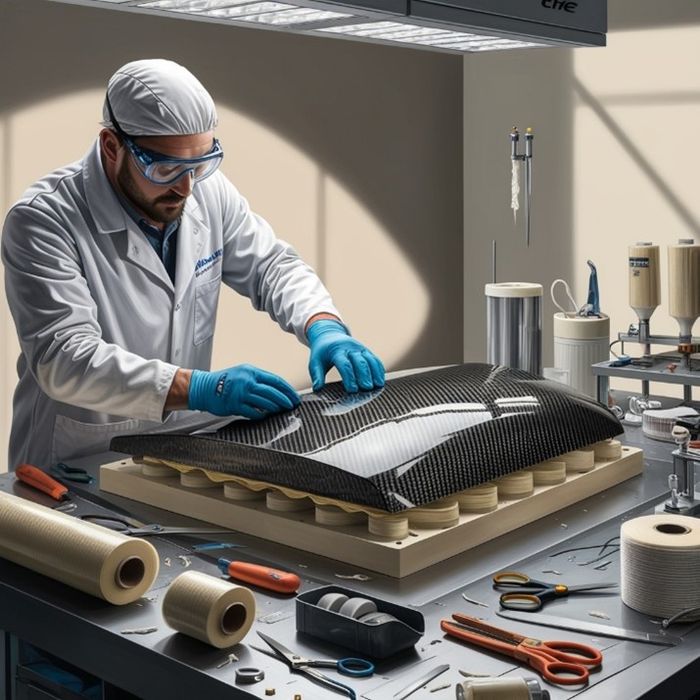
Charles R. Goulding and Preeti Sulibhavi examine how cutting-edge 3D printing with composites enables precise, durable solutions that meet the highest industry standards.
The use of 3D printing for commercial projects can often be challenging, especially if fabrication is intended for the aerospace or automotive industries. This is where composite materials become advantageous.
Composite materials are engineered combinations of two or more constituent substances that work together to create a material with unique advantages such as corrosion resistance, nonconductivity, and weight reduction. These composites are intentionally designed to meet specific performance requirements that the individual components alone could not achieve. Generally, composites consist of a matrix material (like epoxy resins, plastic or metal) and a reinforcing material (such as carbonfibers, fiberglass or nanoparticles). The matrix binds the reinforcement, distributing stress and protecting it from environmental damage, while the reinforcement provides strength and rigidity.
Composite Materials and Polymers
Both polymers and composite materials play integral roles in modern manufacturing, but they differ fundamentally. Polymers, are long chains of molecules known for their flexibility and plasticity, and are often used independently or as the matrix in a composite material. Composite materials, by contrast, are structured to exploit the best properties of their components, like high strength, lightweight, or corrosion resistance.
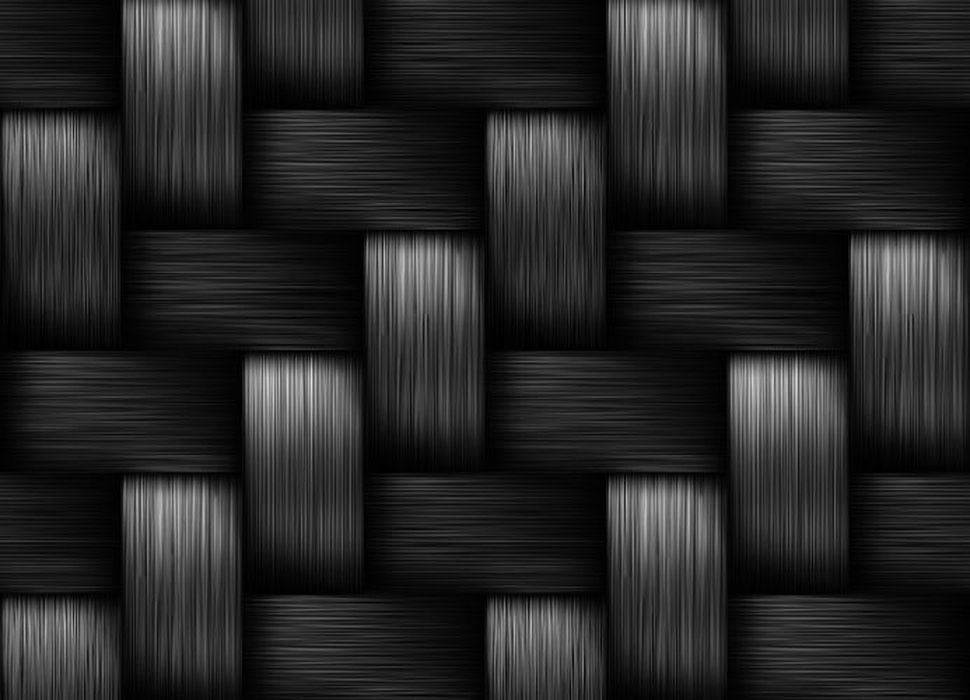
Polymer Composites vs. Traditional Composites
- Polymer Composites: Polymers serve as the matrix in which reinforcement materials, such as glass fibers or particles, are embedded. This composite type is known for its low-density, high specific strength properties, and is commonly used in automotive, marine and aerospace applications.
- Traditional Composites: Traditional composites might use natural fibers (like wood or bamboo) or other non-polymer matrices, relying on more rigid structures and conventional assembly techniques.
Key Differences and Similarities
- Both materials are integral to lightweight, durable applications.
- Composites usually involve fiber reinforcement, whereas polymers may stand alone in product manufacturing.
- Polymer composites are ideal for 3D printing and complex designs, whereas traditional composites may lack the necessary flexibility.
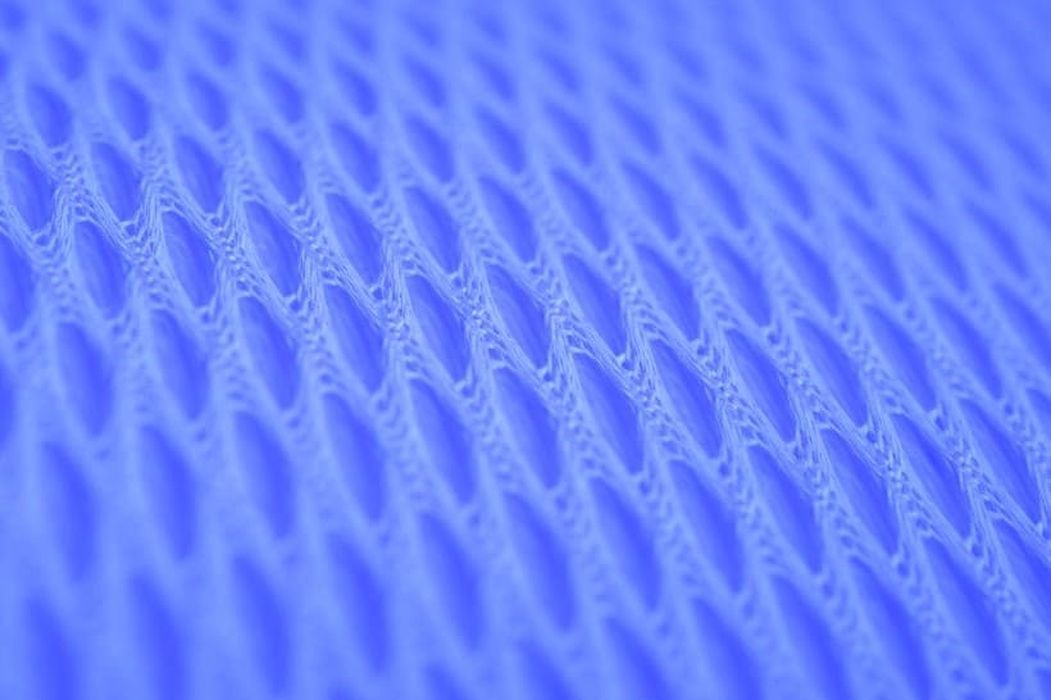
Characteristics of Composites: Strength, Lightweight, and Tensile Properties
One of the most compelling attributes of composite materials is their ability to maintain strength while reducing weight. The fibers within composites, such as carbon or glass fibers, can bear substantial loads, adding tensile strength and stiffness to the material. This combination is essential for the automotive, marine and aerospace industries, where weight reduction without sacrificing strength improves fuel efficiency, payload capacities, and overall performance.
Benefits to Automotive and Aerospace Industries:
- High Strength-to-Weight Ratio: Allows for more efficient fuel consumption.
- Tensile Strength: Prevents material deformation under high stress.
- Resistance to Fatigue and Corrosion: Ensures longer lifespans in harsh environments.
Fiber Composites and Their Role in 3D Printing
Fibers in composite materials typically refer to elongated reinforcing structures embedded within the matrix. These fibers, whether natural or synthetic, provide the primary reinforcement, offering the composite its rigidity and strength. Carbon fibers and glass fibers are common due to their balance of strength, weight, and cost-effectiveness.
3D Printing and Fiber-Reinforced Composites
With the advancements in additive manufacturing (AM) or 3D printing, fiber-reinforced composites are becoming more accessible and customizable. 3D printing processes for polymer composites have specific advantages and challenges in fabricating fiber-reinforced composites for complex applications. A key point noted is that 3D printing enables intricate geometries and layered designs that are difficult, if not impossible, to achieve through traditional manufacturing.
3D Printing Techniques for Composites
Techniques such as fused filament fabrication (FFF) and powder bed fusion (PBF) allow for high-precision control over composite structures. This capability is particularly beneficial in aerospace applications requiring customization and resilience.
Emerging Materials for AM
The development of polymer-based composites tailored for 3D printing includes advanced thermosetting materials that cure at ambient temperatures and UV-curable photopolymers. This adaptability is essential for creating high-performance components.
One of our clients, GSE Dynamics, Inc., a composites manufacturer based out of New York, has been exploring additive manufacturing technology for their business.
Greg J. Mallon, Chief Strategy Officer for the company, has said:
“GSE Dynamics is evaluating large-scale 3D printing of fiber-reinforced polymers for the production of composite tooling and multi-axis machining of composite components. We believe that this near net shape additive manufacturing has the potential to improve quality while being substantially faster and dramatically less expensive.”
Challenges in Composite 3D Printing
However, as with most technologies, there are challenges. Issues such as low interlayer bonding and nozzle clogging in FFF are noted as obstacles, alongside the limited thermal and mechanical stability in 3D printed parts. Innovative solutions like using carbon nanotube-coated filaments for enhanced interlayer bonding is among the strategies used to address these issues.
The Research & Development Tax Credit
The now permanent Research and Development (R&D) Tax Credit is available for companies developing new or improved products, processes and/or software.
3D printing can help boost a company’s R&D Tax Credits. Wages for technical employees creating, testing and revising 3D printed prototypes are typically eligible expenses toward the R&D Tax Credit. Similarly, when used as a method of improving a process, time spent integrating 3D printing hardware and software can also be an eligible R&D credit expense. Lastly, when used for modeling and preproduction, the costs of filaments consumed during the development process may also be recovered.
Whether it is used for creating and testing prototypes or for final production, 3D printing is a great indicator that R&D Credit-eligible activities are taking place. Companies implementing this technology at any point should consider taking advantage of R&D Tax Credits.
Conclusion
Composite materials are revolutionizing manufacturing, especially with advancements in 3D printing. Their strength, lightweight properties, and customizable compositions make them ideal for demanding applications in industries like aerospace, marine and automotive. As 3D printing technology continues to evolve, the integration of fiber-reinforced composites will likely expand, bringing about innovations that push the boundaries of what modern engineering can achieve.