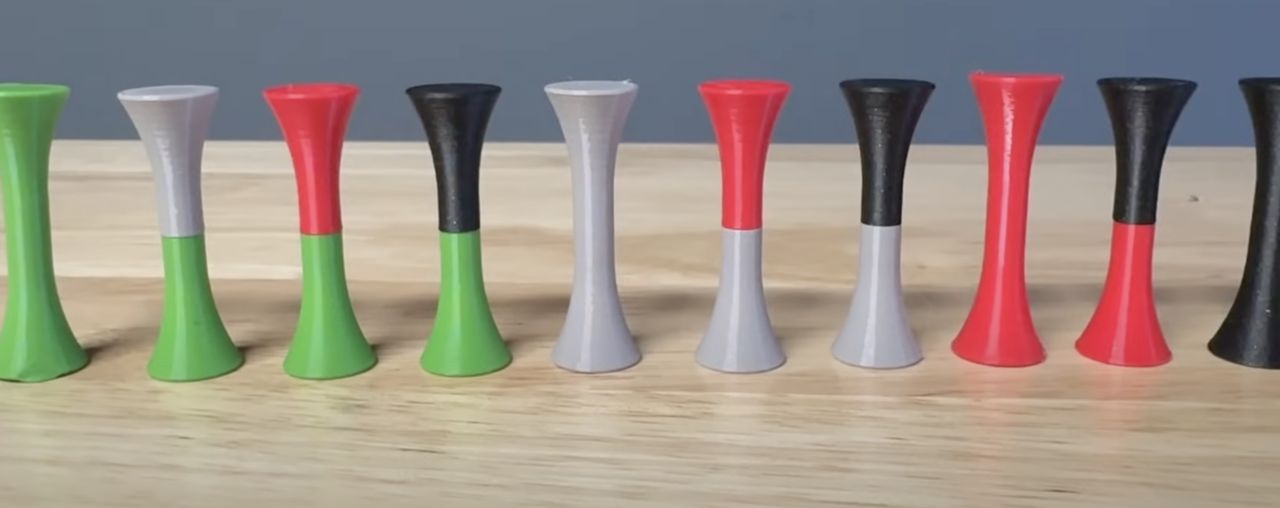
JanTec Engineering has an ingenious way to reduce 3D printed part warping through the use of multiple materials.
The concept involved mixing diverse materials in a 3D print, usually done with a multimaterial-capable device. We’ve all heard that, for example, ABS and PLA don’t adhere to each other, so it might be possible to use one as a support material for the other.
But is this really true? JanTec Engineering decided to do a proper study of mixing materials, and the results are extremely interesting.
Four materials were investigated: PLA, TPU, PETG, and ABS. JanTec Engineering prepared ten combination coupons as shown at top. These were then placed in a test rig to measure the level of adhesion between the materials.
Above you can see the results of this test, and it has some surprising findings. PLA and ABS, for example, adhere quite well to each other, suggesting that combination is not a good choice for support materials.
PLA and PETG, however, don’t adhere at all to each other, and therefore would be ideal as support materials for each other.
JanTec Engineering tested this combination by printing a PETG chain with an enormous amount of PLA support. The result was near perfect, as the PLA supports simply broke away easily. This negates the need for purchasing expensive breakaway support materials.
Another finding was that this technique often means the support material differs in color from the model material. That makes it very easy to distinguish any remaining support material on the print, as shown here. Normally, this whisker of support material would be invisible.
Finally, the major discovery is focused on printing ABS. ABS is a fine material for end-use parts, but it is terrible to 3D print. That’s because it is highly prone to warping. It’s basically impossible to reliably 3D print ABS (or its sibling ASA) on a non-enclosed 3D printer, even if the plate temperature is a whopping 110°C.
JanTec Engineering realized that the PLA to ABS adhesion could be a positive in this case: why not print a thin layer of PLA on the first few layers, and then print the ABS part on top of that?
The experiment succeeded very well, showing how it could be quite straightforward to print ABS — if you have a multimaterial 3D printer, such as the Prusa XL, as used by JanTech Engineering.
A side benefit is that the energy use is decreased: PLA requires only 50-60C temperatures on the build plate, while ABS requires at least 100C. This will also speed up print jobs, because it takes far longer to reach 100C on the build plate.
This is all quite interesting, and should have implications for both 3D printer manufacturers and slicing software developers: these concepts could be more directly integrated into the system so that these approaches could be more easily used by 3D printer operators.
Meanwhile, it should be possible to attempt these methods on any multimaterial desktop 3D printer. Note, however, that there are some issues when doing so.
One is that some of the materials have radically different temperatures. If using a single nozzle multimaterial machine, this will require heating and cooling of the hot end on each and every material swap. That could dramatically increase the print job’s duration.
A second problem is simply support. The Bambu Lab A1 and A1 Mini, for example, do not support printing ABS material: it does not appear in their slicing software. For this, you’d have to fool the machine by specifying a “PETG” material with ABS temperatures, for example.
This is outstanding work by JanTec Engineering, and I hope it changes how we all 3D print in the future.
Via YouTube and JanTec Engineering