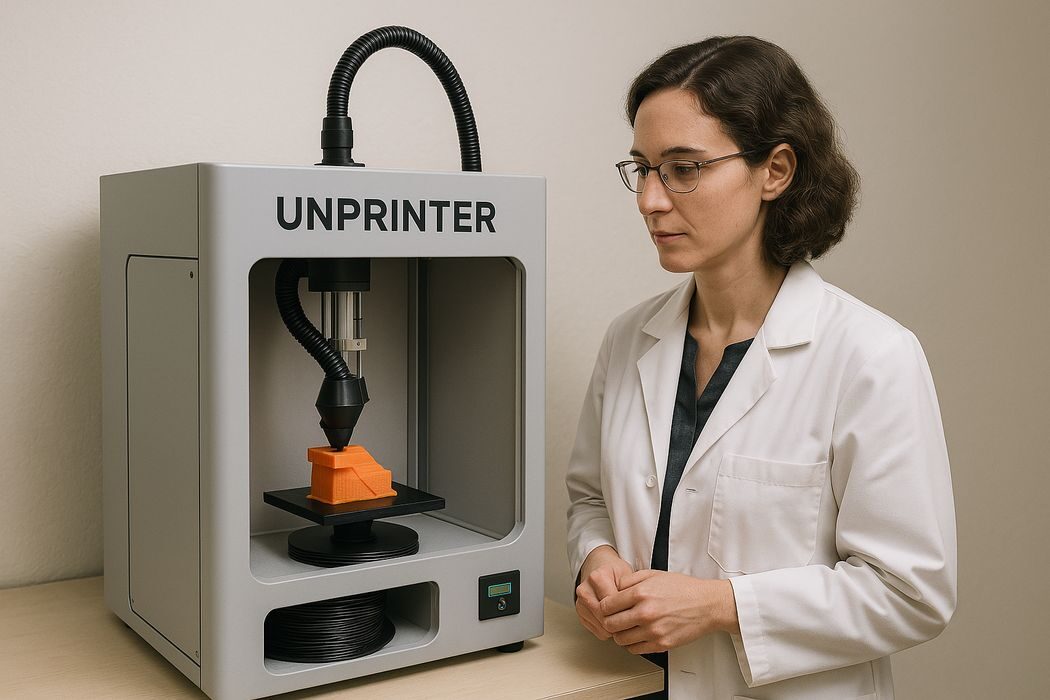
The 3D printing industry has made incredible strides over the past decade, but one nagging problem persists: what happens to the prints you don’t want?
Failed prototypes, outdated iterations, misprints, calibration artifacts — the pile grows steadily in every print lab and hobbyist’s garage. While there are commercial and DIY solutions for recycling filament, they’re often messy, inconsistent, and require significant manual effort.
Now, researchers at the Midwestern Institute of Circular Fabrication (MICFab) believe they’ve found a more elegant answer: a reverse 3D printer that can turn unwanted prints directly back into usable filament — all in one machine.
The device, dubbed the Unprinter, uses a novel active deconstruction system to analyze, soften, and reprocess printed parts. At the heart of the system is a new kind of toolhead the researchers call the MeltVac, which combines targeted heating with a synchronized vacuum-driven feed mechanism. As the MeltVac moves across the surface of a print, it gradually melts the plastic and simultaneously draws it into an internal chamber for filtering and extrusion.
“It works a bit like a 3D printer in reverse — tracing the surface of the object layer by layer, but instead of depositing plastic, we’re recovering it,” said Dr. Petra Lupin, lead researcher on the project. “It’s almost like un-printing, hence the name.”
Once collected, the material passes through a series of internal stages:
- Thermal homogenization, to reduce inconsistencies in melt temperature
- Particulate filtration, to remove small bits of support material or embedded dust
- And diameter stabilization, which relies on an adaptive nozzle to output filament in standard 1.75mm or 2.85mm form
The recovered filament is deposited onto a spool that sits inside a temperature-controlled chamber to ensure proper cooling and roundness. The result, according to the research team, is material that is “comparable in quality to virgin filament in most use cases.”
The system is currently optimized for single-material thermoplastics such as PLA and PETG. Multi-material prints and high-temp polymers remain a challenge due to the precision required for thermal targeting, though Dr. Lupin says they’re working on a next-gen dual-spectrum MeltVac head to address that.
Early prototypes of the Unprinter have already been tested in several university labs and maker spaces, where users report that it has significantly reduced the volume of discarded prints. One beta tester noted, “I used to throw away about a kilo of failed prints every month. Now I just feed them back into the system.”
There are still some limitations: prints with embedded metal components, painted surfaces, or certain adhesives can clog the MeltVac if not pre-sorted. And while the system includes a calibration routine to adjust for color variation in recycled material, users hoping for consistent filament shades may need to temper expectations.
Nevertheless, the implications are significant. If commercialized, the Unprinter could offer a real path toward more sustainable desktop manufacturing — especially in environments where prototyping churn is high.
As for availability, MICFab has not announced a release timeline, though they say they’re in discussions with several hardware manufacturers to explore licensing options.
“This is not just about recycling,” said Dr. Lupin. “It’s about completing the loop. Making 3D printing truly circular — without all the mess.”
Via Materials in Additive Systems Quarterly