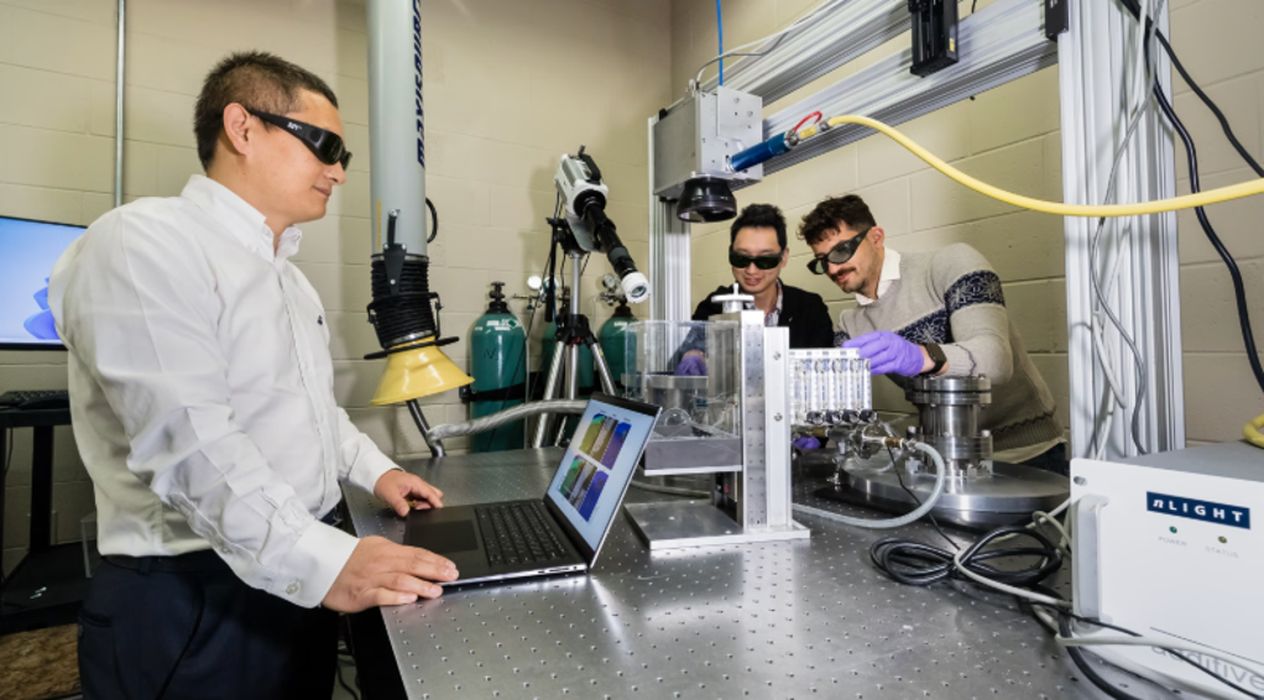
Here’s a comparison of various metals the aerospace industry uses to additively manufacture parts.
Of all the industries that have benefited from 3D printing, aerospace is one of the most prominent. The ability to create strong, lightweight parts through additive manufacturing (AM) presents numerous opportunities in aerospace and aviation applications.
“Aerospace is one of highest consumers of 3D printing applications,” said Chukwuzubelu Ufodike, director and assistant professor at the Digital Manufacturing and Distribution lab at Texas A&M University. “It uses very specific parts that cannot be manufactured with conventional methods.”
The aerospace industry has used both metallic and non-metallic materials in 3D printing. This article focuses on metallic materials and the differences in the most popular choices.
Types of metal AM processes
Metal AM processes can be classified into the following categories:
- Binder jetting uses a liquid binding agent on metal powder to “glue” the powder particles into a desired shape. It is sometimes likened to an inkjet paper printing process.
- Powder bed fusion uses lasers or electron beams to fuse small particles of powder into a 3D mass. This includes subtypes such as selective laser sintering (SLS), multi-jet fusion (MJF) and direct metal laser sintering (DMLS).
- Directed energy deposition uses lasers or electron beams on metal powders or wire. The 3D printing apparatus is usually attached to a multi-axis robotic arm and consists of a nozzle that deposits metal powder or wire on a surface and an energy source that melts it, forming a solid object.
- Material extrusion works by heating a filament that is drawn through a nozzle and deposited on a build platform, layer by layer. Extrusion processes include fused deposition modeling (FDM) and fused filament fabrication (FFF).
Metals for AM in aerospace applications
Various types of metals can be used for additive manufacturing. In the aerospace industry, the following types are most common.
- Titanium — Perhaps the most prominent metallic AM material in aerospace, titanium and titanium alloys offer high strength-to-weight ratios, excellent corrosion resistance and high temperature performance. Disadvantages include high cost, extensive post-processing requirements and slower printing due to high energy requirements.
- Aluminum — Aluminum offers light weight, a fairly high strength-to-weight ratio, high thermal and electrical conductivity, and attractive costs, especially for non-critical parts. Disadvantages include lower fatigue resistance and higher potential for porosity issues. Aluminum alloys used in AM include AlSi10Mg, known for its high corrosion resistance, and Scalmalloy, which includes scandium for higher strength.
- Nickel-based alloys — Often referred to as Inconel, a registered trademark of Special Metals Corp., these superalloys offer high strength under extreme temperatures and maintain chemical and mechanical properties under high stresses. Disadvantages include high cost and longer printing times. A variety of Inconel alloys have been developed, with Inconel 625 and Inconel 718 most common in aerospace applications.
- Stainless steel — Numerous stainless steel alloys have been developed. In general, they offer high strength, excellent corrosion resistance and cost-effectiveness for a wide range of parts. Disadvantages include high weight and strength loss at high temperatures. The 304 alloy is composed of iron, carbon, chromium and nickel. The 316L alloy contains molybdenum, providing additional corrosion resistance and malleability. The 17-4 PH alloy is precipitation-hardened and known for its hardness, corrosion resistance, high tensile strength and high yield strength.
- Cobalt chrome alloys offer high wear resistance, strength and durability. Disadvantages include high cost, brittleness and difficulty to process.
- Other metallic materials used in 3D printing include copper, niobium, zirconium, tantalum, tungsten, and Hastelloy.
What standards apply to 3D printing of metallic materials?
A variety of standards and guidelines have been published for 3D printing. Organizations such as ASTM International, the International Organization for Standardization (ISO), the Consortium for Materials Data and Standardization, the American Institute of Aeronautics and Astronautics, and VDI – The Association of German Engineers provide various documents that can be helpful. Some examples include:
- ASTM F3572 – Standard Practice for Additive Manufacturing – General Principles – Part Classifications for Additive Manufactured Parts Used in Aviation
- ISO/ASTM52941 – Additive Manufacturing — System Performance and Reliability — Acceptance Tests for Laser Metal Powder-bed Fusion Machines for Metallic Materials for Aerospace Application
- ISO/ASTM 52967:2024 — Part Classifications for Additive Manufactured Parts Used in Aviation
The volume of information might seem overwhelming at first. In some cases, values for certain properties might vary based on different conditions, so multiple sources may need to be consulted.
“You might get a wide range of values for properties such as tensile strength,” noted Christian Seidel, a strategic implementation consultant at ASTM-affiliated Wohlers Associates and a professor of manufacturing technologies and additive manufacturing at Munich University. Consequently, industry professionals often conduct “round-robin tests to compile values focused on performance or specific mechanical properties,” he said.
Printer manufacturers and service providers can provide additional information on specific materials and testing. Material data sheets provided by manufacturers have improved in quality in recent years, according to Seidel.
Read the rest of this story at ENGINEERING.com