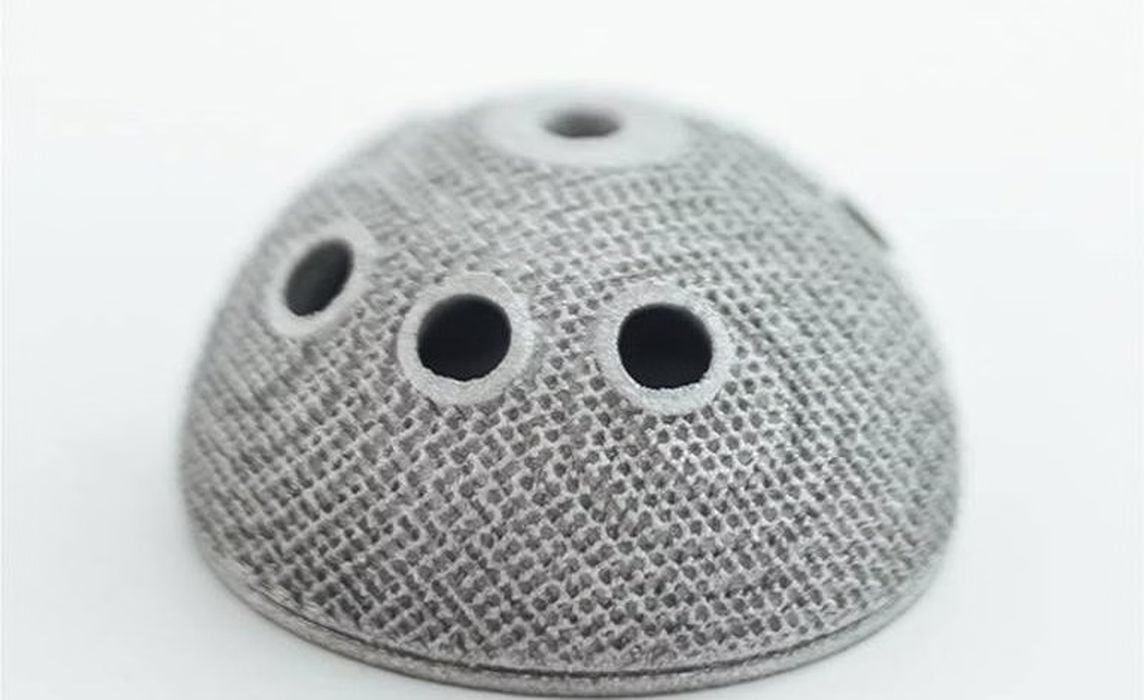
The work from UCL and the University of Greenwich reports an 80% reduction in pore formation in printed components while an appropriate magnetic field was applied.
According to University College London (UCL), a team of researchers from UCL and the University of Greenwich have developed a new 3D printing technique that substantially reduces imperfections in the manufacturing process. The technique was developed after the team used advanced X-ray imaging to observe the causes of imperfections that formed in complex 3D printed metal alloy components.
If this technique becomes widely deployed it could make a range of these components – from artificial hip joints to aircraft parts – stronger and more durable.
The study, published in Science, observes the forces at play during the laser-based 3D printing of metal alloys in unprecedented detail and in real-time. To do this, the team performed high-speed synchrotron X-ray imaging of the manufacturing process at the Advanced Photon Source (APS) synchrotron in Chicago, to record the complex interaction between the laser beam and the metal raw material over timescales of much less than a thousandth of a second.
This allowed them to see the creation of small keyhole-shaped pores in the component as a result of the vapor generated when the laser melted the metal alloys, and the cause of instabilities in the keyhole that leads to defects in 3D printed parts.
The team then observed the manufacturing process with a magnetic field applied to the metal alloys as the part is formed, which they hypothesized might help to stabilize the point at which the laser hits the molten metal – reducing imperfections. This theory proved correct, with an 80% reduction in pore formation in components printed while an appropriate magnetic field was applied.
“When the laser heats up the metal it becomes liquid, but also produces vapor. This vapor forms a plume that pushes the molten metal apart, forming a J-shaped depression. Surface tension causes ripples in the depression and the bottom of it breaks off, resulting in pores in the finished component,” said Dr. Xianqiang Fan, the first author of the study from UCL Mechanical Engineering. “When we apply a magnetic field to this process, thermoelectric forces cause a fluid flow that helps to stabilize the hole so that it resembles an ‘I’ shape, with no tail to break off when it ripples.”
In laser-based 3D printing of metal alloys, a computer-controlled laser melts layers of metal powder to form complex solid shapes. This enables the production of alloy components with unparalleled complexity for use in high-value products in a wide range of sectors – from titanium bicycle parts to biomedical prosthetics.
To obtain thick layers at fast speeds, the laser is highly focused to about the thickness of a human hair – creating a molten pool with a keyhole-shaped vapor depression near the front. However, this keyhole can be unstable and create bubbles that become pores in the final component – impacting mechanical durability.
“Though keyhole pores in these types of components have been known about for decades, strategies to prevent their formation have remained largely unknown. One thing that has been shown to occasionally help is applying a magnetic field, but the results have not been repeatable and the mechanism by which it works is disputed,” said Professor Peter Lee, senior author of the study from UCL Mechanical Engineering.
“In this study we’ve been able to watch the manufacturing process in unprecedented detail by capturing images over 100,000 times a second, both with and without magnets, to show that thermoelectric forces can be used to reduce keyhole porosity significantly. In real terms, this means that we have the knowledge we need to create higher-quality 3D printed components that will last much longer and expand use into new safety-critical applications, from aerospace to Formula 1.”
Before the insights from this study can be applied, manufacturers will need to overcome several technical challenges to incorporate magnetic fields into their production lines. The authors say this translation is likely to take several years, but that the impact of doing so will be significant.
Read the rest of this story at VoxelMatters