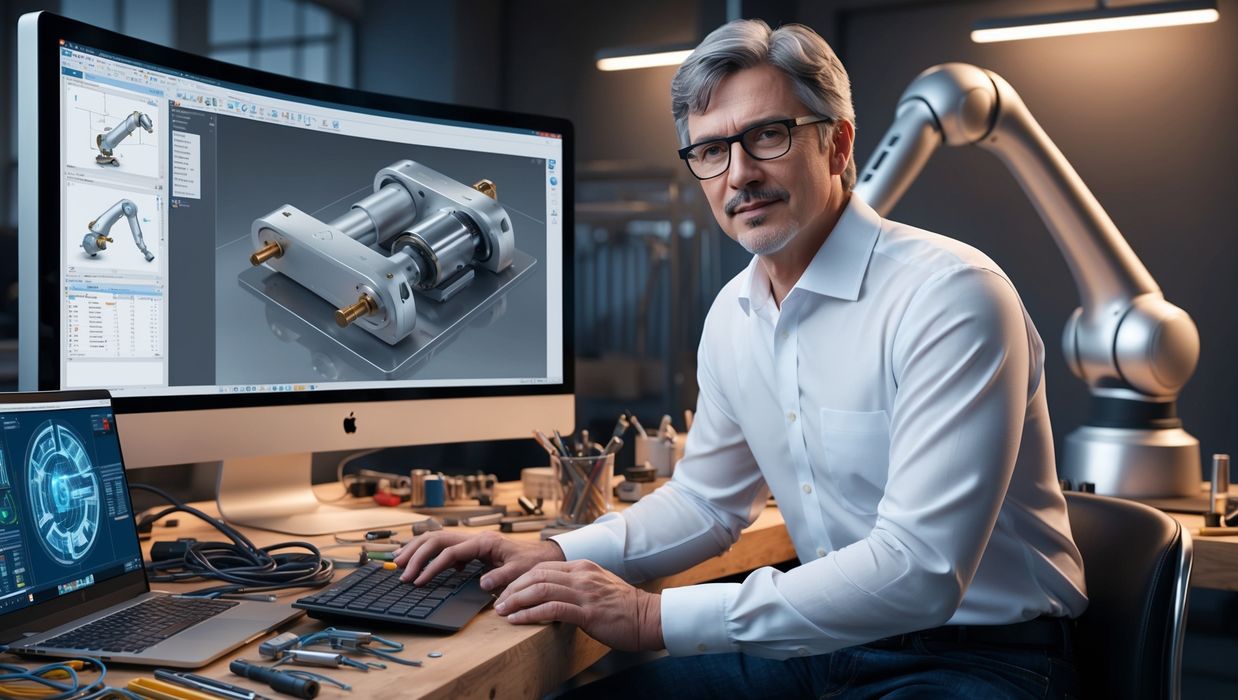
The task ahead is clear: cross-functional collaboration, systems interoperability, and business-digital strategy alignment.
The manufacturing industry in 2024 was a proving ground for transformative technologies. From AI-driven efficiency to the adoption of edge computing, product developers and manufacturing engineers learned critical lessons about what works—and what does not—in the relentless pursuit of speed and innovation.
Looking ahead to 2025, the focus will shift from technology adoption to mastery. This is about more than tools—it is about driving measurable outcomes through integrated and strategic approaches. Let’s break down the key takeaways from 2024 and explore the priorities for 2025.
2024: A year of ambitious gains and sobering realities
AI for Automation and Predictive Analytics
AI proved itself as a game-changer in 2024, enabling automation, predictive maintenance, and workflow optimization. However, achieving measurable ROI remained elusive for many. Successful organizations treated AI as a strategic investment aligned with business goals, not just a shiny tool.
Key lessons learned include:
- Companies that excelled used AI for defect detection, energy optimization, and production adjustments.
- Filling gaps in data quality and platform integration was a critical step toward unlocking AI’s value.
- Manufacturers need implementation roadmaps with measurable KPIs to ensure AI adoption delivers real results.
Robust Digital Thread Foundations
Seamless integration across PLM, ERP, and MES platforms emerged as a significant competitive advantage in 2024—but not without challenges. Establishing digital threads required technical rigor, governance, cross-functional process and data alignment.
Key lessons learned include:
- End-to-end integration enabled faster design cycles, fewer production errors, and smoother operations.
- Engineers played a pivotal role as data stewards, ensuring accuracy and driving adoption of best practices.
- Software providers must prioritize not just APIs but also functional use cases that deliver measurable outcomes.
Decentralized Processing and Edge Computing
Edge computing revolutionized data processing by bringing it closer to the production floor. This enabled real-time analytics, adaptive robotics, and dynamic production controls—allowing machines to make decisions autonomously.
Key lessons learned include:
- Decentralized systems introduced complexities, requiring a balance of performance, security, and infrastructure resilience.
- Engineers faced challenges ensuring secure, uninterrupted data flows across networks.
- Scaling edge computing depends on effectively managing infrastructure robustness and agility.
Security and Network Infrastructure
As connected devices proliferated, manufacturers became prime targets for sophisticated cyberattacks. In response, zero-trust frameworks and AI-powered threat detection became essential.
Key lessons learned include:
- Security must be embedded from the design phase, not added as an afterthought.
- Operational technology (OT) and IT systems convergence created new vulnerabilities requiring proactive management.
- Cybersecurity resilience is no longer optional—it is fundamental to digital transformation.
2025: from adoption to mastery
In 2025, manufacturers will move beyond technology adoption and focus on integrating tools to drive strategic business outcomes. Success will depend on scalability, governance, and workforce enablement as organizations shift from experimentation to enterprise-wide transformation.
Here is what lies ahead and how manufacturing engineers can lead the charge:
AI as the Orchestrator
AI will evolve from incremental improvements to a central orchestrator of production processes, supply chains, and energy efficiency. To enable this transformation, engineers must focus on building robust, scalable infrastructures.
Key priorities include:
- Data governance: Is the data fueling AI clean, accurate, and accessible?
- Interoperability: Does AI seamlessly integrate with PLM, MES, ERP, and other systems?
- Scalability: Can AI solutions adapt to growing production complexities?
- Workforce enablement: Are AI insights designed to empower human decision-making?
- Mastering AI in 2025 means ensuring it drives autonomous, intelligent, and value-driven operations.
Scalable, On-Demand Solutions
Cloud-based solutions and Everything-as-a-Service (XaaS) will dominate manufacturing in 2025, offering flexibility, reduced costs, and faster time-to-value. Manufacturing engineers must bridge legacy systems with cloud platforms to enable this transition.
Key priorities include:
- Integration roadmaps: How will legacy systems connect to cloud-native platforms?
- Cost-value balance: What are the trade-offs of XaaS versus on-premises systems?
- Infrastructure optimization: Are cloud resources configured for performance and minimal latency?
- Complexity management: How will hybrid environments with legacy and cloud systems be managed?
- Success will depend on striking the right balance between scalability and operational stability.
Non-Negotiable cybersecurity foundation
With AI, IIoT, and edge computing driving increased connectivity, cybersecurity must be embedded into every phase of the manufacturing lifecycle. Engineers will play a leading role in ensuring systems are resilient and secure.
Key priorities include:
- Security-first design: Are systems designed with embedded security protocols from the outset?
- OT-IT convergence: How are production systems safeguarded while integrating with IT systems?
- Real-time risk monitoring: Are AI-driven tools used to proactively detect and mitigate threats?
- Team education: How can engineers enable teams to recognize and respond to cyber risks?
- In 2025, neglecting cybersecurity will carry far greater risks than the cost of proactive investments.
IIoT: The Standard for Operations
In 2025, IIoT will transition from an innovation to a baseline standard for all manufacturers. The real challenge will be mastering IIoT to drive clear, actionable results.
Key priorities include:
- Actionable insights: How will raw sensor data be translated into strategic actions?
- Device interoperability: Are diverse IIoT platforms seamlessly connected?
- Scalability: Can IIoT systems grow alongside production demands?
- Security: How are connected devices protected from vulnerabilities?
- Manufacturing engineers must focus on turning IIoT data into decisions that enhance efficiency, reduce costs, and drive competitive advantage.
Read the rest of this story at ENGINEERING.com