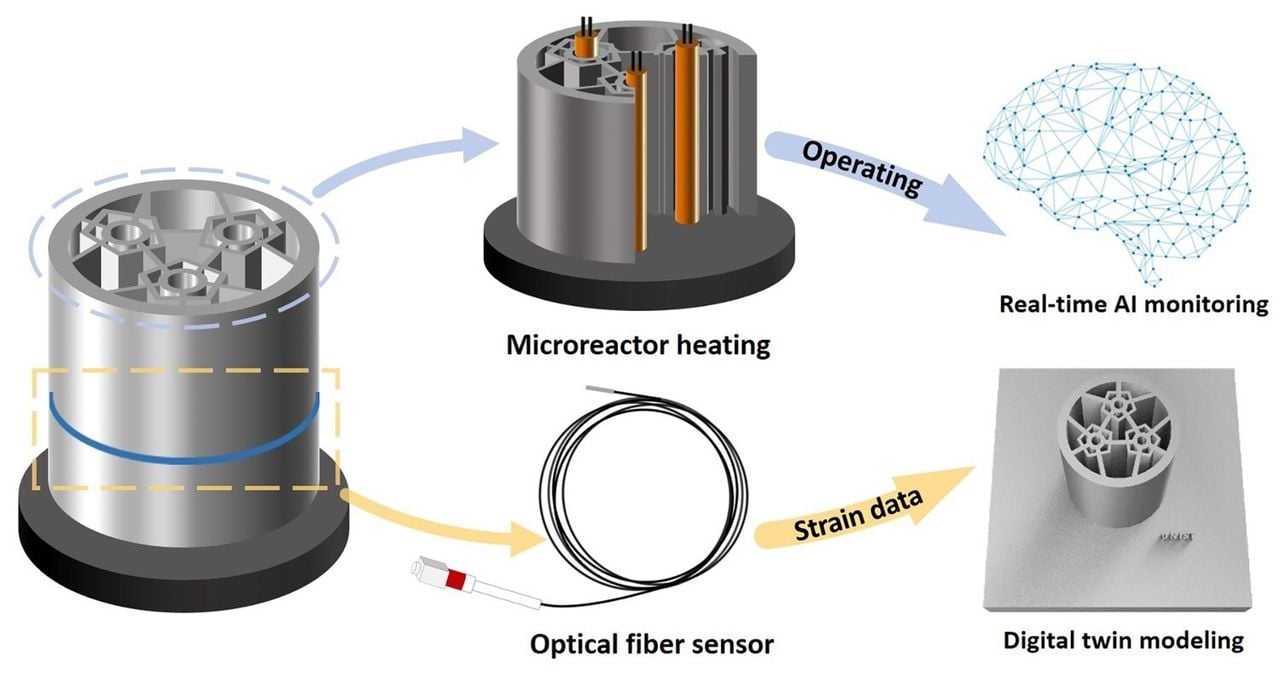
A new application area for additive manufacturing has been identified: micro reactors.
Nuclear reactors have been around for decades, and common belief is that they are enormous, expensive, labor-intensive, and dangerous. That’s probably true for older reactor designs, but newer designs employ considerably more technology than in the past.
Interest in using reactors for energy generation has been increasing after having been stalled for a long while due to radiation fears. However, with the ongoing climate emergency, the prospect of a completely green energy solution such as nuclear energy has been gathering attention.
In particular, the interest has been focused on what’s known as “micro reactors”. These are small reactors that generate in the single megawatt range and are suitable for installation in factories and some larger vehicles like ships and trains. Their reduced size dramatically lowers risks of radiation.
One of the advantages in the present day for reactor design is the availability of 3D print technology to produce the components. Reactor designs require complex geometries for cooling, sensors, and efficiency, and that sounds quite similar to another popular AM application: rocket engines.
The concept is to 3D print reactor parts and directly integrate features, all the while reducing the number of parts. Normally, conventionally designed parts would have to be bolted together, creating opportunities for failure along seams, adding hardware, part counts, and assembly time. By 3D printing more complex parts, it can greatly simplify the assembly and increase the reliability of the parts.
A new research paper has deepened the use of 3D print technologies by incorporating fiber optic sensors directly into the reactor components.
Reactors operate at high temperatures, and it’s critical to monitor them carefully to avoid failures. Past experiments have used sensors simply applied to the surfaces of the components, but in this study, the researchers embedded sensors inside 3D printed reactor parts.
How is this done? The sensors in the study were optical fiber cables, which can detect distortions caused by thermal effects. The 3D models of the parts were designed to include a channel to hold the optical sensor cable.
I wondered how they could 3D print a metal part and at the same time lay in a glass fiber — would the glass fiber not be disturbed (or even melted) by the ongoing DED metal deposition process?
It turns out they found a way to do this. The researchers explain in their paper:
“Embedding sensor within the metal component is carried out through a three-step process. In the first step, the bottom part of the metal component, including the sensor embedding space, is fabricated. The height of the bottom part is half of the total height, measuring 50 mm. In the second step, an optical fiber strain sensor is embedded and securely affixed within the sensor embedding space. A thermal protective layer is applied over the sensor to prevent thermal damage from the additional DED process. The thermal protective layer, which has a thickness of 3 mm and a width of 4.5 mm, is pre-manufactured with stainless steel 316L, the same material used in the DED process. During this process, the height of the first fabricated part and the thermal protective layer are made equal for subsequent fabrication steps.”
The protective layer was also extended to protect the sensors against hot metal particles flying away from the meltpool during the remainder of the printing process.
The researchers were able to successfully produce the part and were able to use the sensor as intended. This proves a new approach for producing additively manufactured reactor parts that can be used in a smart monitoring system.
This capability will undoubtedly be used as the micro reactor business grows. However, the fact that they were able to embed an optical cable during a metal 3D print is a capability that I am certain can be used in many other metal 3D print applications.