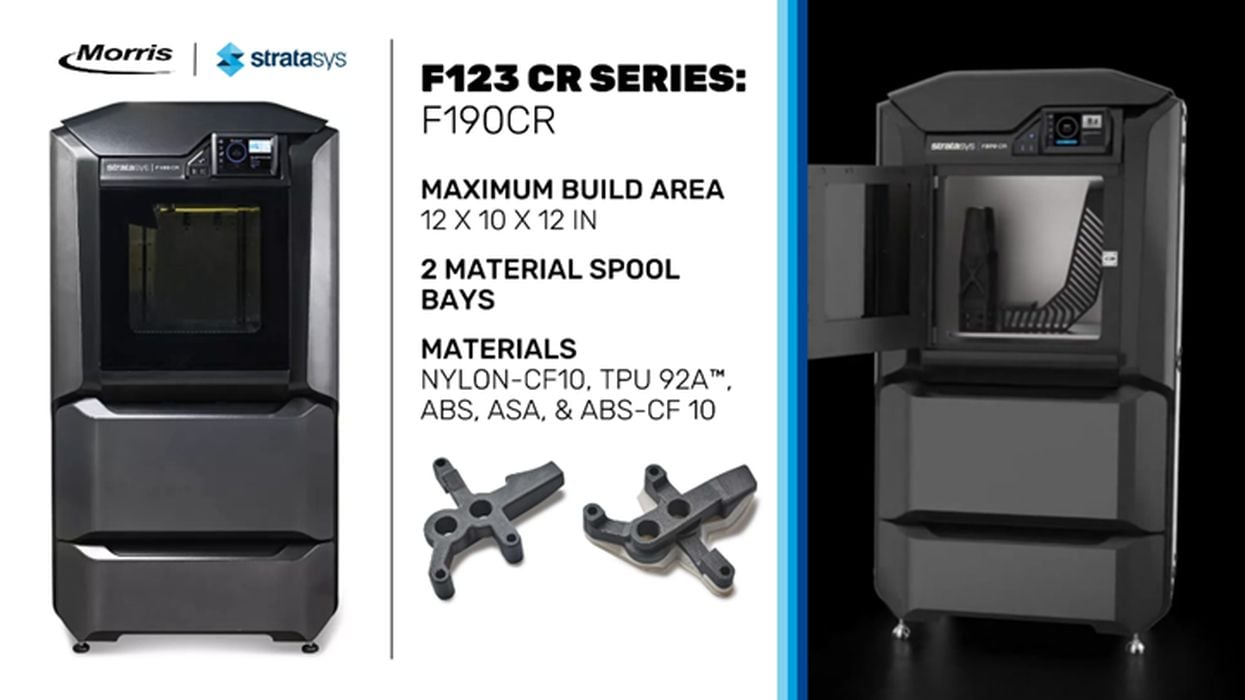
Charles R. Goulding and Preeti Sulibhavi discuss Robert E. Morris’ groundbreaking agreement with Stratasys to integrate additive manufacturing solutions into machine shops and manufacturing facilities.
In a move that promises to shake up the North American manufacturing landscape, Robert E. Morris Co (Morris), the largest seller of machine tools in the United States, has entered into a groundbreaking agreement with Stratasys Ltd., a global leader in 3D printing technology.
Robert E. Morris Co
With over 500 employees and a dominating presence at the International Machine Tool Trade Show (IMTS) in Chicago, Robert E. Morris Co is a behemoth in the world of machine tools. Founded in 1941, over eighty years ago, the company has built a reputation as a trusted purveyor of high-quality metalworking equipment, serving some of the most prestigious names in the manufacturing industry.
Morris’s success can be attributed to its unwavering commitment to customer service, technical expertise, and a vast inventory of cutting-edge machinery from renowned brands. The company’s deep understanding of the needs of modern machine shops and manufacturers has positioned it as a go-to resource for businesses seeking to optimize their operations and stay ahead of the curve.
Morris’s vast inventory includes the latest vertical and horizontal lathes, machining centers, milling machines, and Swiss machines, as well as manual and multi-tasking machines. They also specialize in cutting-edge additive manufacturing and automation solutions that can take productivity to new heights. From double columns to collaborative robots (cobots), they offer the latest in machine tool technology from leading builders. Their wide range of CNC machines can elevate a company’s manufacturing process.
5-axis CNC machines, including those from leading manufacturers like Okuma, Modig, and Soraluce, can revolutionize production processes across industries like aerospace, energy, and automotive by reducing part handling and increasing speed and accuracy.
Manufacturing companies are turning to automation to address their expansion and workforce difficulties. They desire user-friendly and accessible automation solutions that can optimize their processes. By implementing automated systems like robotic process automation and utilizing technologies such as Okuma’s ROID series, AWR’s Load & Go, and collaborative robots from UR Robots, manufacturers can enhance efficiency and profitability, paving the way for a promising future in the industry.
And, Morris is spearheading the automation shift in manufacturing by supplying advanced 3D printing and manufacturing systems from Desktop Metal, One Click Metal, and Stratasys. 3D printing offers significant benefits, such as quick prototyping, minimizing material waste, and facilitating intricate and personalized designs. Furthermore, the Okuma MU-8000V LASER EX, equipped with both subtractive and additive features, is transforming the manufacturing landscape.
Stratasys
Stratasys Ltd. is a pioneering force in the realm of 3D printing technology. With a global workforce of over 2,000 employees and reported revenue of US$521 million in 2022, the company has established itself as a leader in the additive manufacturing arena.
Stratasys’ portfolio encompasses a diverse range of 3D printing solutions, from industrial-grade FDM (Fused Deposition Modeling) systems to cutting-edge PolyJet and stereolithography technologies. These advanced systems are capable of producing complex, high-quality parts and prototypes from a wide variety of materials, including thermoplastics, photopolymers, and composites.
Unparalleled Entry into North America’s Manufacturing Landscape
The partnership between Morris and Stratasys represents a strategic move that will provide Stratasys with unparalleled access to North America’s leading machine shops and manufacturers. Morris’ extensive sales force and longstanding relationships with top-tier clients will serve as a powerful conduit for Stratasys’ innovative 3D printing solutions.
By leveraging Morris’ deep industry knowledge and customer base, Stratasys will gain a significant foothold in a market that is rapidly embracing additive manufacturing as a complementary technology to traditional subtractive processes like CNC machining.
Michael DiMarino, President of Linda Tool, a leading NYC machine shop company that started seventy years ago, is a long-time customer of Morris.
According to DiMarino:
“Their new partnership with Stratasys gives our industry the benefits of Morris reliability coupled with the best of breed 3D printing capability of Stratasys. The new generation of machine shop owners are interested in integrating 3D printers into production tool kits and this joining of the two leading resources will accelerate that process. We are a long-time Morris customer due to their attention to detail and deep knowledge and application of their products. They always recommend the right product for the right job.“
Bridging the Gap Between CNC Machining and 3D Printing
The integration of 3D printing into machine shops and manufacturing facilities offers numerous benefits, including faster prototyping, greater design freedom, and the ability to produce complex geometries that would be challenging or impossible to achieve through conventional machining methods.
Stratasys’ recent advancements in 3D printing technology have yielded impressive results, further highlighting the potential of this technology in the manufacturing sector. For instance, the company’s J826 PolyJet 3D printer is capable of producing parts with unprecedented levels of detail, texture, and material properties, making it an ideal solution for prototyping and low-volume production runs.
Moreover, Stratasys’ F900 Production 3D Printer, built on the company’s FDM technology, enables the production of large, complex parts with exceptional strength and accuracy. This system is particularly well-suited for applications in the automotive, aerospace, and industrial equipment sectors, where high-performance materials and precision are paramount.
By incorporating these advanced 3D printing solutions into their workflows, machine shops and manufacturers can streamline their operations, reduce lead times, and explore new design possibilities that were previously unattainable or prohibitively expensive.
The Research & Development Tax Credit
The now permanent Research and Development (R&D) Tax Credit is available for companies developing new or improved products, processes and/or software.
3D printing can help boost a company’s R&D Tax Credits. Wages for technical employees creating, testing and revising 3D printed prototypes can be included as a percentage of eligible time spent for the R&D Tax Credit. Similarly, when used as a method of improving a process, time spent integrating 3D printing hardware and software counts as an eligible activity. Lastly, when used for modeling and preproduction, the costs of filaments consumed during the development process may also be recovered.
Whether it is used for creating and testing prototypes or for final production, 3D printing is a great indicator that R&D Credit eligible activities are taking place. Companies implementing this technology at any point should consider taking advantage of R&D Tax Credits.
Conclusion
As the manufacturing industry continues to evolve, the collaboration between Robert E. Morris Co and Stratasys represents a significant step forward in the adoption of additive manufacturing technologies. With Morris’ extensive reach and Stratasys’ cutting-edge solutions, this partnership is poised to reshape the way businesses approach product development, prototyping, and production, ushering in a new era of innovation and efficiency in the North American manufacturing landscape.