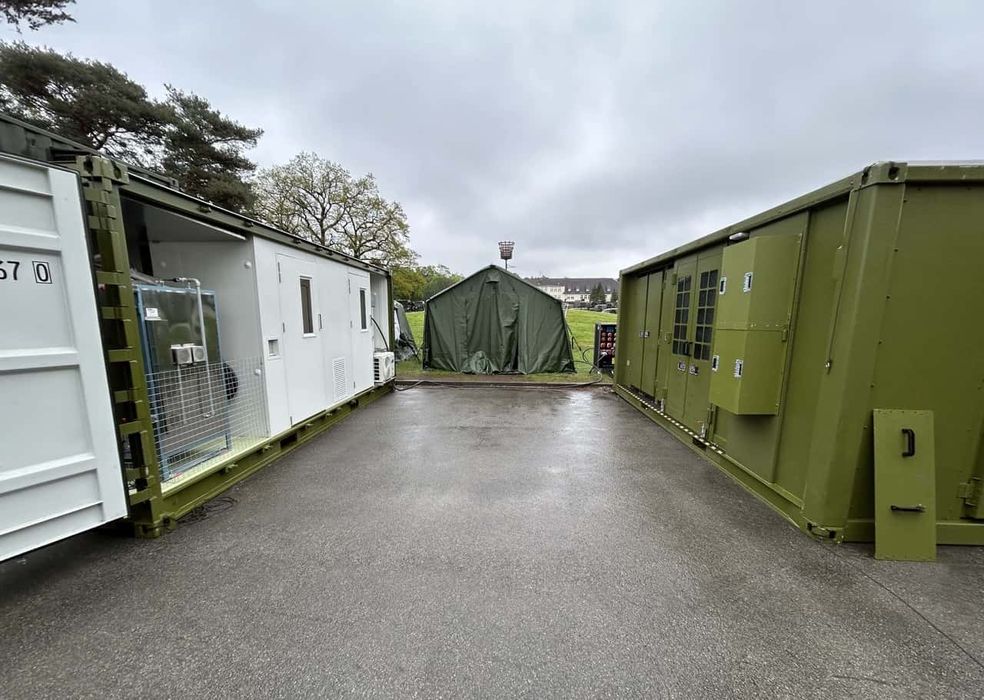
SPEE3D announced something they call the EMU, or “Expeditionary Manufacturing Unit”.
This isn’t a new 3D printer, but it is a radically interesting way to package up a 3D printing system.
Fabbaloo readers may recall that SPEE3D has focused much of their attention towards military applications. Military scenarios are quite compatible with SPEED3D’s technology, which is a supersonic cold-spray process that can rapidly produce metal 3D prints. Even better, their process can easily handle a wide variety of metals, including the difficult-to-print copper.
The nature of the supersonic process makes it more rugged than competing LPBF systems, which require complex and expensive factory setups to operate.
SPEE3D has taken this approach forward by introducing their “XSPEED” system, which packages their process into a single unit that’s inside a standard shipping container. This offering has proven popular among several Western military organizations, which hope to use the technology in the field.
However, we all know there’s more to the story than just the 3D printing part. Metal parts in particular must be post processed, sometimes in a very precise manner, in order for them to be useful.
That’s normally done with a set of post processing equipment that’s in the big factory beside the printers. Whoops, there’s no factory in the fields of the military.
SPEE3D’s latest offering, the EMU, attempts to overcome this challenge by packaging up EVERYTHING together. The EMU consists of the XSPEED and their SPEE3DCell post processing and testing systems.
The SPEE3DCell includes several critical pieces of equipment, including a heat treatment furnace, a CNC three-axis mill to smooth surfaces and cut off supports, tooling, and testing gear.
The result is a single configuration that can actually produce usable metal parts — in the field. SPEE3D describes it as:
“Design, print, cook, and cut.”
Indeed! The design part occurs with software that comes with the EMU, along with the operator’s usual 3D CAD tools and libraries.
There are some constraints, however. The 3D printer does have a maximum volume of 900mm diameter x 700mm tall, and there is a maximum part weight of 40kg. This is likely to ensure that the parts can make their way through the post processing equipment.
The EMU is definitely not a consumer product, and likely won’t be of interest to most industries. However, military applications clearly could make very interesting use of the EMU.
Via SPEE3D