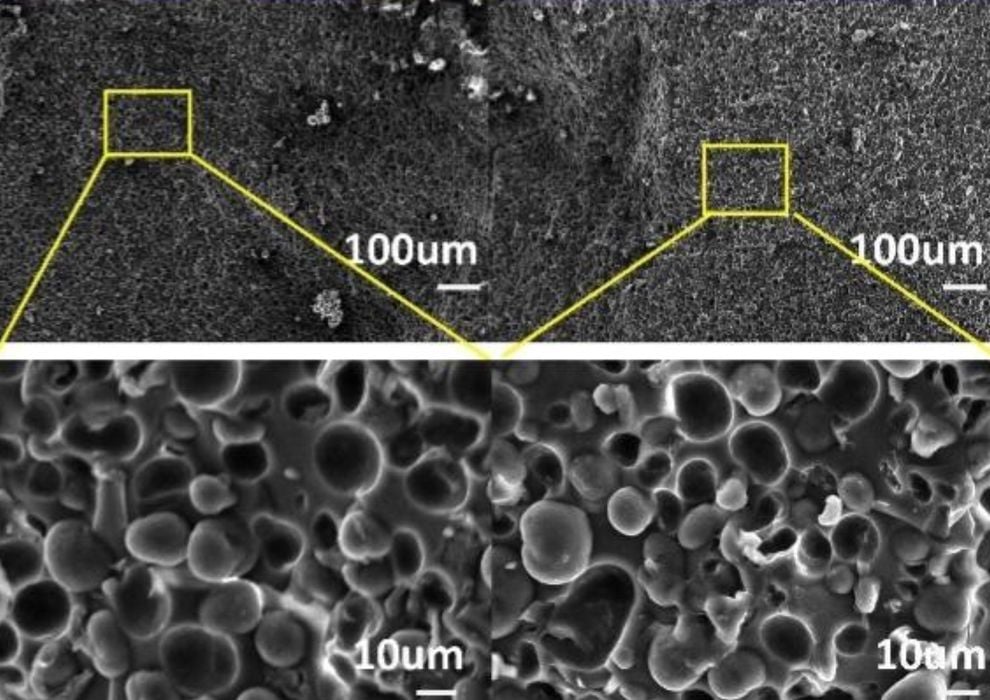
Researchers have proposed a method of 3D printing high temperature PEEK material using DLP technology.
PEEK is one of the most desirable engineering materials for additive manufacturing due to its strength, light weight and chemical resistance. It’s ideal for aerospace applications, and can even substitute for metal parts in certain situations.
There are two current approaches for 3D printing PEEK. By far the most popular is using FFF technology. PEEK filament is heated and extruded, layer by layer. However, there are challenges.
PEEK filament must be absolutely dry in order to achieve the best quality prints, and this requires the use of drying systems. These are sometimes integrated into the equipment, but are also available as standalone accessories.
Another issue is the heat required. PEEK has a far higher melting point than typical 3D print materials, and therefore requires hot ends that can reach 400C or more. In addition, PEEK tends to warp when printing, so the build chamber must be heated far higher than typical levels. Because of these reasons it is basically impossible to 3D print PEEK on common desktop 3D printers.
Now there may be a way to do so.
The researchers investigated the possibility of creating a special “PEEK ink” for use in a DLP-powered resin 3D printer.
Creating hybrid resins is actually common practice. It’s long been known that, for example, ceramic particles can be mixed in with resins to print ceramic “green” objects. These are fired in a furnace after printing to burn out the polymer and sinter the ceramic particles together.
Could something similar be done with PEEK? It turns out it is not only possible, but actually produces very good results.
The researchers first prepared the special resin by combining a typical photopolymer resin with PEEK powder. They ground up standard PEEK pellets with a planetary ball mill into very fine powder. These were mixed together into a 60% by weight PEEK slurry, which was used for 405nm DLP printing.
After printing the green part was then post processing in a muffle furnace. This single step operation both removed the polymer and sintered the PEEK particles together.
They found that prints made with the parameters they developed were of excellent quality, and high resolutions could be achieved. They write:
“The prepared PEEK ink is well-suited for the DLP 3D printing process. Process tests show that, under reasonable parameters, its printing accuracy surpasses the photosensitive resin system, reaches the theoretical resolution of the DMD in the commercial DLP 3D printer used, and effectively constructs complex aggregated architecture.”
They conclude:
“The results show that the proposed process can take full advantage of the PEEK material performance while achieves high-precision, flexible and easy-to-deploy architecture processing.”
The precision implies that small, complex PEEK parts could be built that are not currently achievable using FFF processes.
This is quite an important development, as this reveals another method for producing PEEK parts that could be quite accessible. In theory even home 3D printer operators could use this method, although they’d need access to a sintering service.
Via Arxiv (PDF)