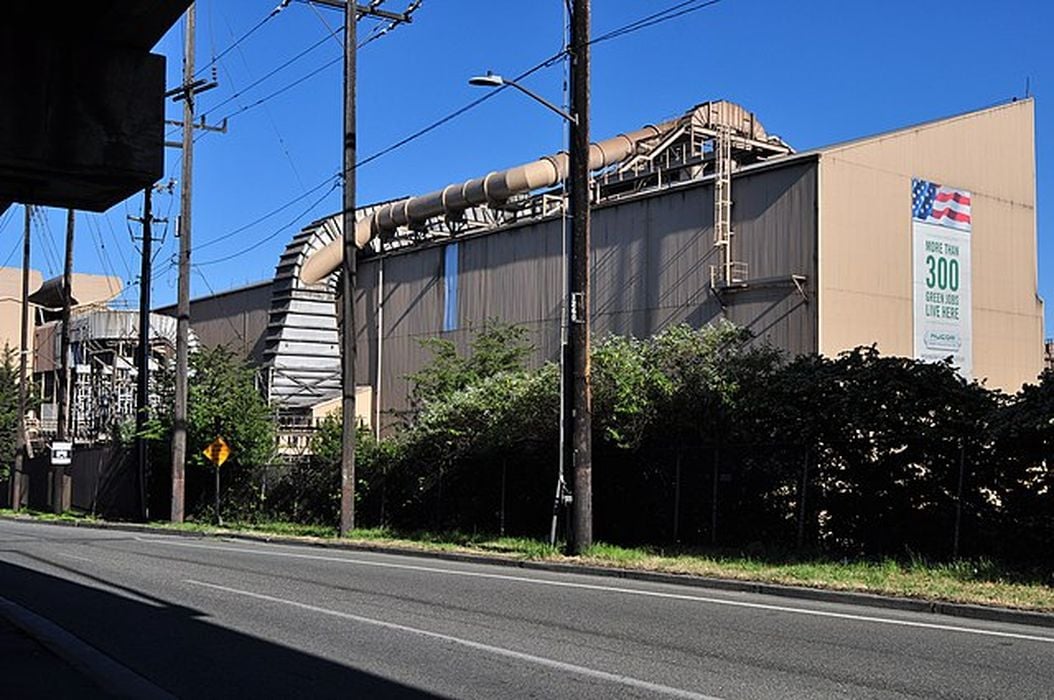
Charles R. Goulding and Kellen Coleman drill into how the ongoing U.S. Steel acquisition battle could redefine material availability, costs, and innovation in the fast-growing 3D printing industry.
The ongoing battle over the acquisition of United States Steel Corp. has significant implications beyond traditional steel manufacturing, reaching into the rapidly growing 3D printing industry. As Cleveland-Cliffs and Nucor contemplate a fresh bid for U.S. Steel, the outcome could shape material availability, pricing, and innovation in metal additive manufacturing (AM).
The U.S. Steel Takeover Saga
After President Biden blocked Nippon Steel’s US$14.1 billion bid for U.S. Steel due to national security concerns, domestic companies Cleveland-Cliffs and Nucor are considering a new offer. The move is aimed at keeping U.S. Steel under American ownership, aligning with broader efforts to secure domestic supply chains. If successful, Cleveland-Cliffs plans to acquire U.S. Steel and sell the Big River Steel mill to Nucor, further consolidating the U.S. steel industry.
Nucor is America’s largest steel company and known for innovation and the utilization of a high percentage of recycled steel.
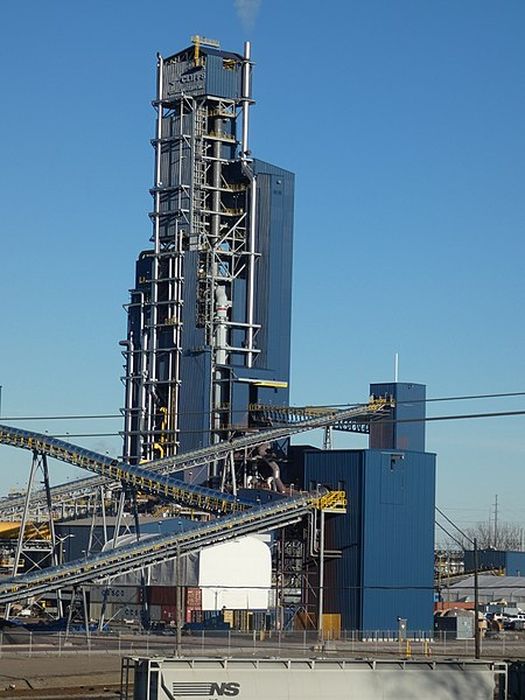
Why It Matters to 3D Printing
The metal 3D printing sector relies heavily on high-quality steel powders and alloys, which are derived from traditional steel manufacturing. U.S. Steel, a historic supplier of specialty steels, plays a crucial role in providing feedstock materials for metal AM processes, including:
- Powder Bed Fusion (PBF)
- Directed Energy Deposition (DED)
- Binder Jetting
With Cleveland-Cliffs and Nucor vying for control, their strategies toward steel production and R&D investments could directly affect the availability of advanced materials tailored for AM applications.
Potential Impacts on the 3D Printing Industry
- Material Availability and Cost
If Cleveland-Cliffs and Nucor prioritize traditional steel production over specialty alloys, 3D printing material suppliers could see disruptions. The consolidation of U.S. steel producers may also lead to pricing shifts, influencing costs for aerospace, automotive, and medical 3D printing applications. - Innovation in Additive Manufacturing Alloys
Companies like Nucor have shown interest in advanced manufacturing, and a successful bid may spur further investment in steel-based 3D printing materials. If these firms recognize the importance of additive manufacturing, they may expand R&D into high-performance alloys optimized for AM processes. - Supply Chain Security
Keeping U.S. Steel domestically owned aligns with broader national security efforts to ensure a reliable supply of critical materials. This could stabilize supply chains for U.S.-based 3D printing firms that depend on high-grade steel powders for defense and industrial applications.
While polymers dominate the consumer 3D printing market, metal 3D printing has seen rapid growth in industries such as aerospace, defense, and automotive manufacturing. Advanced techniques like Direct Metal Laser Sintering (DMLS) and Electron Beam Melting (EBM) rely on metal powders derived from high-quality steel and other alloys. With U.S. Steel at the center of a high-stakes acquisition battle, the outcome could impact the supply chain for these materials, affecting costs and innovation in additive manufacturing.
If Cleveland-Cliffs and Nucor successfully acquire U.S. Steel, the company’s future investments in material innovation will be crucial. For instance, Cleveland-Cliffs’ low-carbon steel project in Middletown, Ohio. Cleveland-Cliffs received funding from the U.S. Department of Energy’s Industrial Demonstrations Program (IDP) to install a hydrogen-ready Direct Reduced Iron (DRI) plant and electric melting furnaces. This project aims to reduce the carbon intensity of primary steel.
Nucor’s Oregon Manufacturing Innovation Center houses seven major types of metal 3D printers, which demonstrates that 3D printing innovation in this field will be thoroughly supported.
A focus on domestic steel production could drive the development of new high-strength alloys optimized for additive manufacturing, reinforcing the U.S.’s position as a leader in advanced manufacturing technologies. Conversely, if market consolidation leads to reduced competition and higher steel prices, metal 3D printing operations could see increased costs.
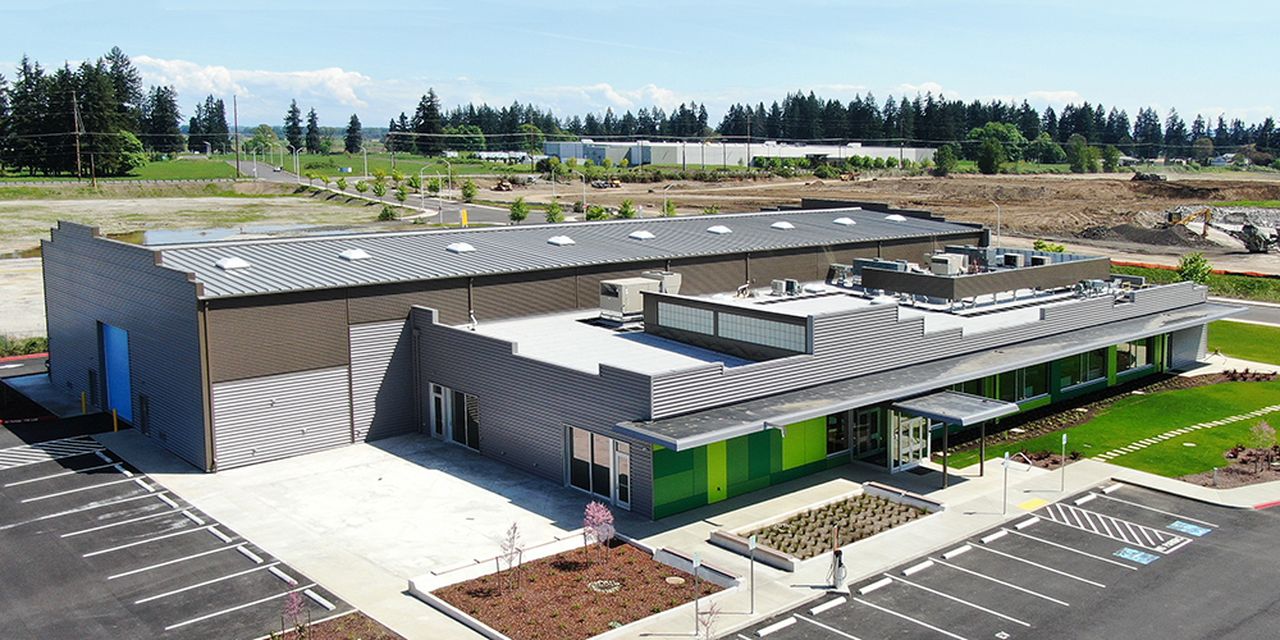
The Research & Development Tax Credit
The now permanent Research and Development (R&D) Tax Credit is available for companies developing new or improved products, processes, and/or software.
3D printing can help boost a company’s R&D Tax Credits. Wages for technical employees creating, testing, and revising 3D printed prototypes are typically eligible expenses toward the R&D Tax Credit. Similarly, when used as a method of improving a process, time spent integrating 3D printing hardware and software can also be an eligible R&D expense. Lastly, when used for modeling and preproduction, the costs of filaments consumed during the development process may also be recovered.
Whether it is used for creating and testing prototypes or for final production, 3D printing is a great indicator that R&D Credit-eligible activities are taking place. Companies implementing this technology at any point should consider taking advantage of R&D Tax Credits.
What’s Next for 3D Printing in a Changing Steel Industry?
As the future of U.S. Steel unfolds, companies in the additive manufacturing industry should pay close attention. A shift in steel production strategies, investments in new materials, and policy changes in domestic manufacturing could all shape the accessibility and affordability of metal 3D printing. At the same time, companies leveraging 3D printing for innovation should explore tax incentives like the R&D Tax Credit, ensuring they maximize the financial benefits of their research and development efforts.
The U.S. government’s intervention in the steel industry highlights a broader emphasis on domestic manufacturing and national security—factors that could further drive investment in 3D printing technologies. Whether through new material innovations or reshaped supply chains, the intersection of traditional steel production and additive manufacturing will be an important space to watch.