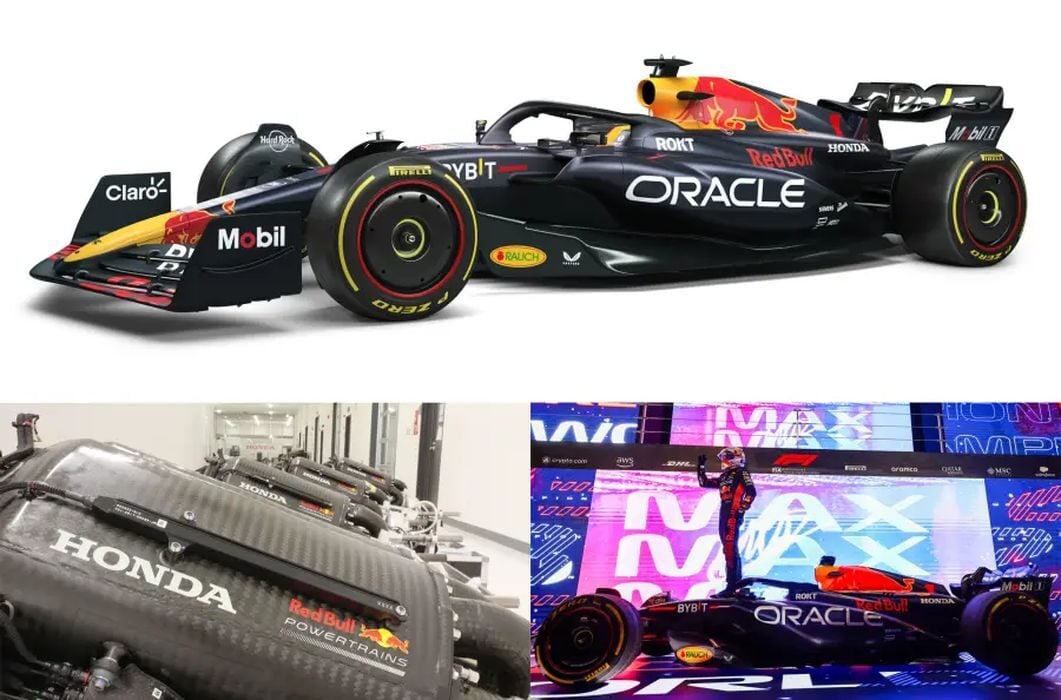
Charles R. Goulding and Preeti Sulibhavi underscore how Honda’s embrace of 3D printing technology is transforming manufacturing, from Formula One innovations to customized car parts.
Honda, a global leader in automotive innovation, has embarked on a transformative journey by integrating 3D printing technology into its manufacturing processes. This strategic move marks a significant shift from traditional methods to advanced additive manufacturing, underscoring Honda’s commitment to innovation and efficiency.
A Shift Towards Additive Manufacturing
For years, Honda maintained a cautious stance on adopting 3D printing for large-scale manufacturing. However, recent developments indicate a decisive pivot towards embracing this technology. This transition aligns with the company’s philosophy of organic technological advancement, favoring internal innovation over mergers and acquisitions. The previously considered merger discussions with Nissan, which did not materialize, may have inadvertently propelled Honda to focus on internal technological enhancements, turning potential setbacks into opportunities for growth.
Expansion in the United States: The New Civic Plant in Indiana
In a strategic move to bolster its manufacturing footprint in the United States, Honda announced the construction of a new Civic plant in Indiana, a project initially slated for Mexico. This decision reflects Honda’s commitment to strengthening its presence in the U.S. market and leveraging local resources for production efficiency.
Honda’s Established Operations in Ohio
Honda’s presence in Ohio has been a cornerstone of its North American operations. The company operates several key facilities in the state, including:
- Marysville Auto Plant: Established in 1982, this plant was Honda’s first automobile production facility in the U.S., producing models like the Accord and Acura TLX.
- East Liberty Auto Plant: Opened in 1989, it manufactures models such as the Honda CR-V and Acura RDX.
- Anna Engine Plant: This facility produces engines and components, serving as a critical hub for powertrain production.
These Ohio-based operations have been instrumental in Honda’s manufacturing strategy, emphasizing quality and innovation.
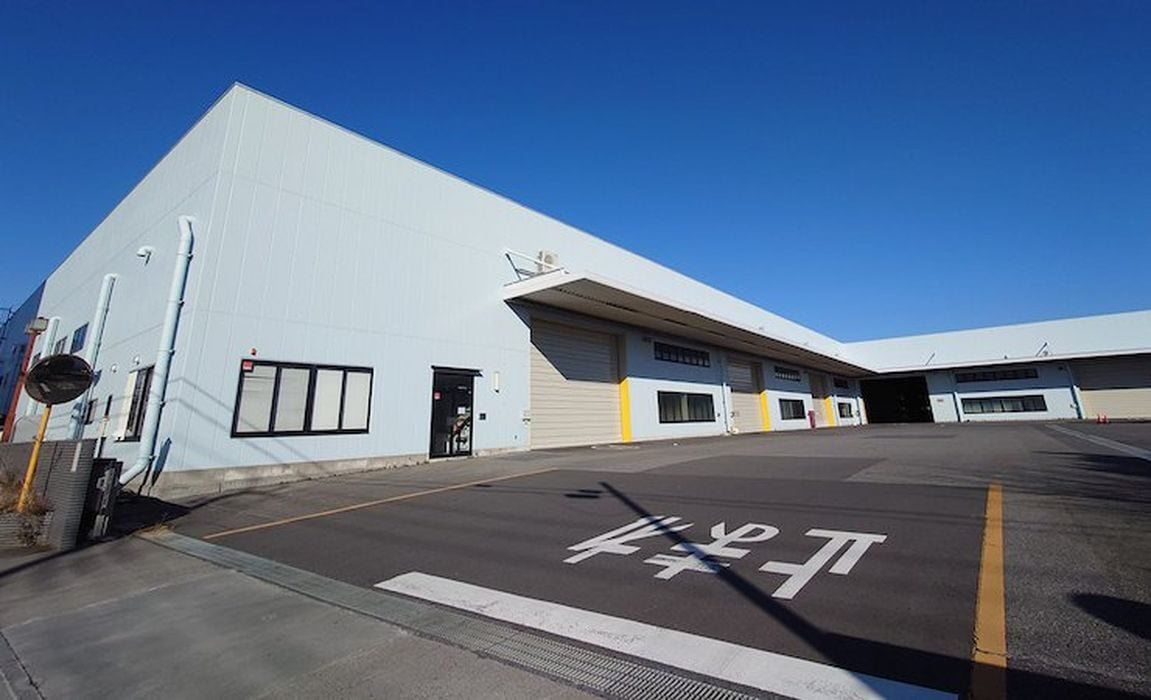
Collaborative Efforts: Honda and Nikon’s 3D Printing Initiative
In a landmark collaboration, Honda has partnered with Nikon to enhance its 3D printing capabilities. This alliance aims to integrate advanced metal additive manufacturing into Honda’s production lines, enabling the creation of complex components with improved efficiency. Nikon’s expertise in precision equipment complements Honda’s manufacturing prowess, promising advancements in the production of intricate parts.
Innovations in Engine Components
Honda has made significant strides in utilizing 3D printing for engine components, particularly in its Formula One endeavors. Since 2020, the company has employed Laser Powder Bed Fusion (LPBF) technology to fabricate parts with complex geometries and reduced weight. Notable applications include:
- Pistons: Transitioning from forged aluminum to 3D printed iron pistons, Honda achieved components that are both lightweight and capable of withstanding high combustion pressures.
- Turbine Housings: The use of 3D printing has enabled the production of turbine housings with enhanced design flexibility, contributing to improved engine performance for F1 racing team Oracle Red Bull.
In fact, Honda has begun to use 3D printing for more customized, interior car parts, like with the Honda CR-V.
Formula One: A Testing Ground for 3D Printing
Honda’s involvement in Formula One has served as a dynamic platform for testing and refining 3D printing applications. The high-stakes environment of F1 racing demands rapid prototyping and the production of lightweight, durable components. By integrating 3D printing into its F1 operations, Honda has been able to:
- Accelerate Development Cycles: The ability to quickly produce and test new parts has shortened development timelines, allowing for swift iterations and enhancements.
- Optimize Performance: Custom-designed components tailored to specific performance requirements have led to measurable gains on the track.
This strategic integration of 3D printing in Formula One not only enhances racing performance but also provides valuable insights for mass production applications.
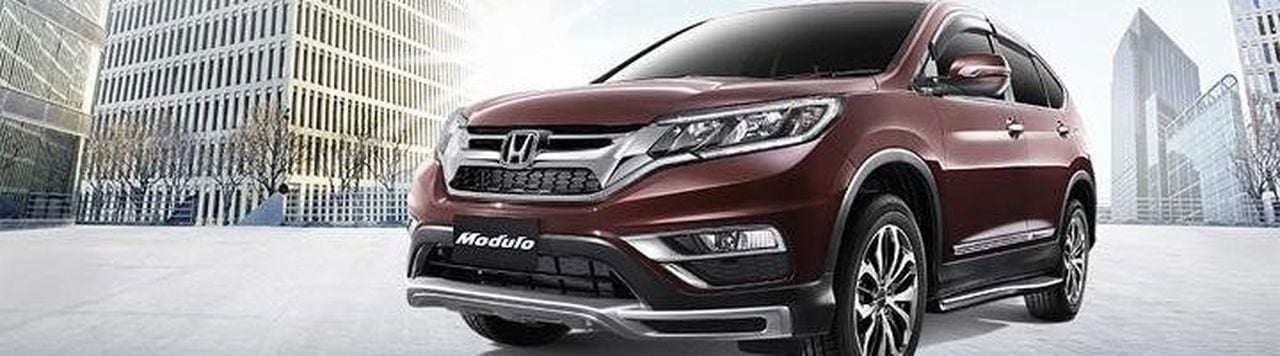
Looking Ahead: The Future of 3D Printing at Honda
Honda’s commitment to 3D printing signifies a broader shift towards advanced manufacturing technologies. By embracing additive manufacturing, Honda aims to make their production more customized, material-efficient and reduce their need for extensive supply chains and crowded inventories.
Below is a table the represents the increase in research and development spending over the last few years.
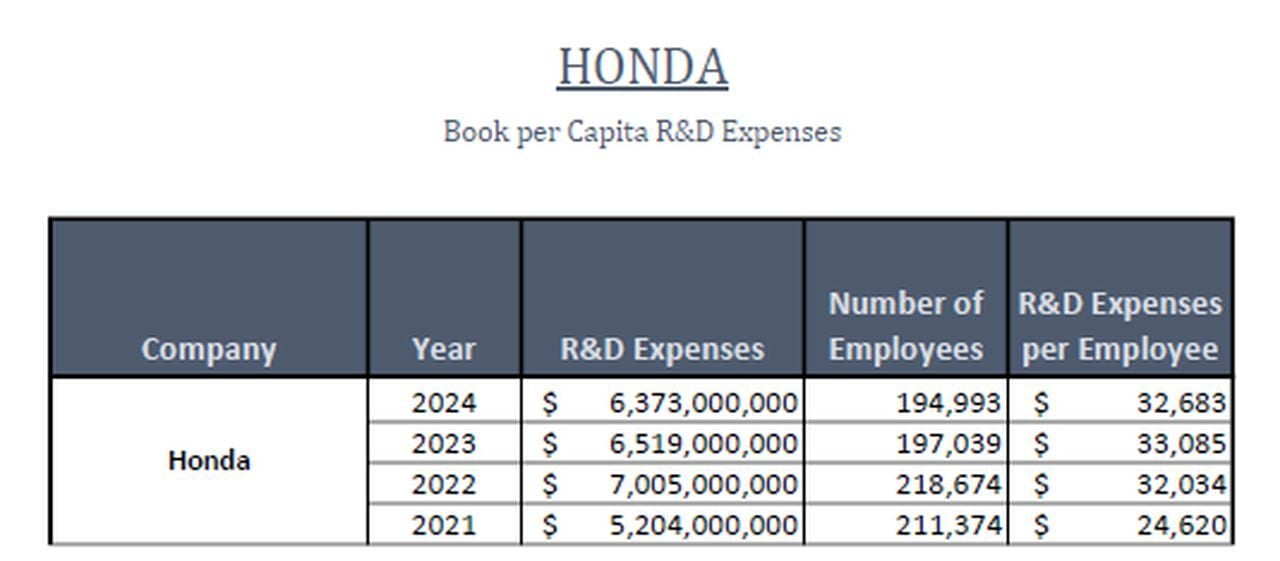
The Research & Development Tax Credit
The now permanent Research and Development (R&D) Tax Credit is available for companies developing new or improved products, processes and/or software.
3D printing can help boost a company’s R&D Tax Credits. Wages for technical employees creating, testing and revising 3D printed prototypes are typically eligible expenses toward the R&D Tax Credit. Similarly, when used as a method of improving a process, time spent integrating 3D printing hardware and software can also be an eligible R&D expense. Lastly, when used for modeling and preproduction, the costs of filaments consumed during the development process may also be recovered.
Whether it is used for creating and testing prototypes or for final production, 3D printing is a great indicator that R&D Credit-eligible activities are taking place. Companies implementing this technology at any point should consider taking advantage of R&D Tax Credits.
Conclusion
Honda’s integration of 3D printing technology represents a pivotal advancement in automotive manufacturing. By leveraging 3D printing, the company is poised to enhance efficiency, innovation, and sustainability across its operations, setting a new standard in the industry.