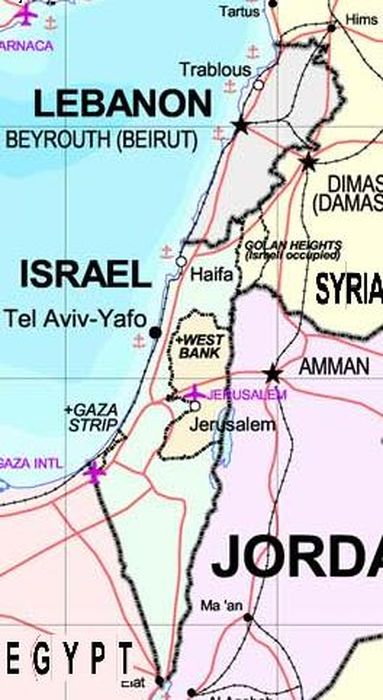
Preeti Sulibhavi and Ryan Donley uncover how Rafael is leveraging 3D printing technology to accelerate production, streamline repairs, and maintain its edge in the global defense industry.
Rafael has been in the news lately since Hezbollah targeted some of its plants with recent attacks. The irony is the Iron Dome thwarted the attack and Rafael is a co-creator of the Iron Dome. Rafael is unique since it is an Israel state-owned defense company.
The defense company has a unique skill set with many leading technologies including 3D Printing, Air & Missile Defense, Air & Space, Land Warfare, Naval Warfare, Intelligence & Cyber, and Multi-Domain Rafael has experienced a recent surge in employees who were conscripted for Israel military service and are now actively participating in the ongoing war effort.
Rafael is transferring engineers from multiple firm branches to backfill vacancies as well as hiring for hundreds of open positions. The defense company is currently seeing a tremendous increase in order backlogs year-over-year, and the current backlog is US$8 billion.
Amid these challenges, Rafael has strategically embraced advanced technologies, including 3D printing, to accelerate production, streamline prototyping, and enhance maintenance capabilities. 3D printing, allows for more flexibility in design, faster turnaround times, and cost efficiencies, all of which are crucial in the defense sector. By leveraging 3D printing, Rafael not only maintains its technological edge but also reduces dependence on traditional supply chains, an invaluable asset during times of increased demand and operational strain. In the last few years, Rafael has integrated 3D printing across its product development and repair workflows, making it a core component of its manufacturing ecosystem.
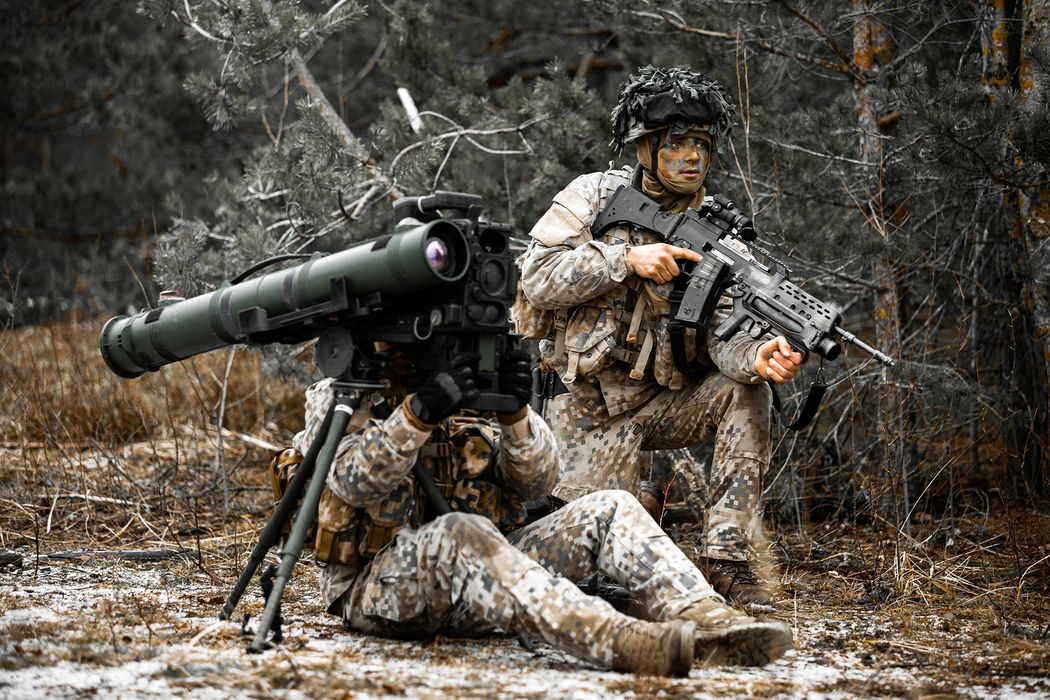
How Rafael Uses 3D Printing in Its Operations
1. Prototyping and Development of the Spike Missile Family (2020)
One of the most significant applications of 3D printing at Rafael is in the prototyping and development of its Spike missile family. The Spike missiles are electro-optical guided missiles, which include the Spike NLOS (Non-Line Of Sight), Spike LR (Long Range), and Spike ER (Extended Range), among others. They are key assets for both offensive and defensive operations in land, naval, and air combat.
In 2020, Rafael started using 3D printing for the rapid prototyping of components used in the Spike missile series. Traditionally, missile prototypes were time-consuming to produce, involving multiple rounds of costly tooling and molds. However, by integrating 3D printing, Rafael was able to significantly shorten the time it took to produce early-stage prototypes and iterate designs. This was especially beneficial for the Spike NLOS, which requires precision-engineered guidance systems. Engineers could now 3D print these systems to test different configurations, reduce design flaws, and finalize functional prototypes within weeks rather than months.
The use of 3D printing also extended beyond the prototype phase into the manufacturing of small, complex parts that would otherwise require specialized machining processes. This allowed Rafael to keep production agile and adaptable to the changing needs of its clients. Given the highly variable and fast-paced nature of global defense requirements, this flexibility offered a strategic advantage to Rafael.
2. Repair and Maintenance of the Iron Dome System (2021)
Another key area where Rafael has integrated 3D printing is in the repair and maintenance of its flagship Iron Dome missile defense system. The Iron Dome, which intercepts short-range rockets and artillery shells, has been a pivotal defense tool for Israel since its deployment. However, with frequent deployments and operational wear, maintaining the Iron Dome’s readiness is a priority for Rafael, especially in conflict zones where downtime can be critical.
In 2021, Rafael implemented 3D printing in the field to manufacture replacement parts for the Iron Dome. Previously, if a component of the system was damaged, technicians would have to wait for replacement parts to arrive, which could take days or weeks depending on the location and severity of the damage. Now, with mobile 3D printing units deployed in key operational zones, Rafael’s teams can produce small, intricate parts for radar systems, launchers, and interceptors on-site, significantly reducing repair times.
For example, one of the most critical components in the Iron Dome is the radar system, which detects and tracks incoming threats. The radar system is composed of many small, high-precision parts that must function perfectly for the system to operate effectively. By 3D printing these components, Rafael can ensure that even if a part fails, it can be replaced quickly, ensuring that the Iron Dome remains operational at all times. This capability was first demonstrated during a series of tests in 2021, where Rafael successfully produced and installed 3D printed radar parts on-site in under 24 hours, significantly reducing the Iron Dome’s downtime.
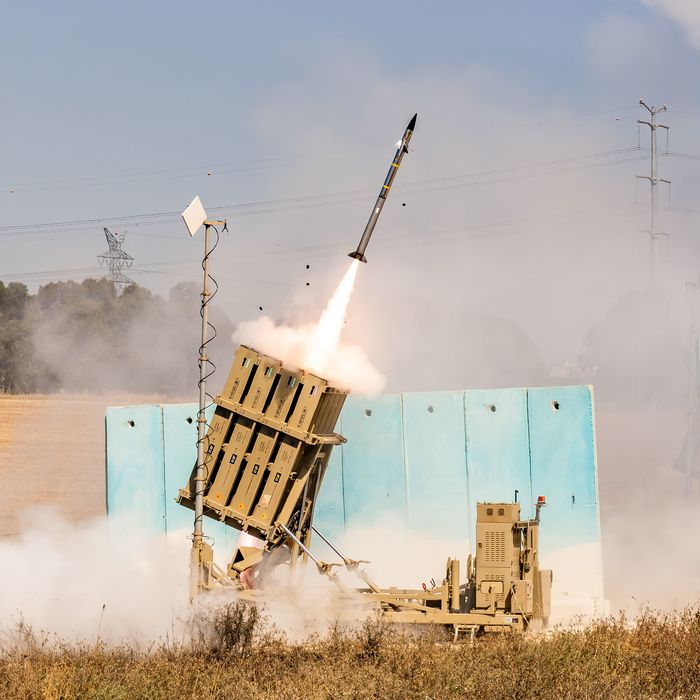
3. Streamlined Production of Drone Components for Firefly UAV (2022)
In 2022, Rafael took another significant step in its adoption of 3D printing by incorporating it into the production process for the Firefly UAV (Unmanned Aerial Vehicle). The Firefly is a loitering munition, often described as a “suicide drone,” designed to provide soldiers in the field with an autonomous, highly maneuverable asset that can loiter above a battlefield and strike targets with pinpoint precision.
One of the biggest challenges Rafael faced with the Firefly UAV was the need for lightweight, durable materials that could withstand harsh combat environments while keeping production costs low. Traditionally, producing such materials would involve expensive alloys and complex machining processes, which limited the speed at which Rafael could ramp up production to meet demand.
In 2022, Rafael introduced 3D printing into the production process for key structural components of the Firefly, including its airframe and propulsion system. Using additive manufacturing, Rafael was able to produce these parts out of advanced composites, which reduced weight while maintaining structural integrity. 3D printing also allowed for more streamlined production lines, as parts that once required multiple manufacturing steps could now be produced in a single process. This not only sped up production but also allowed for more customized designs based on operational feedback from the field.
In particular, the Firefly’s lightweight airframe was redesigned using 3D-printed components, resulting in improved maneuverability and flight endurance. The rapid production capability also gave Rafael the flexibility to scale up manufacturing as the need for UAVs increased, especially in response to rising global demand for loitering munitions. This innovation was a critical factor in Rafael’s ability to fulfill a surge in orders for the Firefly UAV in 2022, meeting both domestic and international demands.
The Research & Development Tax Credit
The now permanent Research and Development (R&D) Tax Credit is available for companies developing new or improved products, processes and/or software.
3D printing can help boost a company’s R&D Tax Credits. Wages for technical employees creating, testing and revising 3D printed prototypes can be included as a percentage of eligible time spent for the R&D Tax Credit. Similarly, when used as a method of improving a process, time spent integrating 3D printing hardware and software counts as an eligible activity. Lastly, when used for modeling and preproduction, the costs of filaments consumed during the development process may also be recovered.
Whether it is used for creating and testing prototypes or for final production, 3D printing is a great indicator that R&D Credit-eligible activities are taking place. Companies implementing this technology at any point should consider taking advantage of R&D Tax Credits.
Conclusion
Rafael’s adoption of 3D printing across its production, prototyping, and repair processes has been a game-changer for the company, enabling it to stay ahead in the highly competitive and ever-evolving defense industry. The use of additive manufacturing has allowed Rafael to develop sophisticated systems like the Spike missile family, maintain the operational readiness of the Iron Dome, and streamline the production of advanced drones like the Firefly UAV. In an industry where precision, speed, and adaptability are paramount, Rafael’s strategic use of 3D printing gives it a crucial edge in delivering cutting-edge defense technologies.
As Rafael continues to face growing demand for its products and services, the role of 3D printing in its operations will likely expand, further cementing its place as a leader in both defense innovation and manufacturing. With this technology, Rafael is well-positioned to respond to the challenges of the modern battlefield, whether in terms of rapid prototyping, field repairs, or high-volume production, ensuring its products remain at the forefront of global defense capabilities.