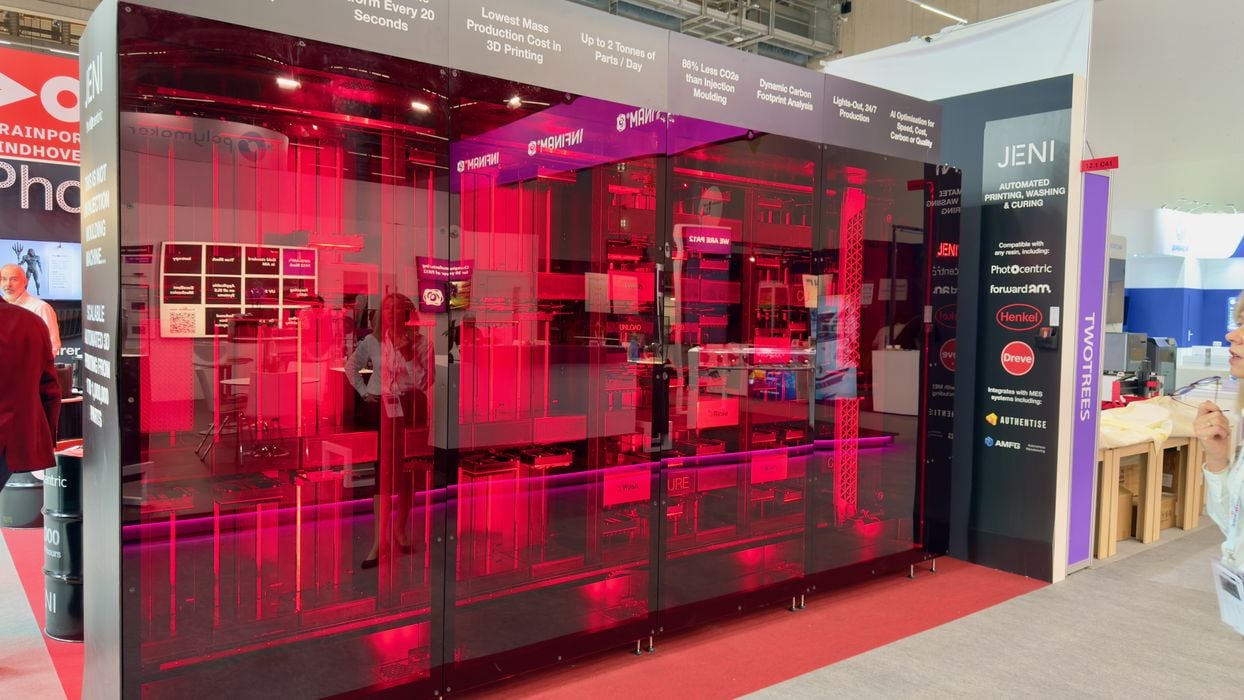
I had a bit of a shock at Formnext when looking at Photocentric’s new JENI product.
Photocentric produces not only 3D printer resin but also a growing portfolio of industrial resin 3D printers, some of which are quite large.
This was the first time I had a close look at JENI, which is a modular resin 3D print farm concept. The system involves modules that can contain printers, washers, and curing stations.
JENI involves a robotic system to take completed print plates off the printers and move them through washing and curing stages, and eventually piling up completed plates. They also have the ability to remove parts from the plate, but that has to be customized per customer as it depends on the part design and characteristics.
I asked about the washing system, which uses Photocentric’s own solvent. The wash is a multistage affair, with a final cleaning to completely remove any remaining resin. I wondered about how the solvent is handled, because over time it would become saturated with resin and become ineffective.
It turns out that in the JENI system the solvent remains in each wash cell but is constantly pumped and filtered. There are sensors that can automatically determine when it’s time to replace the solvent because of over saturation. At that point, the solvent is pumped out and replaced with fresh solvent.
The JENI concept is able to handle up to 30 modules, with a single module able to handle up to nine resin 3D printers. Of course, you’ll need a mix of wash and cure modules, and the ratio depends on the application.
The JENI system is also capable of reporting CO2 emissions for print jobs, as shown here.
So far, this may sound interesting but not revolutionary. It’s at that point I was told of the throughput of JENI.
It can produce a completed print platform every 20 seconds.
TWENTY SECONDS.
Is this due to print speed? The 3D printers involved print at a respectable 60mm/hour, which is not the fastest we’ve seen. However, putting multiple systems in parallel truly ramps up the production throughput.
Photocentric told us JENI can print TWO TONNES OF RESIN EVERY DAY.
This is quite incredible. The throughput is so high that customers have to reconsider how they use the system. For example, Photocentric related how one client wanted a “lights out, 24/7” setup. Photocentric suggested that they didn’t really want that because the machine, unattended over the weekend, would produce gymnasiums full of parts, all on its own. They’d need operators just to keep up with the output.
Photocentric said the system can produce parts faster than traditional injection molding, and each of the parts produced can be unique.
As an example, they printed 300,000 small PCB board standoffs in an hour. The barrel above shows these parts, and they were all of excellent quality.
The enormous throughput of JENI causes different approaches to system tuning. A customer might work really hard to knock one gram off a part — because a million parts would add up to a tonne of material. Similarly, by tweaking the layer size from, say, 0.100mm to 0.115mm, the throughput can be correspondingly increased.
Photocentric said the throughput of the machine allows for part costs that are about the same as injection molding.
Did Photocentric just beat injection molding? I’m not quite sure, but it sounds like they are close. If so, this is a major milestone in 3D printing, which has always been thought of as a low-volume technology.
There’s more to be said about JENI and its implications.
Via Photocentric