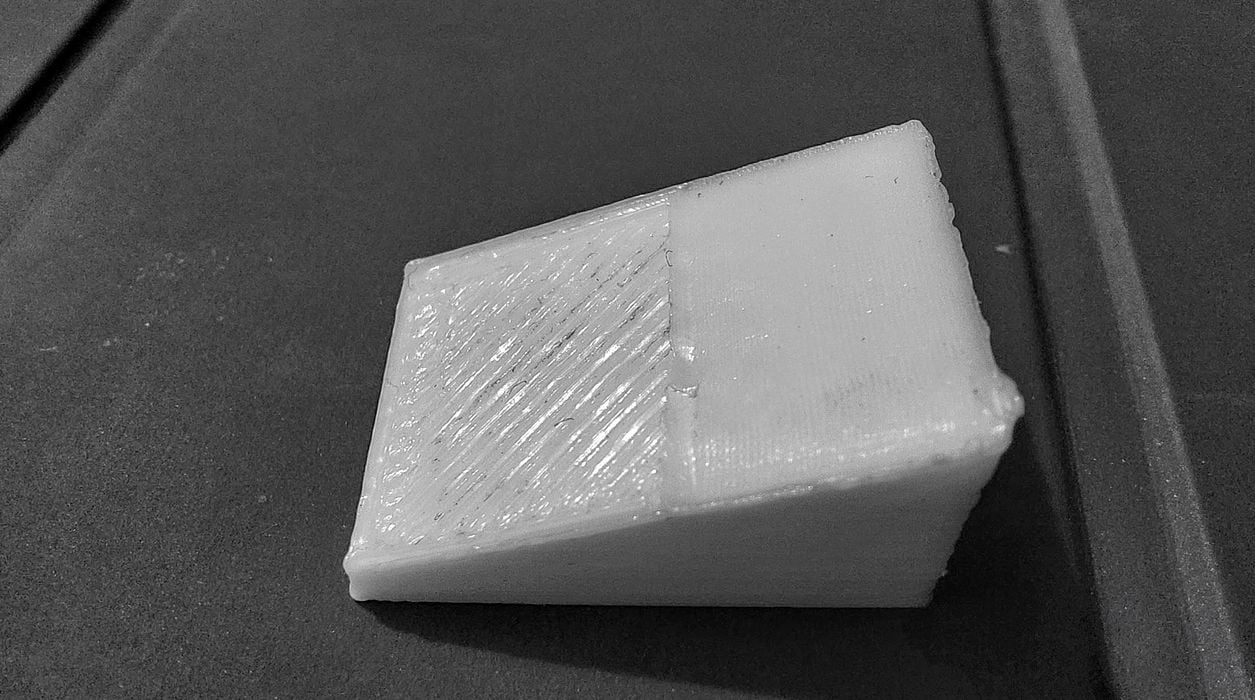
Researchers have identified an effective way to “iron” non-planar surfaces when 3D printing.
Ironing is a relatively recent practice in FFF 3D printing. The idea is to perfectly smooth flat surfaces by running the hot nozzle over that surface without extruding. The heat from the nozzle acts like an “iron” and smooths the surface.
Ironing is very effective and has been integrated into many popular slicing software systems. It works on basically any FFF 3D printer.
But it works ONLY on flat surfaces. It does not work on curved or angled surfaces.
To smooth angled or curved surfaces there are only a couple of not great options. One is “adaptive layers”, in which the layer size is decreased for heights where the curves exist. That works somewhat, but can greatly increase the job time. Another approach is to re-orient the print to present surfaces in a way that they print a bit smoother.
Aside from that, the only other approach is to mechanically smooth the surfaces, either by hand with sandpaper or a vibratory system, both of which can take considerable time and effort.
The researchers found a way to directly print smooth slopes and curves, but it’s actually quite complex. Their approach is a combination of practices performing ironing and non-planar 3D printing.
Hold on, what’s “non-planar” 3D printing?
Normal FFF 3D printing is “planar”, meaning each and every layer is a 2D plane. These are stacked together to form the object. Non-planar is the method of extruding 3D surfaces instead of planes for each layer. In other words, curved layers.
Non-planar 3D printing is quite challenging and has one severe limitation: the angle of extrusion, which is normally zero degrees for planar operations, cannot exceed the angle of the nozzle. If it does the nozzle will crash into printed material, ruining the job.
Nevertheless, it is possible to do some level of non-planar 3D printing with almost every FFF 3D printer.
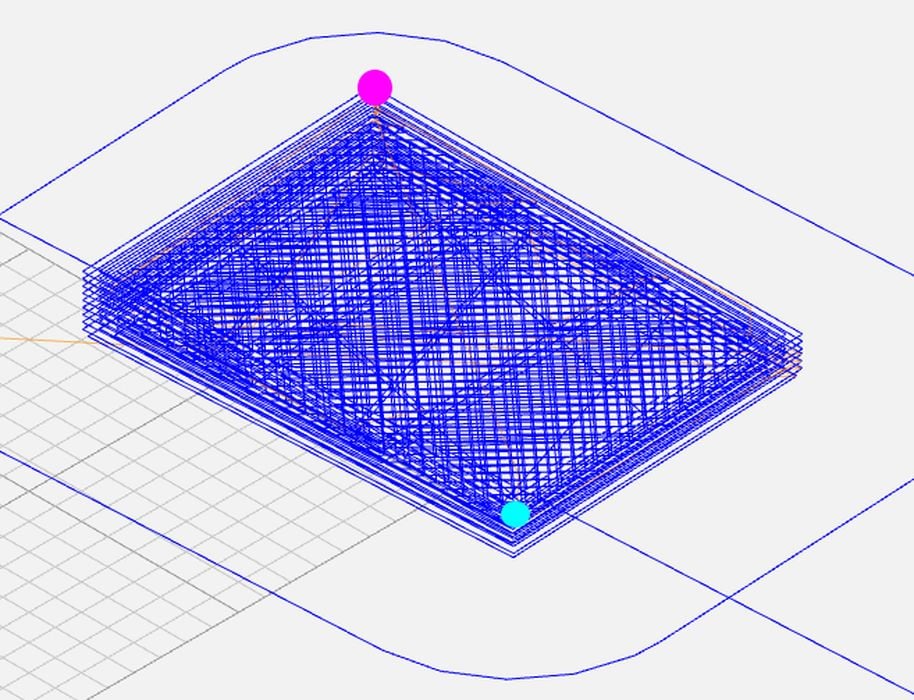
The new approach involves printing much of the object in planar style, but then applying non-planar toolpaths over top to create the smoother surfaces.
Their testing involved multiple common desktop FFF 3D printers and typical PLA materials. After considerable tuning, custom software development and a lot of testing, they were able to perform non-planar ironing.
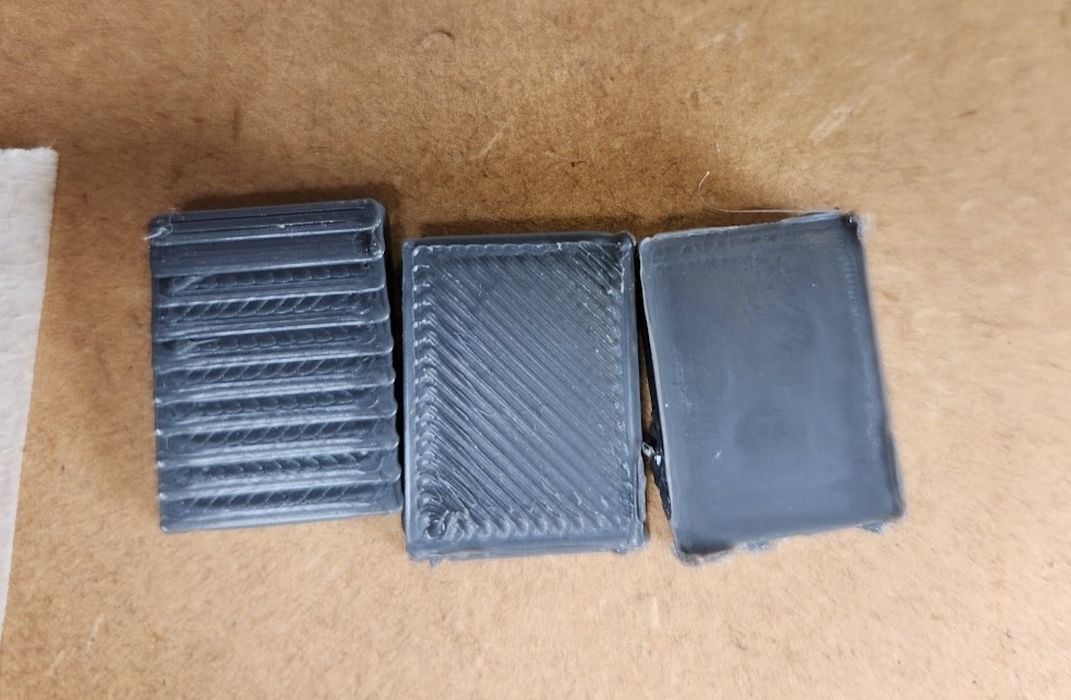
Here you can see an example of their approach. At left is the top of a typical angled surface, where the the classic stair-step pattern is seen. The middle example shows the same angled surface, but with a non-planar printing approach. The right example is the angled surface with their ironing approach. As you can see, it’s quite smooth.
They’ve even posted the code for their experiments to GitHub for anyone to test.
Finally, they say this:
“The results of using non-planar ironing have been very promising; they can be performed on entry-level material extrusion printers at no extra cost to machine owners. If this were to be integrated into slicing software for material extrusion 3D printers, it could greatly improve the appeal of owning a 3D printer.”
That should be the logical outcome of this work: Slic3r, PrusaSlicer, BambuStudio, OrcaSlicer, UltiMaker Cura and the rest should all integrate this function directly into the software so that everyone can make use of this powerful feature.
Via Exordo (PDF), Reddit, Google Photos and GitHub