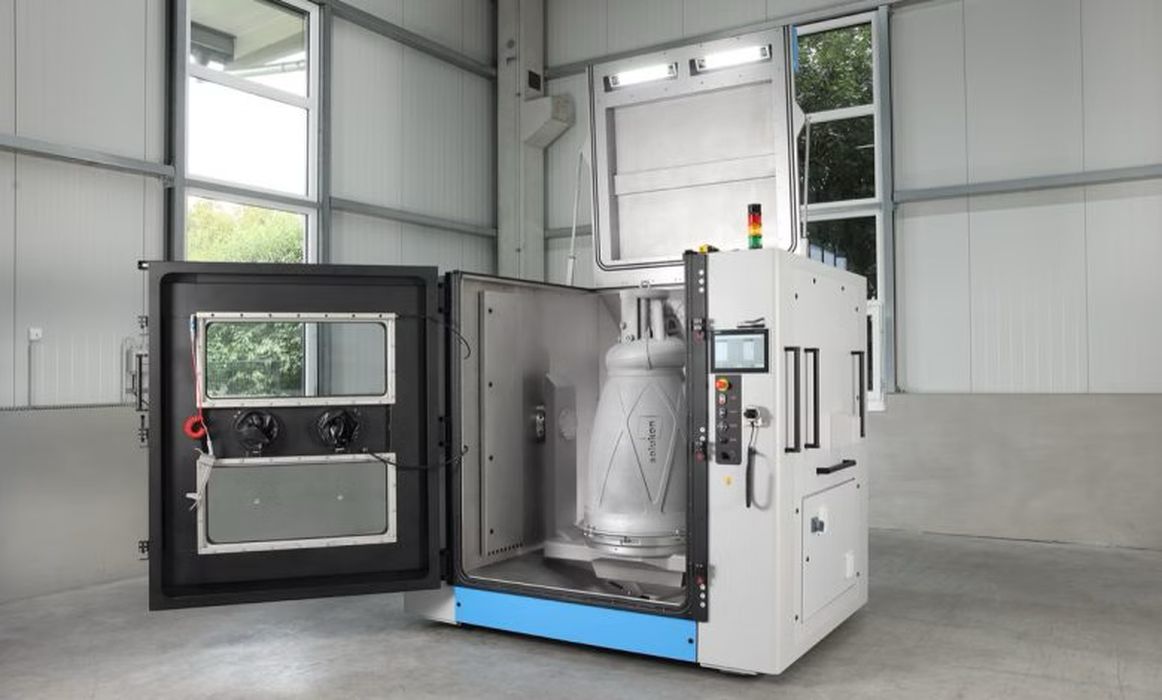
Two leading 3D printing companies have already ordered the new depowdering system.
Solukon started back in 2015 with a depowdering system designed for the largest machine on the market at the time, the Xline 2000R from Concept Laser (now Colibrium Additive), measuring 800 x 400 x 500 mm. As early as 2020, Solukon proved its depowdering expertise in the large-scale part segment again when it launched SFM-AT1000-S, a system that rapidly established itself as the market leader. The comprehensive experiences acquired since then have informed the development of an even larger system for metal parts. Solukon is now introducing the SFM-AT1500-S, a depowdering system that meets the growing demand for a depowdering solution in the heavy load segment at the highest level.
Two systems have already been sold, ahead of the official launch, to two of the leading print manufacturers with whom Solukon was in close consultation during the development of SFM-AT1500-S. These manufacturers were convinced by the system’s compact design.
Growing demand for heavy load depowdering
As metal additive manufacturing has matured, the need for larger and more complex parts has grown. Industries such as aerospace and automotive now routinely produce parts with massive dimensions that require efficient and thorough depowdering. The SFM-AT1500-S was developed in response to this growing demand, providing a solution capable of handling parts up to 2,100 kg and measuring up to 1,500 mm in length.
The SFM-AT1500-S stands out as Solukon’s largest depowdering system to date. Its capacity to depowder parts with dimensions of 600 x 600 x 1,500 mm or 820 x 820 x 1,300 mm, along with a weight capacity of 2,100 kg, makes it a perfect fit for industries where heavy-duty parts are a necessity. This system features several innovative technologies that set it apart from earlier models, including advanced vibration control and a compact design that minimizes its footprint while maximizing performance.
One of the key features of the SFM-AT1500-S is its compact design, which addresses the common challenge of limited production space. Despite its ability to handle extremely large parts, Solukon has engineered the system to be as space-efficient as possible. The machine’s narrow footprint and low-profile structure eliminate the need for platforms or stairs, streamlining the loading and handling process for operators.
Depowdering large and heavy metal parts requires a system capable of generating sufficient vibration to dislodge powder without damaging the component or the system itself. Solukon has solved this problem by developing a vibration decoupling technology, which ensures that the vibrations affect only the part being cleaned, while the rest of the system remains stable. This technology is critical for effectively depowdering parts of various sizes and materials.
The drive system in the SFM-AT1500-S is designed specifically to support parts weighing up to 2.1 tons. This ensures that even the largest and heaviest parts are moved smoothly and safely during the depowdering process. Solukon’s engineers have implemented a new generation of drive technology that is both reliable and durable, making it suitable for demanding industrial environments.
The depowdering chamber in the SFM-AT1500-S is constructed entirely from stainless steel, offering durability and resistance to wear over time. The machine also features a rotary table with four separately controlled compressed air lines, allowing operators to configure the system for a variety of different depowdering tools, including vibrators, knockers, and blowers. This versatility makes the SFM-AT1500-S an ideal choice for companies that work with a wide range of part sizes and geometries.
The SFM-AT1500-S is designed for industries where large metal parts are essential, such as aerospace, automotive, and energy. Its ability to handle heavy parts and complex geometries makes it an invaluable tool for manufacturers in these sectors. As additive manufacturing continues to evolve, the SFM-AT1500-S is positioned to meet the growing demand for efficient and reliable depowdering solutions.
Solukon’s unique capabilities
In today’s industrial landscape, digital tools are essential for achieving efficient and accurate results. The SFM-AT1500-S is compatible with Solukon’s SPR-Pathfinder software, which automatically calculates the ideal motion sequence for depowdering based on the part’s CAD file. This reduces human programming effort and ensures consistent, high-quality results. Additionally, the Digital-Factory-Tool provides real-time tracking of the entire depowdering process, giving users complete transparency and control.
Handling the large quantities of powder generated during the depowdering of massive parts is another challenge that Solukon addresses with the SFM-PCU powder collection unit. This system collects powder in large containers and is monitored by sensors to ensure safety and efficiency. The SFM-AT1500-S can also be integrated with powder conveying systems from other manufacturers, making it highly adaptable to different production environments.
Solukon’s success with the SFM-AT1000-S has been instrumental in establishing the company as a leader in the field of depowdering technology. With the SFM-AT1500-S, Solukon takes this leadership to the next level, offering an unparalleled solution for companies producing large-scale metal parts.