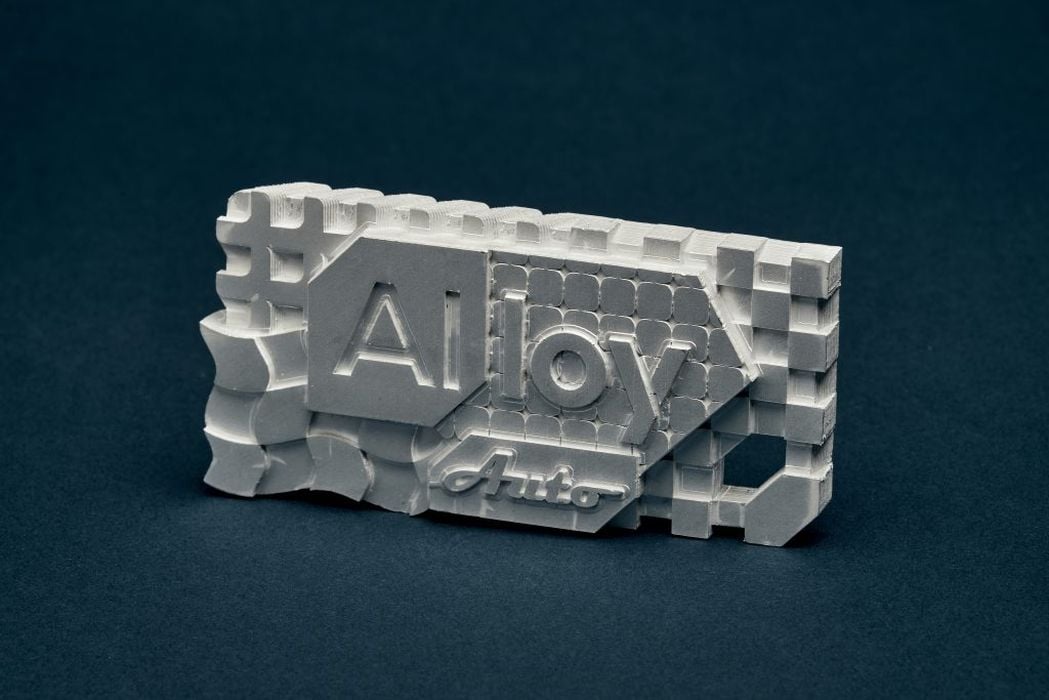
Charles R. Goulding and Preeti Sulibhavi discover how the latest U.S. tariff policies are driving innovation and growth in the 3D printing industry, reshaping the future of American manufacturing.
The recent shifts in U.S. tariff policy present significant opportunities for the 3D printing industry. Historically, U.S. trade policy deferred the implementation of tariffs when lower-cost sourcing alternatives were absent. Katherine Tai Biden’s trade ambassador made the new policy change clear. Previously, many importers “simply asserted that alternative products were unavailable because China remained the lowest cost source.” She went on further to say that extending their exclusions would delay the shift to “alternative sourcing and continue their dependence on Chinese suppliers and products which undermines the goal” of changing China’s behavior. This policy shift aims to reduce dependency on Chinese products by encouraging the development of alternative sourcing strategies, thus potentially benefiting the domestic 3D printing industry.
The New China Tariffs and 3D Printing
The updated U.S. tariff policy explicitly targets specific product categories, including personal protective equipment (PPE) and port cranes. This section will describe these new aluminum and steel tariffs and explore how the 3D printing industry must plan for these changes.
PPE Tariffs and 3D Printing

The PPE sector has seen a notable increase in tariffs aimed at encouraging local production and reducing reliance on Chinese imports. Companies like 3M Corp., a major player in the PPE market, have embraced 3D printing technology to enhance their manufacturing processes.
3M Corp.
- Employees (2023): ~95,000
- Sales (2023): US$34.8 billion
3M has integrated 3D printing into its production lines to create custom PPE components. This includes using 3D printing for prototyping and producing parts for respirators and face shields. The agility and speed of 3D printing enable 3M to quickly respond to changing demands and supply chain disruptions, providing a competitive edge in the PPE market.
Port Crane Tariffs and 3D Printing
Port cranes are another focal point of the new tariff strategy. By imposing tariffs on imported Chinese port cranes, the U.S. aims to stimulate domestic manufacturing and reduce dependency on foreign suppliers. The Chinese ship-to-shore crane import duty will go from 0 to 24 percent. 3D printing offers innovative solutions in the crane manufacturing industry by enabling rapid prototyping, customization, and cost-effective production.
Companies Utilizing 3D Printing in Crane Manufacturing
Several companies have pioneered the use of 3D printing in the crane manufacturing sector, demonstrating the technology’s potential to revolutionize the industry.
1. Konecranes
- Employees (2023): 18,000
- Sales (2023): US$4.1 billion
Konecranes has incorporated 3D printing for prototyping and producing customized crane parts. By using 3D printing, Konecranes can swiftly design and test new components, reducing the time and cost associated with traditional manufacturing methods. This approach enhances the company’s ability to innovate and maintain a competitive edge in the global market
2. Manitowoc Cranes
- Employees (2023): 5,800
- Sales (2023): US$1.8 billion
Manitowoc Cranes has leveraged 3D printing to develop prototypes and produce small-batch parts for their cranes. The flexibility of 3D printing allows Manitowoc to experiment with new designs and materials, optimizing the performance and durability of their cranes. This capability is particularly valuable in customizing cranes to meet specific customer requirements.
3. Liebherr Group
- Employees (2023): 49,000
- Sales (2023): US$14.5 billion
Liebherr Group utilizes 3D printing technology for both prototyping and manufacturing components for their cranes. The company has invested in advanced 3D printing systems that enable the production of complex parts with high precision. This technology not only accelerates the development process but also reduces material waste, contributing to more sustainable manufacturing practices.
Aluminum and Steel Tariffs
The proposed major increases in tariffs on Chinese Aluminum and Steel imports are already of major concern to many U.S. manufacturers. Aluminum is of major concern since there are only four U.S. aluminum smelters left operating. Two owned by Century and two by Alcoa. Possible alternatives include substituting materials and using recycled aluminum or steel.
Specifically, 3D printing aluminum for electric vehicle (EV) parts has grown increasingly popular. Three-year-old Alloy Enterprises, which is 3D printing aluminum, counts Lockheed Martin and Robert Downey Jr.’s venture fund among its early investors.
Alloy is developing and scaling 3D-printing technology that combines laser-cutting techniques and “diffusive bonding” (a solid-state welding method) to fabricate components for the automotive, industrial and heavy equipment sectors. It uses coiled sheets of aluminum as the raw input, instead of the powders typically required by other types of 3D metal printers.
“As Lockheed Martin endeavors to create an even more resilient, agile, efficient and cost effective supply chain, we see the unique additive metal process Alloy is developing as an enabling technology,” said Chris Moran, vice president and general manager of Lockheed Martin Ventures, in a statement. “We have several use cases for Alloy’s capability, and we want to see this technology succeed.”
The Research & Development Tax Credit
The now permanent Research and Development (R&D) Tax Credit is available for companies developing new or improved products, processes and/or software.
3D printing can help boost a company’s R&D Tax Credits. Wages for technical employees creating, testing and revising 3D printed prototypes can be included as a percentage of eligible time spent for the R&D Tax Credit. Similarly, when used as a method of improving a process, time spent integrating 3D printing hardware and software counts as an eligible activity. Lastly, when used for modeling and preproduction, the costs of filaments consumed during the development process may also be recovered.
Whether it is used for creating and testing prototypes or for final production, 3D printing is a great indicator that R&D Credit-eligible activities are taking place. Companies implementing this technology at any point should consider taking advantage of R&D Tax Credits.
Conclusion
The U.S. tariff policy changes represent a pivotal moment for the 3D printing industry. By encouraging domestic manufacturing and reducing dependency on Chinese imports, these policy shifts create opportunities for companies to innovate and strengthen their market positions. The examples of 3M Corp., the referenced crane manufacturers and Alloy enterprises illustrate how 3D printing can revolutionize manufacturing processes, enhance efficiency, and drive sustainable growth.
As the U.S. continues to navigate the complexities of global trade, the adoption of 3D printing technology will be instrumental in achieving a more resilient and competitive industrial landscape. This strategic alignment between policy and technology holds the promise of a robust and dynamic future for the U.S. manufacturing sector.