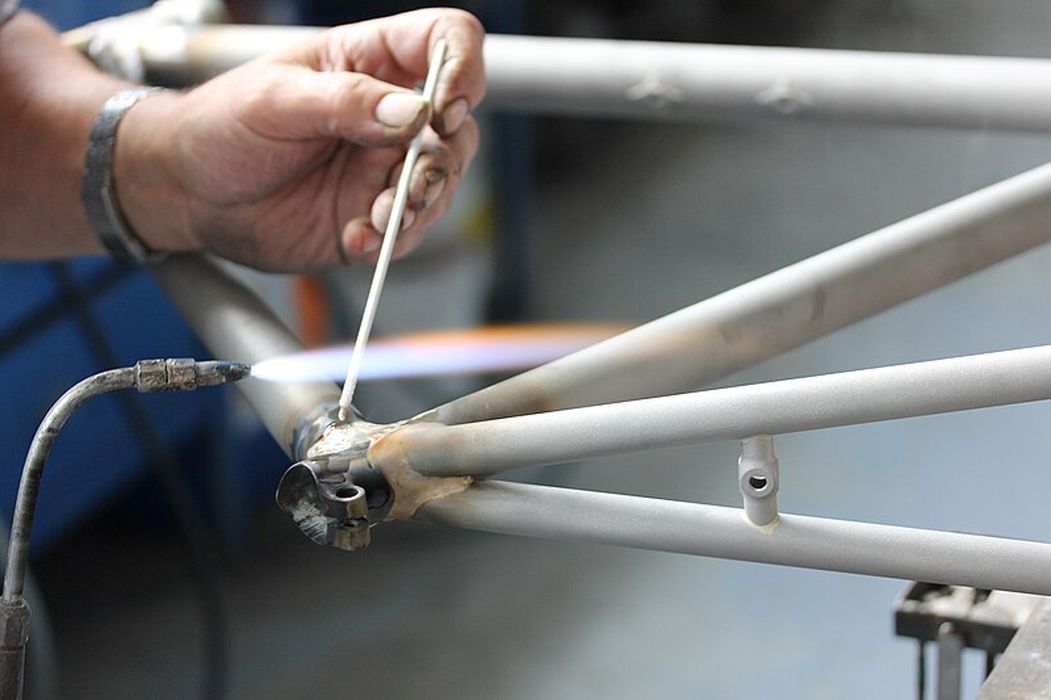
Peter Saenz investigates the transformative forces of tariffs, advanced manufacturing, and supply chain transparency, revealing how they could drive a new era of U.S. bicycle production.
In 2018, the Trump administration introduced tariffs on many products manufactured in China—including bicycle components—with the stated goal of encouraging American companies to localize production by raising the cost of imports. In practice, however, these tariffs mainly hit China’s export-dependent industries and incentivized workarounds. Chinese manufacturers began circumventing the tariffs by rerouting goods through third countries, performing final assembly steps offshore, or shifting portions of production to nations such as Malasyia, Thailand, Vietnam, and Cambodia.
Now, under a “second administration” again proposing Chinese and global tariff increases and in an era of rapidly advancing supply chain transparency, these evasive maneuvers may soon face serious challenges. Improved digital tracking systems at ports are making it easier to verify the true origin of goods—a change that could dampen the longstanding practice of tariff circumvention. As a result, American manufacturers are increasingly assessing the viability of reshoring production, but this shift comes with the challenge of rethinking both manufacturing technology and product design.
Rethinking the Manufacturing Paradigm
For decades, China’s bicycle industry has benefited from enormous sunk costs in specialized factories, tooling, and workforce skills. Even now, over 90% of bicycle components used by many U.S. brands originate from China. Shifting production domestically isn’t simply a matter of retooling—it demands a fundamental change in the production model. Commentators like Peter Zeihan argue that rising labor costs in China combined with stagnating productivity make domestic manufacturing in the Western Hemisphere increasingly cost competitive when logistics and other hidden costs are taken into account. In fact, when you factor in robust innovation ecosystems, local supply chain security, and shorter lead times, there’s significant incentive to move production closer to market—even if the traditional Chinese model still benefits from deep, decades-long investments in industrial infrastructure.
This is where the agile, “Zara-like” manufacturing model enters the conversation. Just as Zara Management successfully capitalized on fast fashion by producing in proximity to its key markets,U.S. bicycle manufacturers could adopt a similar strategy. Shorter production cycles would allow companies to rapidly capitalize on design trends and market demands. However, to harness these benefits, the overall design and manufacturing approach must change.
The Promise and Challenge of Additive Manufacturing
Advancements in 3D printing are poised to play a transformative role—provided that the design of components is rethought entirely. Traditional bicycle components have been designed with conventional manufacturing techniques (stamping, forging, machining) in mind. To make 3D printing economically competitive with mass manufacturing, companies must rethink functionality. For example, shifting from chain-and-sprocket drive trains—which are difficult to replicate with the performance and smoothness offered by conventional machining—to belt drives, string-based systems, or drive shaft designs could open the door for 3D printed components. Supplementary metal components can be integrated into these designs for durability. Recent research suggests that incorporating high-performance alternative fill materials that mimic the properties of metal could enhance the durability of printed parts, although further technological improvements are needed.
Design for 3D printing is not simply about printing existing designs—it requires a complete rethinking of components. Optimizing parts for weight, performance, and cost may mean that consumers, engineers, and manufacturers must break cultural inertia and redefine what a bike should look like and how it should function. A more agile design process would allow manufacturers to rapidly prototype and refine components, enabling highly customizable designs that are produced in smaller, more localized batches—a scenario much like the fast-turnaround, trend-sensitive approach seen with Zara’s fashion model.
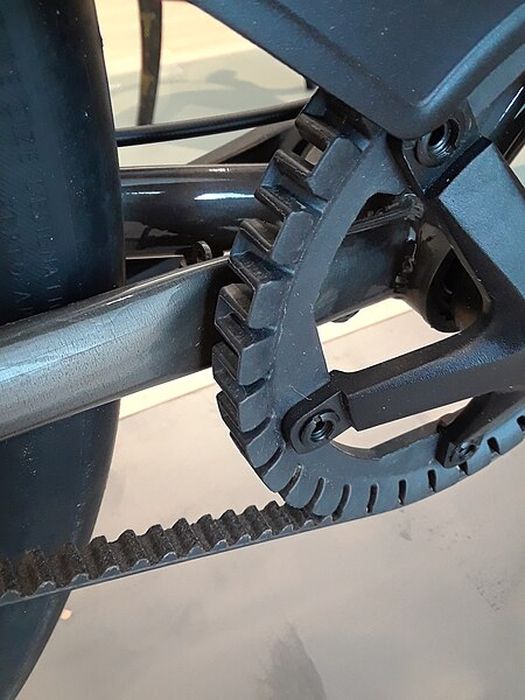
The Economic Equation and Policy Shifts
Tariffs continue to shift the economic balance in favor of domestic production, especially for mid-tier and premium bicycles. Although the policy was partly intended to encourage onshore production (even if it primarily hurt Chinese manufacturers), the deep-seated dependence on Chinese supply chains remains a significant challenge. For example, after the 2018 tariffs, American brands like Guardian Bikes have continued to grapple with an overwhelming reliance on Chinese components—even as they’ve begun to localize assembly and eventually production of certain parts.
Some industry leaders anticipate that the overall economic landscape will evolve as new tariffs and existing tax incentives for domestic manufacturing (such as proposed lower corporate tax rates for reshored production and R&D tax credits) increase the competitiveness of U.S. companies. While Zeihan notes that despite the current challenges—such as the sunk costs of Chinese manufacturing and legacy industrial infrastructure—the long-term trend of rising wages in China and the overall advantages of onshoring are tipping the scale in favor of American manufacturing. Advancements in digital tracking further support this shift by enhancing transparency in supply chains.
Looking Ahead: Transforming the Bicycle Industry
For now, 3D printing and other emerging manufacturing processes remain a fraction of the global bicycle market. However, if U.S. companies can successfully integrate design for additive manufacturing into an agile, domestic production strategy, there’s potential for a significant transformation in the industry. Not only would this approach allow companies to rapidly respond to market trends—a strategy akin to the Zara model—but it might also redefine the aesthetic and functional benchmarks for bicycles in the U.S. and the Western Hemisphere.
Ultimately, transitioning to a more localized, responsive manufacturing ecosystem will require coordinated efforts between policymakers, industry leaders, and technology innovators. As supply chain technologies improve and as the economic rationale for domestic production strengthens, the bicycle industry may see an entirely new generation of products that blend the customization and rapid design turnaround of 3D printing with the enduring durability demanded by cyclists.
Note: Peter Saenz is an analyst with R&D Tax Savers and has over a decade of experience in the bicycle industry, specifically in the retail sector.