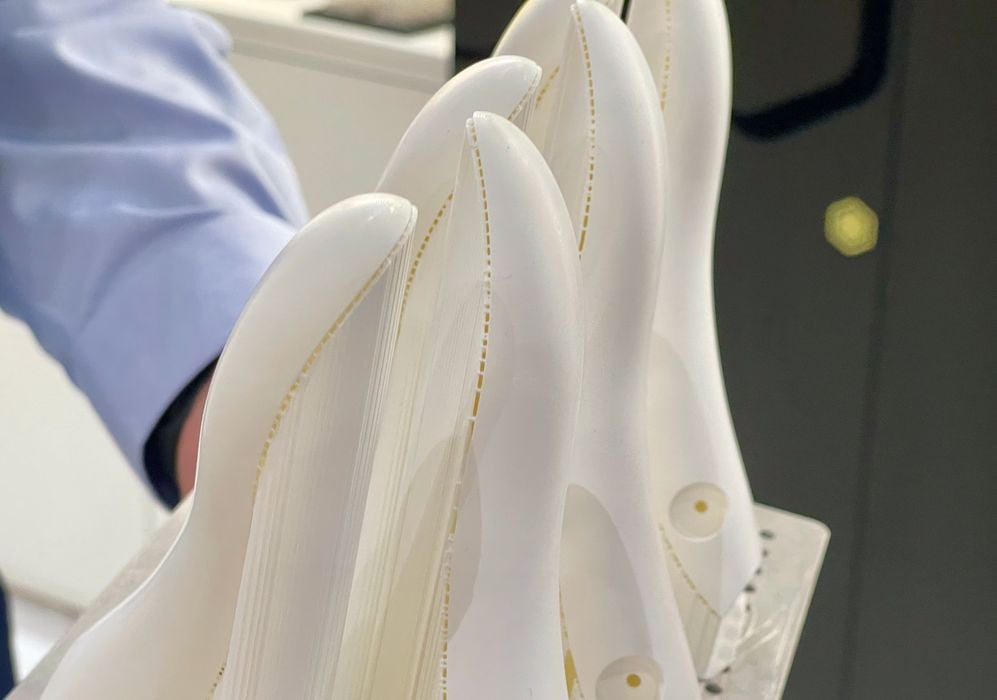
I spent some time at Rapid with Rajeev Kulkarni, Axtra3D’s new Chief Strategy Officer.
Axtra3D has been developing a unique resin 3D printing system that seems to be gathering momentum. The key feature of their Hybrid PhotoSynthesis Technology (HPS) process is that it uses BOTH DLP and laser light engines in the same machine.
Why do this? DLP resin 3D printers offer fast printing because complete layers are printed at once, but surface quality can suffer because of the pixel-based nature of DLP. SLA / laser 3D printers produce high quality surfaces due to the smooth laser movements, but take far longer to print. HPS combines both: the interior is quickly printed with DLP, while the exterior perimeter is lasered for smoothness.
I believed that this approach was more than sufficient to produce high quality prints in record time, but it turns out there are more interesting technology features in Axtra3D’s equipment that lead to even greater quality and speed.
Kulkarni walked me through four key features that enable quality and speed. One, of course, is the DLP-laser combo, as discussed above. But what are the other three?
One deals with the layer changes, which are very challenging on resin equipment. Typically fresh layers tend to adhere to the bottom of the resin tank, and must be slowly peeled off. This is not only slow, but can also produce forces that damage delicate structures. Some companies overcome this with tricky chemical surfaces on the resin tank, a flow of oil within the tank or an oxygen layer to prevent adhesion.
Axtra3D solves the problem with a most interesting mechanical approach: they simply slide the print plate sideways.
The slide motion introduces no hydrostatic forces as normally occur on typical resin 3D printers. It’s also fast and dramatically speeds up the print process.
Another feature is dual Z-axes holding the print plate. Normally there’s only one, and that can allow the plate to “tip” very slightly. Two axes hold the plate much firmer.
Finally, Axtra3D has included a series of sensors that help position the plate at the correct height for each layer. Normally this is not done on other machines, as the plate is expected to mechanically land within a range of possible heights.
A competing machine, for example, hits the height within 0.08-0.20mm. To compensate for the variation, the machine’s setting essentially overexpose the resin to ensure curing takes place through the entire layer. That can reduce the quality of the print because the extra exposure can “bleed” solid material where it shouldn’t occur.
The combination of these four features results in prints with amazing quality.
If that wasn’t enough, Kulkarni explained that Axtra3D is an open materials company, and they currently have a number of materials certified for HPS, including resins from Henkel, BASF, 3D Systems, Keystone, Pro3Dure, NextDent and INFINAM, among others.
The company has a goal of certifying 50 materials for HPS by the end of this year. Apparently it takes about two weeks for their techs to certify a material, so even if one isn’t listed, they’ll certify it for you — at no charge.
Via Axtra3D