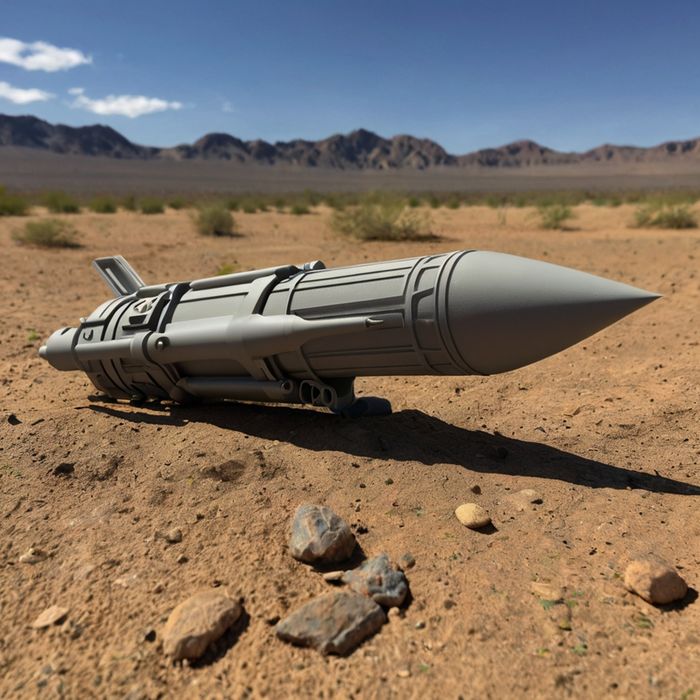
Charles R. Goulding and Preeti Sulibhavi discuss how the Ukraine war is transforming the EU defense industry, driving a surge in 3D printing adoption for rapid prototyping and on-demand production.
The ongoing war in Ukraine has triggered a profound transformation within the European Union’s defense industry, catalyzing a surge in military spending and driving innovation across various sectors. One area that has gained significant traction is the adoption of 3D printing technology, which is revolutionizing the manufacturing processes and supply chains of defense contractors.
The conflict in Ukraine has exposed the vulnerability of traditional supply chains, with the depletion of critical munitions and equipment stockpiles. This shortage has prompted defense companies to explore alternative manufacturing methods that can deliver rapid prototyping, mass customization, and on-demand production capabilities. 3D printing has emerged as a game-changer, enabling the production of intricate components, spare parts, and even entire systems with unprecedented speed and efficiency.
The integration of 3D printing in the defense industry is not entirely new, but the urgency created by the war in Ukraine has accelerated its adoption. Major defense contractors, such as BAE Systems, have been at the forefront of this technological revolution, leveraging 3D printing to produce missile components, propellant tanks, and other critical parts.
One prime example is BAE Systems’ joint venture with Nano Dimension, an Israeli additive manufacturing company. This partnership aims to explore the potential of 3D printing in the production of specialized electronics and components for the defense sector. By employing Nano Dimension’s proprietary technology, BAE Systems can manufacture high-performance electronics, including radio frequency (RF) and electromagnetic wave components, directly onto circuit boards. This capability streamlines the production process, reduces lead times, and enhances the overall efficiency of the supply chain.
The benefits of 3D printing extend beyond the production of individual components. Defense contractors are exploring the use of this technology to manufacture entire missile systems, including propellant tanks and other intricate structures. Rheinmetall, a German defense giant, has successfully utilized 3D printing to produce propellant tanks for its Intra Missile Launcher (IML) system. This innovative approach has not only reduced production times but has also enabled the creation of complex geometries that would be challenging or impossible to achieve through traditional manufacturing methods.
The integration of 3D printing into the defense industry is not limited to large corporations. Smaller companies and start-ups are also playing a vital role in driving innovation. For instance, Tekever, a Portuguese-British company specializing in unmanned aerial systems, has been utilizing 3D printing to rapidly prototype and manufacture components for its drones, which have been deployed in Ukraine.
The war in Ukraine has also highlighted the need for agile and iterative development cycles in the defense sector. Traditionally, defense procurement processes have been lengthy and bureaucratic, often taking years to introduce new technologies. However, the rapid pace of technological advancements, particularly in areas like 3D printing, has necessitated a nimbler approach. Defense contractors are now working closely with smaller, technology-led companies to leverage their expertise and accelerate the deployment of innovative solutions on the battlefield.
The Research & Development Tax Credit
The now permanent Research & Development Tax Credit (R&D) Tax Credit is available for companies developing new or improved products, processes and/ or software.
3D printing can help boost a company’s R&D Tax Credits. Wages for technical employees creating, testing and revising 3D printed prototypes can be included as a percentage of eligible time spent for the R&D Tax Credit. Similarly, when used as a method of improving a process, time spent integrating 3D printing hardware and software counts as an eligible activity. Lastly, when used for modeling and preproduction, the costs of filaments consumed during the development process may also be recovered.
Whether it is used for creating and testing prototypes or for final production, 3D printing is a great indicator that R&D Credit eligible activities are taking place. Companies implementing this technology at any point should consider taking advantage of R&D Tax Credits
Conclusion
As the war in Ukraine continues to unfold, the defense industry’s reliance on 3D printing is expected to grow further. This technology not only offers a solution to address immediate supply chain challenges but also opens up new avenues for design and manufacturing innovation. By embracing 3D printing, defense contractors can optimize production processes, enhance operational readiness, and ultimately strengthen the overall defense capabilities of the European Union and its allies.