
Charles R. Goulding and Preeti Sulibhavi explore how FTAI Aviation’s unique approach and potential integration of 3D printing could revolutionize the aerospace industry.
FTAI Aviation, a relatively small but rapidly growing company, has recently been making headlines in the aviation sector. FTAI Aviation operates under a unique business model that has positioned it to capitalize on the current challenges facing the aerospace supply chain. In this article, we will explore FTAI Aviation’s strategic growth, its innovative approach to the jet engine overhaul business, and the potential impact of 3D printing (3DP) on its operations. Additionally, we’ll highlight recent 3D printing advancements within the aerospace industry, particularly from Boeing and Airbus, that could serve as benchmarks for FTAI Aviation’s future development.
FTAI Aviation’s Unique Business Model
FTAI Aviation, originally established by the global investment firm Fortress, has since spun off to become an independent, publicly traded company. This independence has allowed FTAI to pursue a specialized niche in the aviation industry—specifically, the overhaul and maintenance of jet engines using second-hand or non-OEM parts. FTAI takes in worn engines and swaps them for refurbished replacement ones. This model not only sets them apart from traditional aviation companies but also allows them to offer more cost-effective solutions to airlines that are struggling with the high costs and supply chain issues associated with new OEM parts.
One of FTAI Aviation’s most significant moves has been its acquisition of a 526,000-square-foot plant in Quebec, Canada, previously owned by Lockheed Martin. This acquisition marks the company’s third MRO (Maintenance, Repair, and Overhaul) facility, further expanding its capacity to service jet engines. Initially, FTAI focused on overhauling CFM56 engines, the workhorses of older Airbus A320 and Boeing 737 models. However, the company has since expanded into servicing International Aero Engines V2500 and has plans to further diversify its offerings to include other engine types.
The Expansion of 3D Printing in Aerospace
As FTAI Aviation continues to grow its jet engine business, it is worth considering the role that 3D printing could play in its future. The aviation industry has increasingly embraced 3D printing technology, recognizing its potential to revolutionize the manufacturing process by reducing costs, shortening production times, and allowing for greater customization.
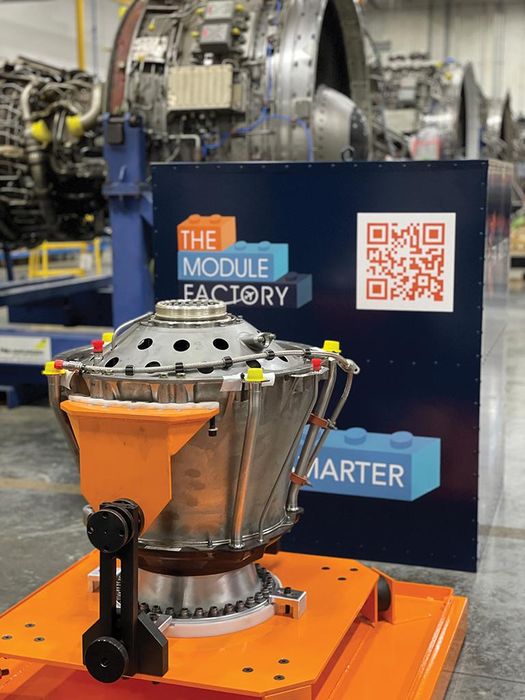
3D Printing in FTAI Aviation’s Future
While there is no direct evidence that FTAI Aviation currently utilizes 3D printing in its operations, the company is well-positioned to integrate this technology into its business model. With its focus on overhauling older engines using second-hand and non-OEM parts, 3D printing could allow FTAI to manufacture its own parts rather than relying on external suppliers. This would not only reduce costs but also provide greater control over the supply chain, a significant advantage given the ongoing supply chain disruptions in the aviation industry.
For example, as FTAI expands into servicing newer engine models, many of which contain OEM 3D-printed components, the ability to produce these parts in-house could be a game-changer. By investing in advanced 3D printing technology, FTAI could begin manufacturing its own replacement parts that meet or exceed OEM specifications, offering airlines a cost-effective alternative without compromising on quality or safety.
3D Printing Success Stories: Boeing and Airbus
To understand the potential impact of 3D printing on FTAI Aviation’s future, it is helpful to look at how industry giants like Boeing and Airbus have successfully integrated 3D printing into their operations.
Boeing:
Boeing has been a pioneer in the use of 3D printing, or additive manufacturing, in the aviation industry. One of the most notable examples is the 787 Dreamliner, which contains over 30 3D-printed parts. These components range from structural elements to air ducts, and even flight-critical parts like titanium brackets. The use of 3D printing has allowed Boeing to reduce the weight of the aircraft, leading to improved fuel efficiency and lower operating costs for airlines. Additionally, 3D printing has enabled Boeing to streamline its supply chain by reducing the need for multiple suppliers and decreasing production lead times.
Boeing has also been exploring the potential of 3D printing for maintenance and repair purposes. For example, the company has developed 3D-printed tools that can be used to repair damaged aircraft on-site, reducing the need for costly and time-consuming part replacements. This approach could be particularly valuable for FTAI Aviation as it continues to expand its MRO operations.
Airbus:
Airbus, another leader in the aviation industry, has also embraced 3D printing technology. The A350 XWB, for instance, features over 1,000 3D-printed parts, including brackets, ducts, and structural components. Airbus has used 3D printing to reduce the weight of the aircraft, improve fuel efficiency, and enhance overall performance.
One of Airbus’s most ambitious 3D printing projects is the production of titanium parts for its aircraft. These parts, produced using a technique called selective laser melting (SLM), are not only lighter than their traditionally manufactured counterparts but also stronger and more durable. Airbus has also been experimenting with the use of 3D printing to produce complex, customized parts on-demand, which could revolutionize the way aircraft are designed and built in the future.
In addition to its use in manufacturing, Airbus has also explored the potential of 3D printing for maintenance and repair. For example, the company has developed a mobile 3D printing unit that can be deployed to airports around the world to produce replacement parts on-site, significantly reducing downtime and costs for airlines.
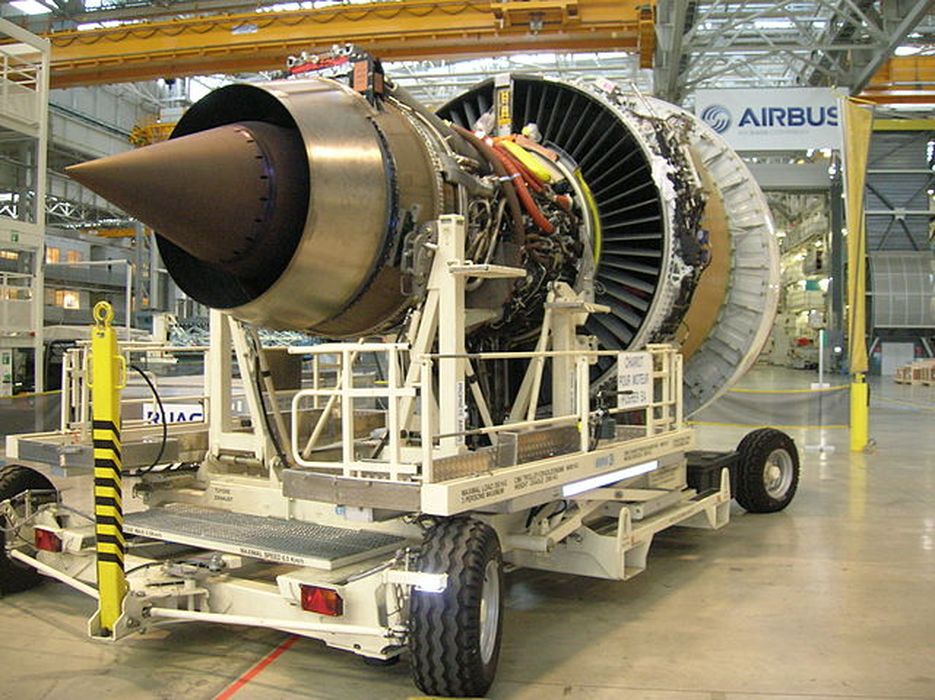
The Future of FTAI Aviation and 3D Printing
As FTAI Aviation continues to expand its jet engine overhaul business, the integration of 3D printing technology could play a crucial role in its future success. By leveraging 3D printing, FTAI could reduce its reliance on external suppliers, streamline its supply chain, and offer more cost-effective solutions to airlines. Additionally, the ability to produce high-quality replacement parts in-house could help FTAI differentiate itself from competitors and position itself as a leader in the MRO industry.
However, to fully realize the potential of 3D printing, FTAI Aviation will need to invest in the necessary technology and expertise. This could involve partnerships with established 3D printing companies or the development of in-house capabilities. Either way, the integration of 3D printing into FTAI’s operations could provide a significant competitive advantage in an industry that is increasingly looking for innovative solutions to meet the challenges of the twenty-first century.
We have previously written about HEICO and Wencor, and their strategic use of 3D printing for spare parts on Fabbaloo. FTAI is seizing the moment and can use 3D printing to maximize the opportunity.
The Research & Development Tax Credit
The now permanent Research and Development (R&D) Tax Credit is available for companies developing new or improved products, processes and/or software.
3D printing can help boost a company’s R&D Tax Credits. Wages for technical employees creating, testing and revising 3D printed prototypes can be included as a percentage of eligible time spent for the R&D Tax Credit. Similarly, when used as a method of improving a process, time spent integrating 3D printing hardware and software counts as an eligible activity. Lastly, when used for modeling and preproduction, the costs of filaments consumed during the development process may also be recovered.
Whether it is used for creating and testing prototypes or for final production, 3D printing is a great indicator that R&D Credit-eligible activities are taking place. Companies implementing this technology at any point should consider taking advantage of R&D Tax Credits.
Conclusion
FTAI Aviation’s unique business model and strategic expansion have positioned it to capitalize on the current challenges facing the aerospace industry. As the company continues to grow, the integration of 3D printing technology could play a key role in its future success. By taking inspiration from industry leaders like Boeing and Airbus, FTAI could leverage 3D printing to reduce costs, improve efficiency, and offer more competitive solutions to its customers. As the aviation industry continues to evolve, FTAI Aviation’s embrace of innovative technologies like 3D printing could be the key to its long-term success.