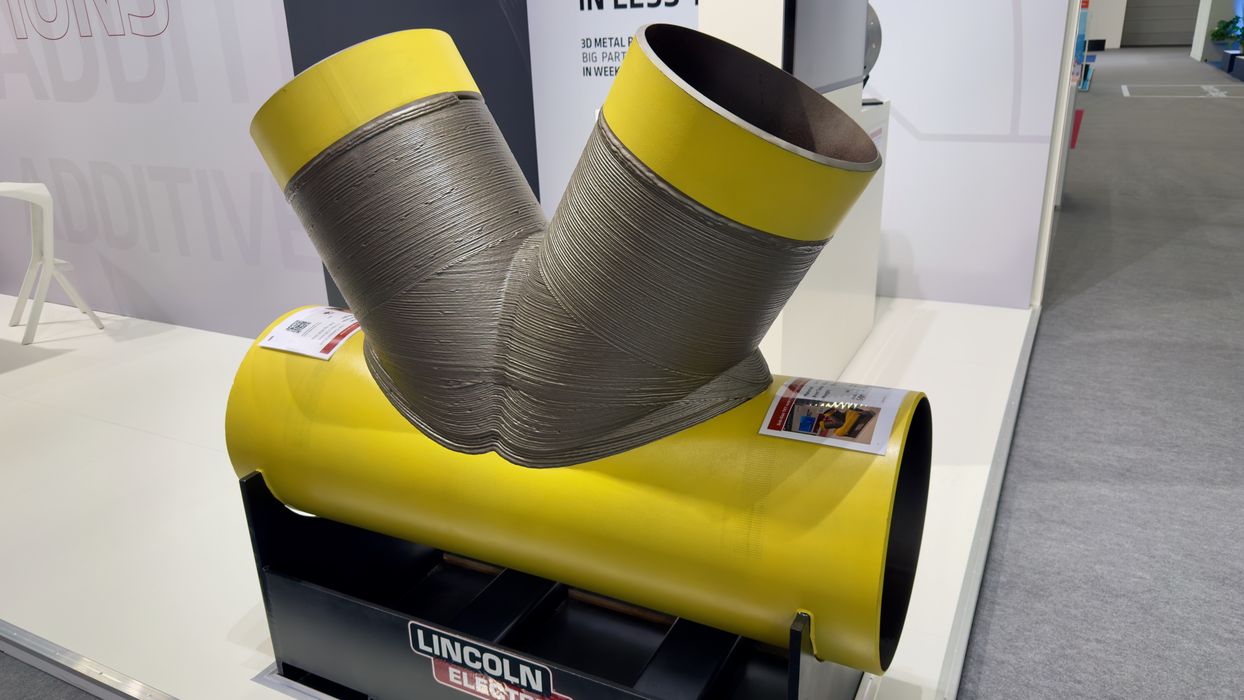
I had a chat with Lincoln Electric at Formnext and learned about an entirely new class of 3D print application.
You’ve probably never heard of Lincoln Electric before; they just happen to be the world’s largest welding company, 130 years old. In 2019 the company started experimenting with additive manufacturing by leveraging their welding capabilities.
After all, DED / WAAM 3D printing is simply welding on the end of a robotic arm. Currently they offer wire-arc AM systems, but intend on adding laser versions next year. These systems are quite large, with one able to print ten-tonne objects in a 3m wide build volume.
What exactly would you want to print at that scale? It turns out that Lincoln Electric has identified a very unusual and what appears to be highly productive application for metal 3D printing: wind turbine structures.
To understand this, let me explain how these work. We’re all familiar with the typical wind turbines you see from the highway: a single pole holds the turbine high in the air where it catches wind.
It’s quite different, however, for offshore wind turbines, which must reach all the way down to the seabed. This is not possible with a single pole. Instead, they use a complex tree-like structure of massive pipes to support the turbine from the seafloor.
This tree structure is made of huge pipes, but must be connected to each other at appropriate angles. Traditionally this has been done entirely manually by expert welders. They put down layer after layer of one-inch “weld metal” to form the joints in the structure.
As you might imagine, this has all kinds of challenges, including extremely long durations (apparently up to years), high expense due to labor costs, and an inability to scale because there simply aren’t enough qualified welders to do this work. It is complex enough that it cannot be automated.
This is one of the reasons that offshore wind projects take so long and why they can be so terribly expensive.
Enter Lincoln Electric’s new vision: prefab nodes. The idea is to use their metal AM technology to make joint structures that have the connections at the correct angles. Then standard pipes are attached to the joints in a much more straightforward manner — that can be automated.
By putting their structural engineers on the case, they were able to design joints that have as much as 70% less welding required using this approach. They were also able to 3D print bracing inside the joints, something that could not be done using manual techniques.
While these prints can be quite long — five days for the example at top — this is vastly less than the months or even years required to build these structures using traditional techniques.
This all adds up to a solution that could break though the time and cost barriers to achieve larger scale offshore wind energy, something very likely required to move away from fossil fuels.
Lincoln Electric representatives told us they have seen “great interest” from the wind industry, and they are continuing to develop the technology. However, one challenge is that the structures are truly enormous: the examples shown in the images here are only one-sixth of actual size. This will require Lincoln Electric to build a much larger machine to accommodate this size of part.
Via Lincoln Electric