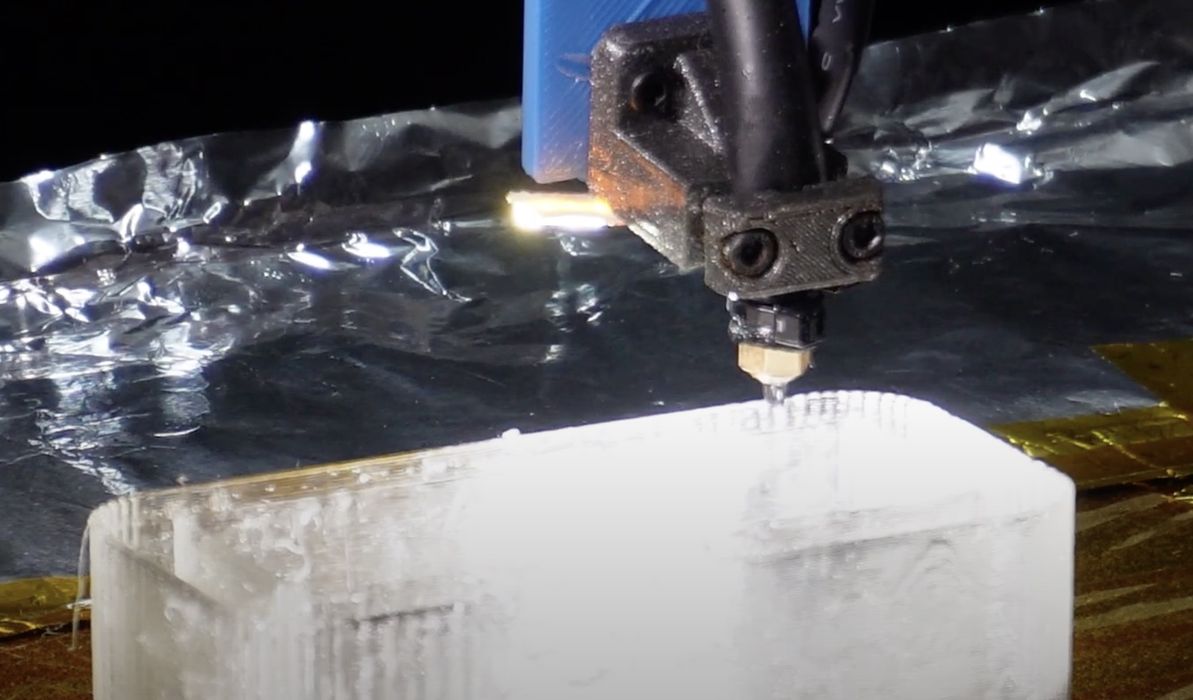
Modix announced a powerful new technology for their large-format 3D printers: Resin Infill Technology.
The Israeli company has produced large format FFF and FGF 3D printers for many years, and recently introduced a high-capacity extrusion system, the Griffin Ultra, and a massive large format FGF 3D printer, the MAMA-1700.
It’s a fascinating idea that I don’t believe has been attempted in the 3D print world: using a different technology for infill. Normally, FFF / FGF 3D printers simply print a sparse matrix of the same material as infill, where the density is varied according to part strength requirements.
The new Resin Infill Technology changes all that. By leveraging Modix’s existing independent extruder (IDEX) technology, they set up the second extruder as a dispenser of resin. As the print job proceeds, the resin is selectively deposited as infill in selected interior regions.
Unlike sparse infill, the resin will flow, so you will have 100% density for these resins in selected regions. However, there are many different resin types possible, including foam. This could approximate the sparse density traditional approach for lightweight prints.
Modix explained that Resin Infill Technology (RIT?) can make use of either single part or two-part resins. This means you can use UV-curable resins, just like SLA, or epoxies. This opens up many possibilities. For example, Modix explained:
“This advancement positions epoxy-filled 3D printed parts as a viable alternative to metal in certain high-end applications. Mixing Epoxy with longer than standard carbon fibbers will add additional strength and creates a new class of composite solutions.”
Using RIT it would be possible to produce parts that have greater strength, better water tightness, and more lightweight than typical 3D printed parts.
An example application to illustrate how this could work might be a surfboard. Imagine printing the exterior shell with a strong carbon fiber-infused polymer, and having the infill as lightweight foam. Or perhaps even carbon fiber-infused foam. You’d end up with an incredibly strong and super-lightweight surfboard.
Another advantage of RIT is cost. 3D print materials tend to be expensive per weight. If you avoid using them for infill and instead use a far less expensive resin, the parts produced could require reduced costs.
Another possible use of RIT would be for molding: if a sacrificial breakaway 3D print material was used, then it could be broken away to reveal a molded part inside. This may be of significant interest to the molding industry.
This surprising technology will be available as an option for Modix customers starting in “late 2025”, but will be shown to the public in a few weeks. We’ll be there to see it.
Finally, with this new technology it appears that Modix is set for expansion: interest in RIT could drive up sales, requiring additional manufacturing and staffing. Accordingly, Modix is now seeking external investors in the company for the first time. Modix explained:
“Due to the immense potential and wide-ranging applications of its new technologies, Modix is, for the first time, actively seeking investors or strategic buyers. The aim is to accelerate the development of its Resin Infill Technology, along with other groundbreaking innovations currently in stealth mode.”
Modix writes that they now have 4,000 installations around the world, and reached sales of US$7.4M last year. The new technology could enable significant growth for the company as new markets will open.
Via Modix