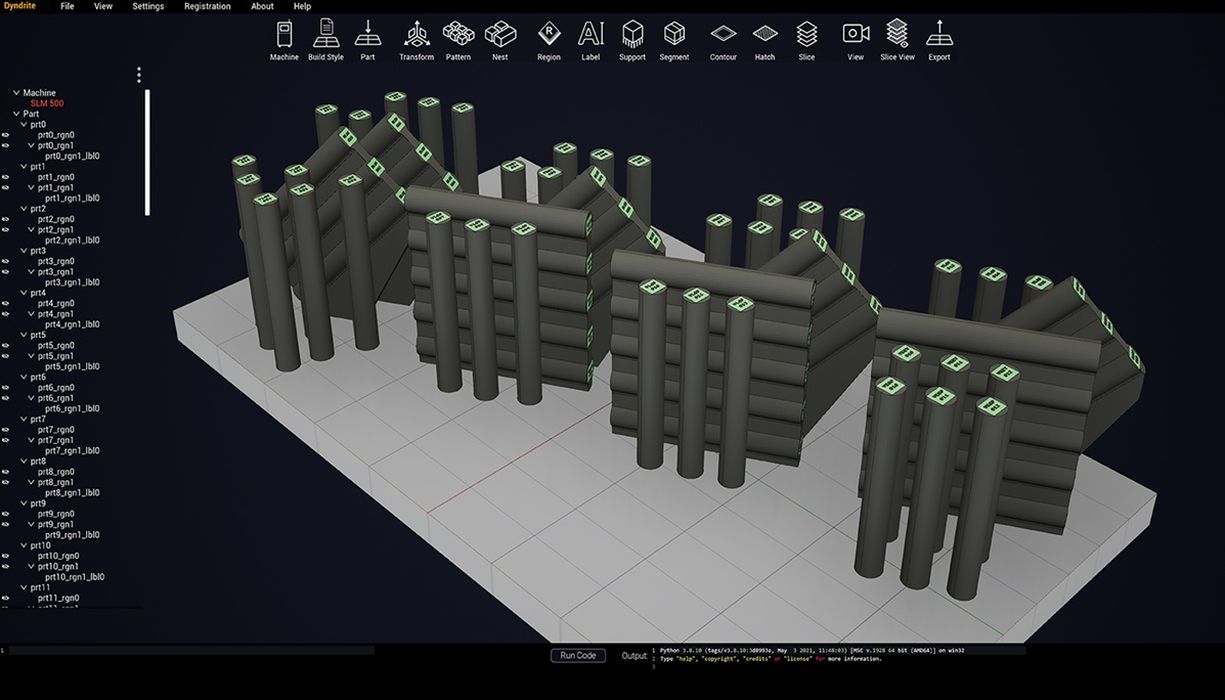
At AMS 2025, I heard an interesting angle on print profiles from Dyndrite CEO Harshil Goel.
Goel’s company produces advanced software to prepare 3D print jobs for LPBF and MJF equipment. They explain how it works:
“Our flagship product, the Dyndrite Accelerated Computation Engine (ACE), is a tool that gives hardware and software companies the power, freedom, and control necessary to deliver the future of digital manufacturing. This multi-threaded and GPU-accelerated software delivers eyebrow-raising performance, Python automation, and one of the most accessible app development environments in the engineering and manufacturing industry. It helps our customers solve the toughest geometry and compute problems on the planet.”
In Goel’s talk, he described what might be called the “one parameter set problem”.
The idea here is that when an organization qualifies a product and material for use in that organization, they typically end up with a single print profile for the equipment and specific material. This profile is then used for any parts produced using that pair of machine and material going forward.
This is the way that it’s been done for decades. Manufacturers need to consistently produce identical parts, and they therefore need a standard to use during production. Having a qualified print profile makes that easy.
Or does it?
Goel’s proposal is that while a print profile may work optimally for a specific test part used during qualification, it may not be as optimal for other parts.
This is because geometries of parts change. Different parts may require slightly different variations of print profiles to achieve the best results.
But if the organization’s approach is to simply use the qualified profile, then less than optimal results will happen. This is not a good situation at all.
The correct approach would be to re-qualify a profile for a specific part, matching three factors instead of two: machine, material, and part.
But that’s usually not happening because the qualification activities are usually quite expensive, and a company would want to do them only once. This is very likely a barrier to the adoption of 3D print technologies by many organizations.
Dyndrite hopes to break through that barrier with their advanced software. They explain:
“Leverage GUI and Python programmable tools to develop new parameter strategies and optimize routines. Streamline materials & process development, accelerate repeatable qualification processes.”
As industry continues to adopt additive manufacturing as a production option, issues will surface and need to be addressed. Here Dyndrite has taken on a significant problem and created a solution.
Via Dyndrite