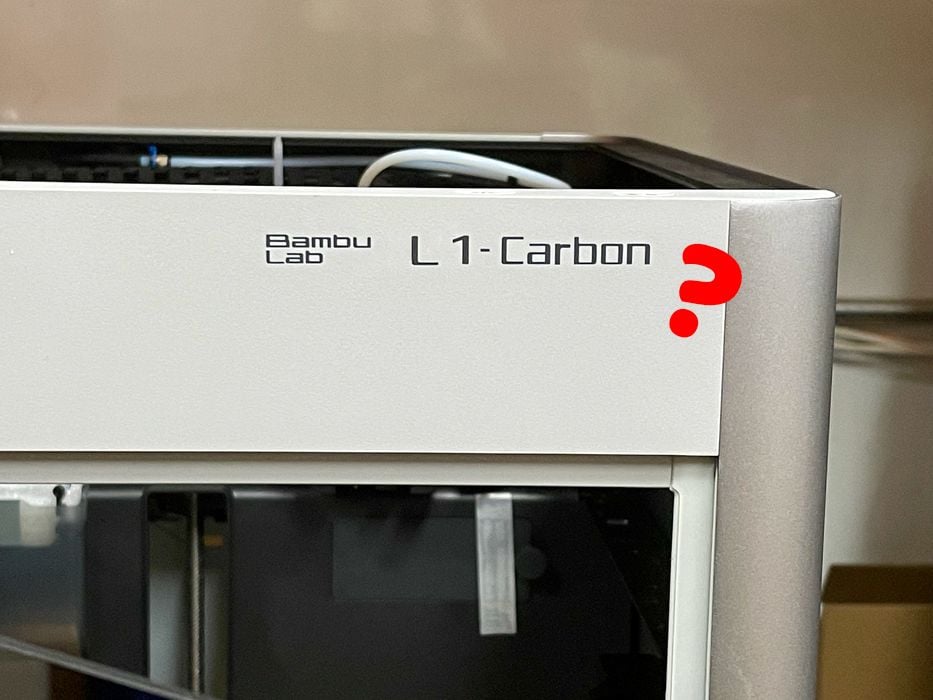
There have been many hints of Bambu Lab nearing an announcement of a new 3D printer, but what could it be?
After reading through the company’s recent Reddit AMA session, it seems that they are deep into development of a new device that is very likely to be announced this year.
Based on their cryptic responses in the AMA it seems that they will almost certainly produce a machine with a bigger build volume. That’s quite understandable because the one knock on their popular X and P series devices has been the somewhat limited build volume.
These machines today offer 256 x 256 x 256 mm, which is certainly adequate for many applications. But there are always some that are just a bit larger. By offering a larger build volume, Bambu Lab could capture another slice of the market.
There’s another reason for releasing a larger volume machine: competition. The main competition for the X and P series is most likely Prusa Research’s XL device, which just happens to have a much larger build volume of 360 x 360 x 360 mm. Anyone considering a Bambu Lab product but needs to print larger parts would certainly then look at the XL instead.
If Bambu Lab had a device with a similar build volume, they might not lose as many potential sales to Prusa Research’s XL. That’s why a larger build volume machine could be in the cards for Bambu Lab.
But there’s another factor at play: multimaterials. The entire Bambu Lab 3D printer lineup already offers optional material switching through their AMS or AMS Lite accessories. These work quite well, as we found in our reviews of the A1 and A1 Mini devices
These filament switchers work quite reliably, far more than the challenging Prusa MMU2S device that we tested a few years ago. Prusa Research has recently updated their design to the MMU3, which may or may not have been a reaction to the AMS capabilities.
However, the XL is quite different. Instead of switching filaments to use a single nozzle, the XL has separate toolheads for each material.
That overcomes a significant problem with both the AMS and MMU concepts: material wastage. Whenever a material is changed the single nozzle must be purged of the old material. This requires a brief extrusion of mixed colors until it “comes out clean”.
On Prusa MMU systems the purged material is printed in an adjacent “purge tower” or used as infill. On Bambu Lab systems the purge material is simply ejected as “poop”, which accumulates in a large pile beside the printer.
On these single nozzle multimaterial systems the amount of wasted material can be very significant, often exceeding the weight of the model itself. Many 3D printer operators are beginning to notice this effect, and some feel they are spending more on materials than they should simply because of the inefficiency of the single nozzle approach.
The XL is also far faster when printing multimaterial prints because it doesn’t have to wait for purges to occur. Instead the next color is already to go in another toolhead, and printing occurs almost immediately. The XL includes five toolheads for this purpose.
We do know from the AMA that Bambu Lab is considering a “new generation 3D printer”, as that was their answer regarding multicolor futures.
To me that suggests they may take an alternative approach to multiple materials on the new machine, one that could be much more efficient and less wasteful, and perhaps faster. That would be the formula to compete with the popular XL machine.
I see two approaches for Bambu Labs here. They could follow Prusa Research’s lead and simply develop a machine with a bunch of independent toolheads. That would certainly work, but all those toolheads can make the machine much more expensive.
The XL currently lists for US$1999, but that’s for the single toolhead version. The five-toolhead option raises the price to a whopping US$3,499. That’s more than 2X the price of the Bambu Lab X1C combo, showing how the multimaterial approach can affect costs.
My suspicion is that Bambu Lab may opt for a new switching method in the as-yet-unnamed new generation 3D printer.
One concept could be to have only two toolheads. The idea would be to switch out the filament on the not-used-right-now toolhead while the active toolhead does its work. That would certainly speed up printing quite a bit, but doesn’t do much for the material wastage issue: the nozzles must still be purged.
They could opt for the two-toolhead approach but combine it with additional purge tuning. It’s quite possible to do so, as there are plenty of suggestions for reducing the movement. Another approach I’ve seen is to do a big retraction before cutting the filament, which would significantly reduce the amount of purging required. It might also be possible to rework toolpaths to maximize use of purge material as infill.
As long as you are sharing nozzles, you must purge. Perhaps the key is to reduce the amount of purge required, and avoid the extra cost of more toolheads.
On the other hand, maybe Bambu Lab has something completely different in mind that offers both increased switching speed and reduced wastage. There are plenty of approaches that could be considered and I’m sure they’ve looked at many.
Either way, we will no doubt hear from Bambu Lab in coming months about their mysterious “next generation 3D printer”.