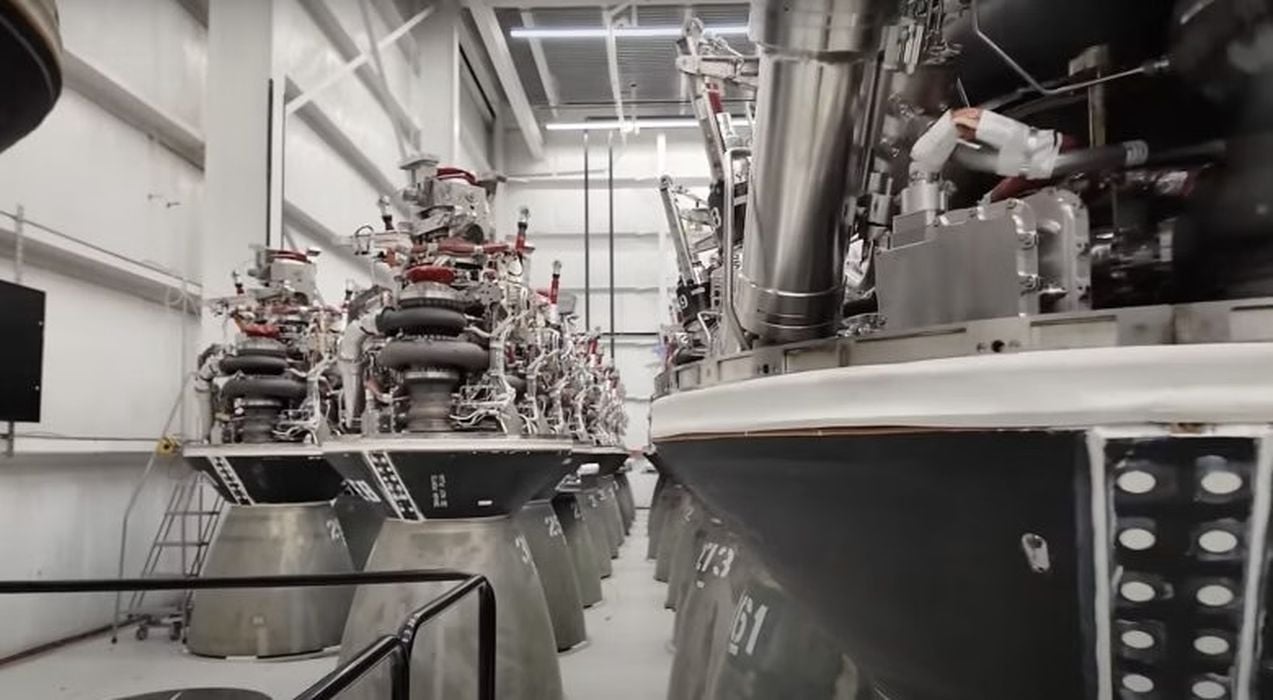
This level of rapid prototyping for complex functional systems would not be possible without additive manufacturing technology.
Starship’s fifth flight test, which took place perfectly on time on Sunday, October 13, around at 7 a.m. CT., was an incredible success. After just five test flights, SpaceX was able to develop the largest and most powerful spacecraft ever, launch the Starship spacecraft close to orbit, and catch its giant first stage as it landed using a sci-fi-inspired Mechazilla system and “chopsticks”. This would not have been possible without the ability to quickly and cost-effectively iterate prototypes using additive manufacturing. And SpaceX is a major user of AM technology for metal AM and 3D printed metal casting.
It’s too bad there are not enough SpaceXs out there to help drive AM adoption. Still, aerospace companies are among the biggest users of additive manufacturing – driving a large and rapidly growing global business. Pioneering space companies like VAST, Rocket Lab, Ursa Major, Relativity and Beehive are all heavy AM users, though certainly not at the same scale SpaceX is. There are also many large adopters in aviation and UAVs. That’s why Aerospace AM is the topic of VoxelMatter’s latest market report, which just went into pre-sale today, and delves into AM adoption by manufacturers in aviation, space and UAVs, for both defense and civil industries.
Back to SpaceX, Flight 4 was also a tremendous success. A fully successful ascent was followed by the first-ever booster soft-landing in the Gulf of Mexico and Starship making it through a brilliant reentry, before its own landing burn and splashdown in the Indian Ocean.
The fifth flight test of Starship took another step towards full and rapid reusability. The primary objective was the first-ever return to the launch site and catch of the Super Heavy booster and another Starship reentry and landing burn, aiming for an on-target splashdown of Starship in the Indian Ocean (you can try catching Starship it here).
Extensive upgrades ahead of this flight test have been made to hardware and software across Super Heavy, Starship, and the launch and catch tower infrastructure at Starbase. SpaceX engineers have spent years preparing and months testing for the booster catch attempt, with technicians pouring tens of thousands of hours into building the infrastructure to maximize our chances for success.
During a recent tour of the Starfactory, Musk told the Youtuber EveryDay Astronaut that several thousand changes are made to the vehicle’s hardware after each launch. Considering the last launch took place only a couple of months ago, this requires very high-speed manufacturing capabilities.
housands of distinct vehicle and pad criteria must be met prior to a return and catch attempt of the Super Heavy booster, which requires healthy systems on the booster and tower and a manual command from the mission’s Flight Director. If this command was not sent before the completion of the boost back burn, or if automated health checks show unacceptable conditions with Super Heavy or the tower, the booster would have defaulted to a trajectory that took it to a landing burn and soft splashdown in the Gulf of Mexico. The returning booster slowed down from supersonic speeds, resulting in audible sonic booms in the area around the landing zone.
Starship flew a similar trajectory as the previous flight test with splashdown targeted in the Indian Ocean. This flight path did not require a deorbit burn for reentry, maximizing public safety while still providing the opportunity to meet SpaceX’s primary objective of a controlled reentry and soft water landing of Starship. Even if it doesn’t crash, landing in the ocean means many of Starship’s parts – including its engines – must be sacrificed.
This also means that SpaceX must be able to produce multiple engines, rapidly and cost-effectively. While some of the simpler parts can be sourced from die-cast and CNC’d components, all the complex parts and subassemblies must be 3D printed. There is simply no way around it. Judging by the incredible number of boosters on the Starfactory floor, this means a lot of AM.
Read the rest of this story at VoxelMatters