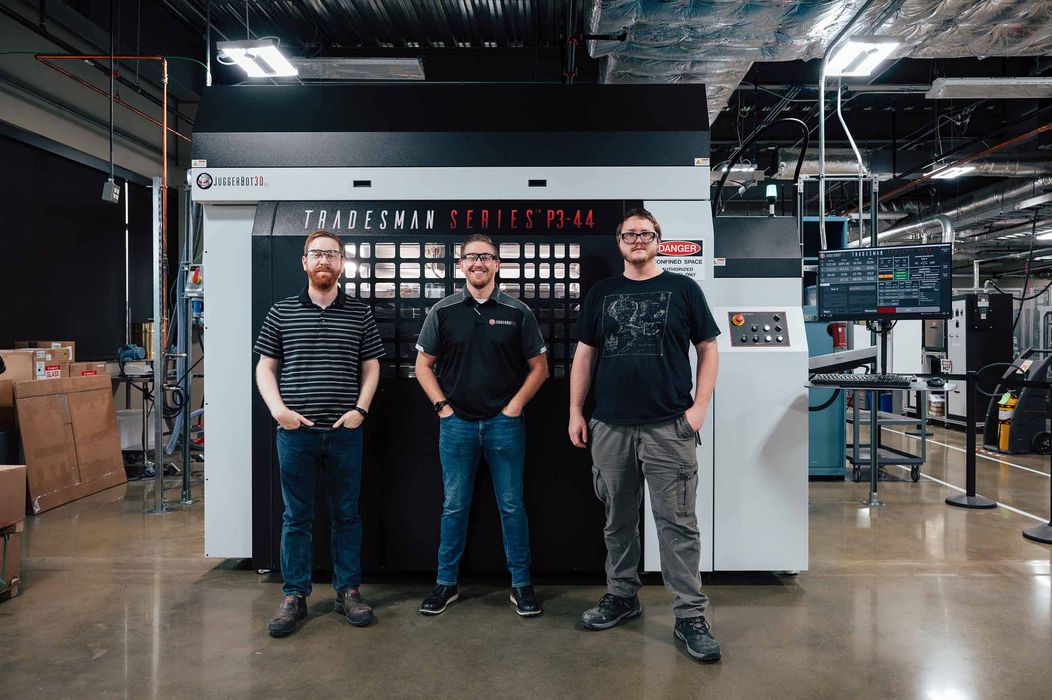
JuggerBot3D announced partners for a very intriguing project with the USAF.
The company announced that Mississippi State University’s Advanced Composites Institute (ACI) and Oak Ridge National Laboratory (ORNL) will join their project, but what is it all about?
It’s a US$4M project announced earlier this year that intends on developing new methods, materials and technology to enable rapid creation of production tooling for composite manufacturing.
In other words, the USAF wants ways to build new systems much more quickly, and they’re looking for ways to achieve that goal from JuggerBot3D and partners.
JuggerBot3D currently produces a large-format 3D printer that uses the FGF process. They’ve done considerable work to perfect FGF on their equipment, including the development of a “Material Card” that is somewhat analogous to a FFFF “Print Profile”, except that it is for pellets.
This is where it gets interesting. In the press release, JuggerBot3D explains:
“The project involves the development of a system integrating two-part resin and pellet-fed material extrusion technologies, processing performance-grade thermoplastic polymers and advanced thermoset resin inks, including epoxies and vinyl esters. The system is designed to reach build volumes of 360 ft³, showcasing critical process controls synonymous with JuggerBot 3D’s additive technologies. Throughout the project, set to be completed in December 2025, several phases of technology development will occur, from system development to comprehensive modeling and advanced tool path development.”
There’s several things to unpack here.
First, JuggerBot3D does not currently market any non-FGF 3D print technology. Two-part resin and advanced thermoset resin ink technologies would be entirely new to the company.
This may be one of the reasons they’re partnering with the two research institutions, as they may have experience in those areas where it could be new to JuggerBot3D. JuggerBot3D explains how ORNL will work with them:
“RNL and JuggerBot 3D will enhance slicing software and printer hardware to process thermosets independently and simultaneously with thermoplastics. As a result, JuggerBot 3D will also develop and integrate thermoset Material Cards.”
The implication here is that when the smoke clears, JuggerBot3D will have the technology to produce an unusual hybrid 3D printer that uses both FGF and Two-Part resins simultaneously. I am not aware of any other 3D printer manufacturer that has this unusual technology combination.
The other interesting item to note is the 360 cubic foot build volume. Converting that to standard 3D print measurements, this would be equivalent to a build volume of 2170 x 2170 x 2170 mm, or about seven feet on a side.
JuggerBot3D’s current flagship 3D printer, the Tradesman P3-44 has a build volume of “only” 914 x 1219 x 1219 mm. The proposed build volume would be almost 8X the size of the P3-44’s build volume.
In other words, JuggerBot3D seems to be building a very large-format 3D printer — and one that has the unusual hybrid resin-FGF technology.
This technology will certainly be useful for tooling, as huge structures could be printed for composite layups, likely faster than traditional methods. The USAF’s partners will then be able to develop aerospace systems much faster.
But that same technology will no doubt be of similar benefit to non-military manufacturers of larger composite parts. It’s likely that JuggerBot3D will have themselves quite an attractive product for this market in 2025.
Via JuggerBot3D