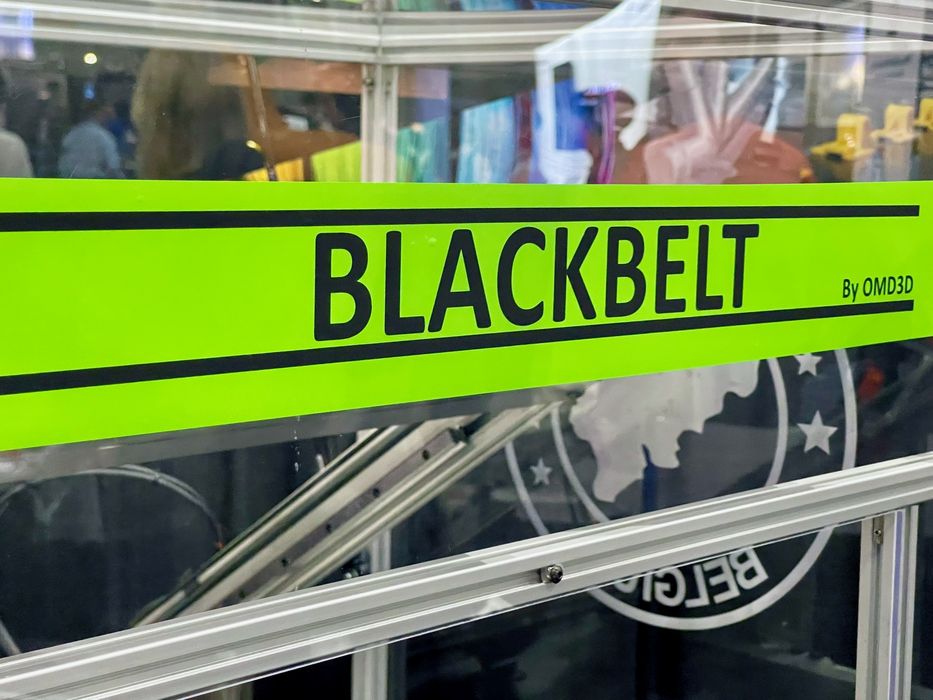
We received an update from OMD3D, the makers of the Blackbelt 3D printer.
A few years ago belt 3D printers were popping up all over, but it seems that most of the manufacturers have stalled out or stopped offering the machines. It’s not a surprise; belt 3D printing is a tricky business that offers interesting benefits, but also some challenges.
One of the first commercialized belt 3D printers was the Blackbelt, which appeared some years ago. The original makers of the device faded away to other projects, and the Blackbelt technology was taken up by OMD3D, the leading reseller for the belt machines.
Since the acquisition OMD3D has been making incremental improvements to the system. It still sports the unique carbon-fiber belt that is able to withstand considerable use, and now includes a number of interesting improvements.
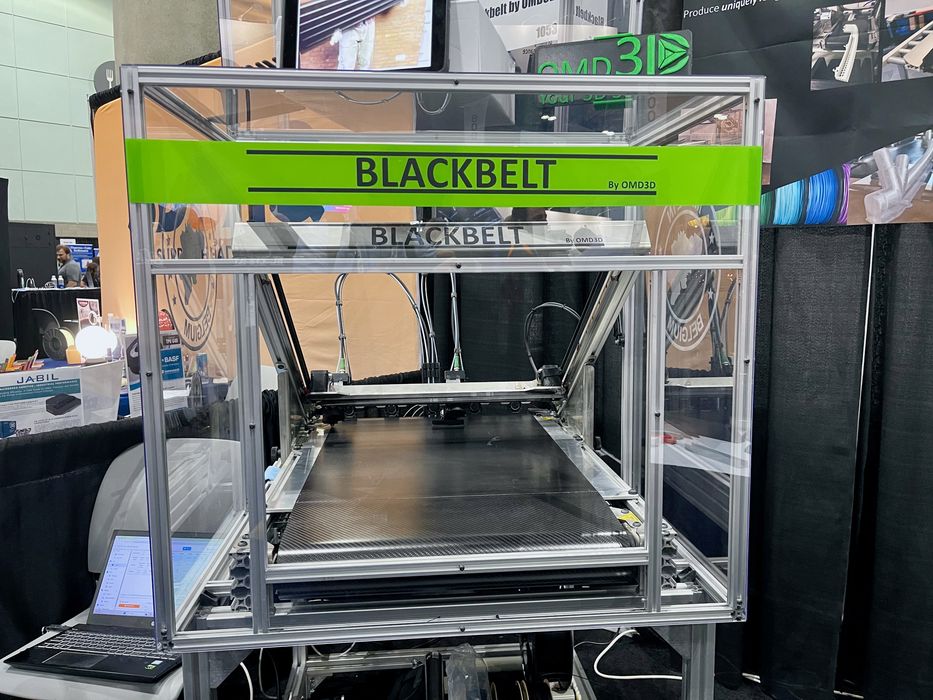
The machine has an optional enclosure, as you can see above. This is something that will help when printing higher temperature materials, which the machine is now capable of handling.
Another very interesting feature is independent extruders (IDEX), which allow printing of objects in a choice of up to two materials, or a “copy” using the second extruder. However, the system cannot yet print a single object in two materials. OMD3D CEO Peter De Corte explains:
“The IDEX dual extruder on the Blackbelt allows users to print with the Primary toolhead or with the Secondary toolhead or with both in COPY mode printing 2 same objects simultaneously.
For now it can’t print with the 2 heads on One object. Reason: None of the Belt slicers is ready for printing with 2 heads. We are looking for companies who can make a slicer with these features.”
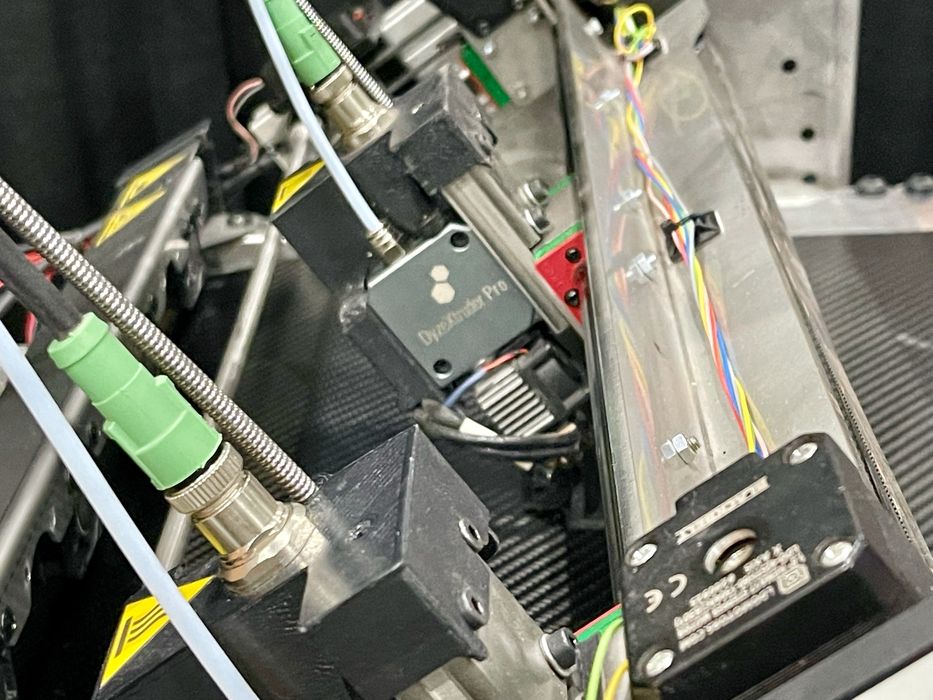
They also offer two models: one is a tabletop style that includes legs, while the other is the “Roller Table” version.
The Roller Table is an extension that has a series of rollers to accept longer printed parts. The roller table can support up to two meters in length, and likely permits printing of objects a bit longer than that. That’s something you just can’t do on most 3D printers.
I asked about the industries using the Blackbelt, and was told that there has been interest from the shipbuilding industry to produce end-use parts. They’ve also sold units to door manufacturers that use the system to produce profile prototypes. That makes sense, given the lengthy objects that can be made on the system.
There is now a wider version of the system available, taking the width up to 500mm. This means parts can be up to 500 x 340 x 2000+ mm in size.
There’s also work underway to develop a self calibration system for the printer. This may sound strange because self calibration is rapidly becoming a de facto standard feature on many desktop 3D printers.
Why couldn’t OMD3D simply re-use those approaches on the Blackbelt? It turns out that calibration is quite a bit different with the system due to the angled nature of the toolhead. Complicating the problem is that the angle of the toolhead can be changed on every job! Because of this OMD3D is working on ways to have the Blackbelt 3D printer calibrate itself before each job.
In the meantime the company provides mandatory training and installation (including in the USA) to minimize calibration issues.
Via Blackbelt 3D and OMD3D