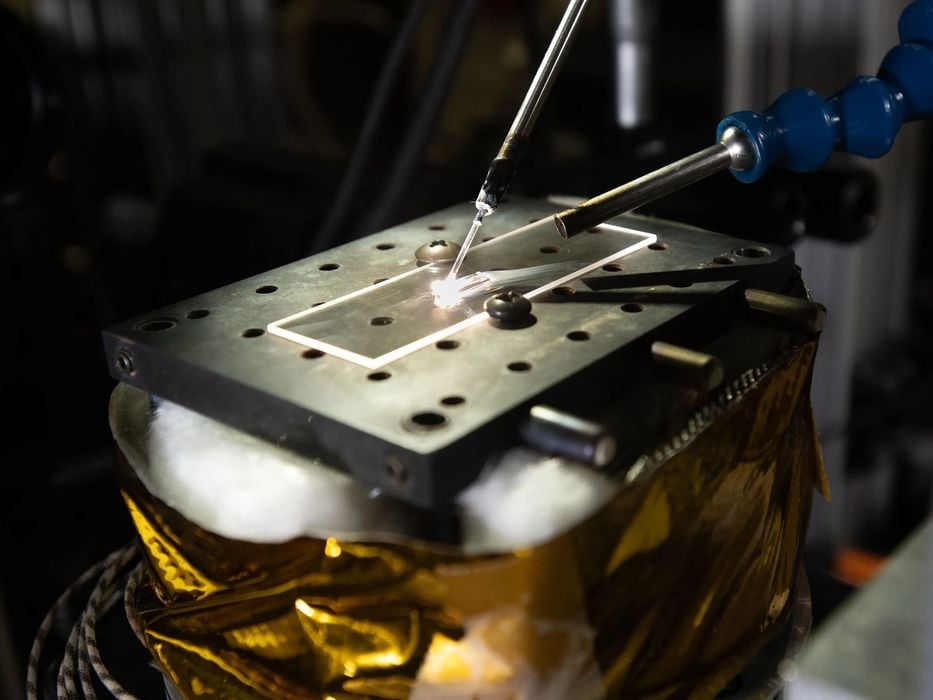
There’s been an important development in the ability to 3D print glass.
Many different materials have been used in 3D printers, but perhaps the rarest one is glass. Glass is a very unique material that not only offers transparency, but is also chemically resistant, high heat resistance and extreme rigidity. One can imagine the possibilities to create unusual glass geometries if a practical way to 3D print the material were unlocked.
There have been several attempts at 3D printing glass, but all have challenges of one kind or another. Two main approaches are used: extrusion, where glass rods are instantly melted with an energy source, and post-print sintering methods, such as SLA with glass-infused resin.
The sintering methods have challenges achieving usable glass densities, as well as having dimensional issues when objects shrink during post processing. The DED-style approaches overcome that, but are challenged by flow rates. They call this process Digital Glass Forming (DFG).
The main issue with glass DED 3D printing is that energy deposited on the glass material surface only penetrates a few micrometers, and to melt the interior time is required for heat to soak through. It doesn’t help to increase the energy levels, as then you risk vaporizing or bubbling the glass. As a result, glass DED 3D printing has been too slow for much practical use.
The researchers found a way around this limitation that could be very promising. They focused on the “surface heating” problem, and realized they could perform “volumetric heating” instead. A volumetric approach would heat both the surface and the interior of the glass at the same time.
How is this done? They start with a glass that is perfectly transparent to the laser. Then they dope the glass with a material that can absorb laser energy. The laser beam travels through the glass, heating up the distributed particles. It’s like uniformly placing an array of heaters inside the material.
They found that the method works extraordinarily well: their testing showed a prototype system able to deposit a surprising 15.3 cubic mm of glass material per second. This is actually higher than typical FFF 3D printers, but about half of today’s high speed FFF 3D printers.
However, the researchers noted that:
“These results show a deposition rate of V̇ = 15.7 mm3/s, which was limited by the maximum velocity of the motion stage, can be achieved.”
In other words, if they were able to re-engineer their motion system, the deposition volume could be even higher. This strongly suggests it might be possible to build a laser DED 3D printer able to print glass as fast as today’s high speed FFF devices print polymers.
It seems there is potential for DFG to become the primary way glass 3D printers could be built in coming years, and I’m certain someone will attempt commercialization of the technology.
Via Science Direct and IEEE Spectrum